- Placa
- Plasma
- Oxicombustible
Ventajas del montaje de la Antorcha magnetica
INNOVACIONES DESTACADAS
Debido a que tanto las antorchas de plasma como las de Oxi acetileno utilizan el mismo soporte, también comparten todas las ventajas que se derivan de las tecnologías integradas. Como, por ejemplo, el rápido Control de altura y True Volt.
NO NECESITA CALIBRACIÓN
Se trata de un montaje magnético con sólo 2 accionamientos perfectamente sintonizados, independiente de cualquier tipo de tolerancias y sin necesidad de calibración. Además de estas ventajas, el montaje magnético también influye en la velocidad del proceso de producción.

MONTAJE CON TORNILLO MAGNÉTICO
VISIÓN GENERAL DE LAS VENTAJAS
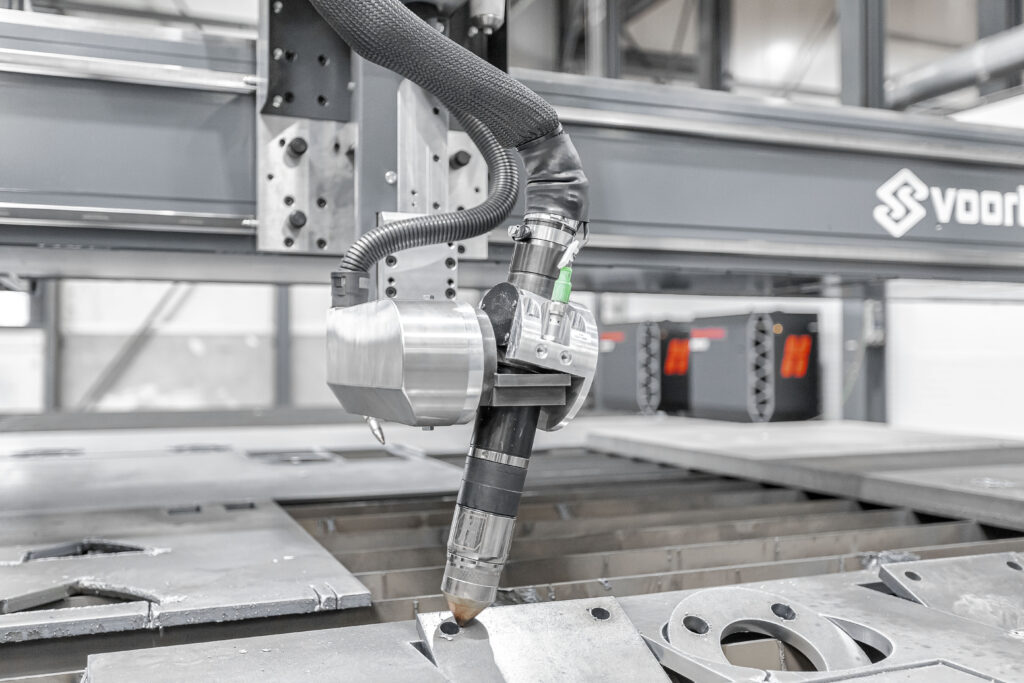