Vorteile der magnetischen halterung
GEMEINSAME INNOVATIONEN
Da sowohl das Plasma als auch die autogenen Schneidbrenner dieselbe Halterung verwenden, teilen sie auch alle Vorteile der eingebauten Technologien. Zum Beispiel die schnelle Höhensteuerung und True Volt.
KEINE KALIBRIERUNG ERFORDERLICH
Hierbei handelt es sich um eine magnetische Halterung mit lediglich 2 perfekt abgestimmten Antrieben, unabhängig von jeglichen Toleranzen. Kalibrierung ist nicht erforderlich. Neben diesen Vorteilen beeinflusst die magnetische Montage auch die Geschwindigkeit im Produktionsprozess.
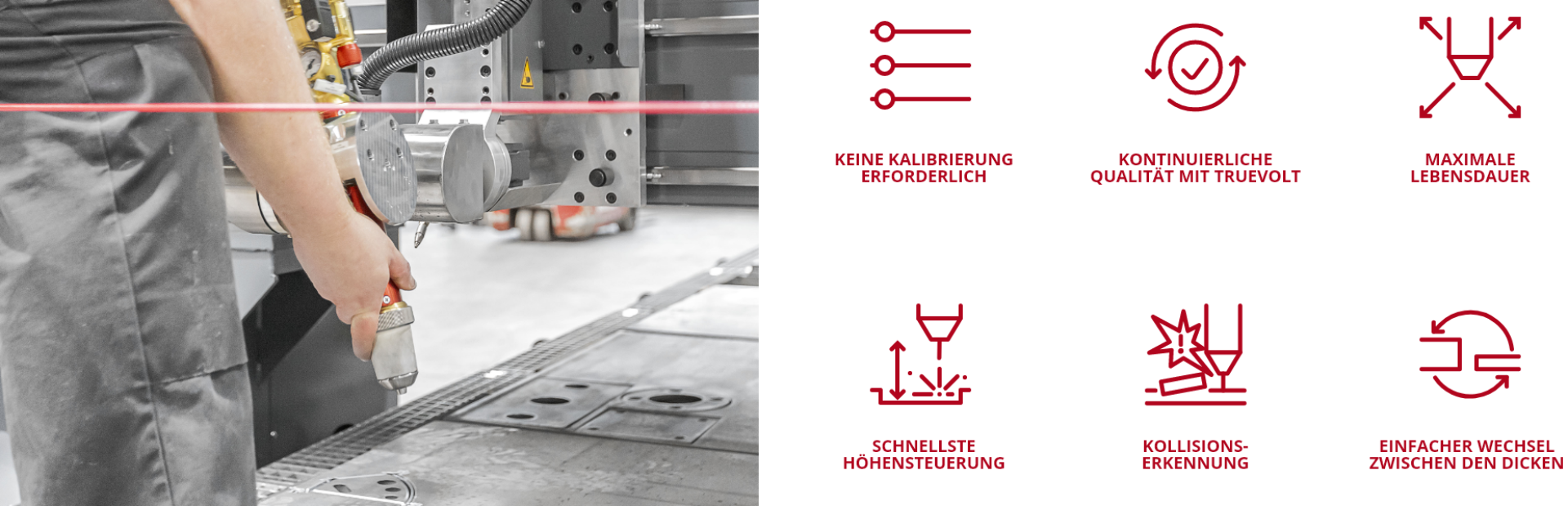
MAGNETSCHE HALTERUNG
DIE VORTEILE
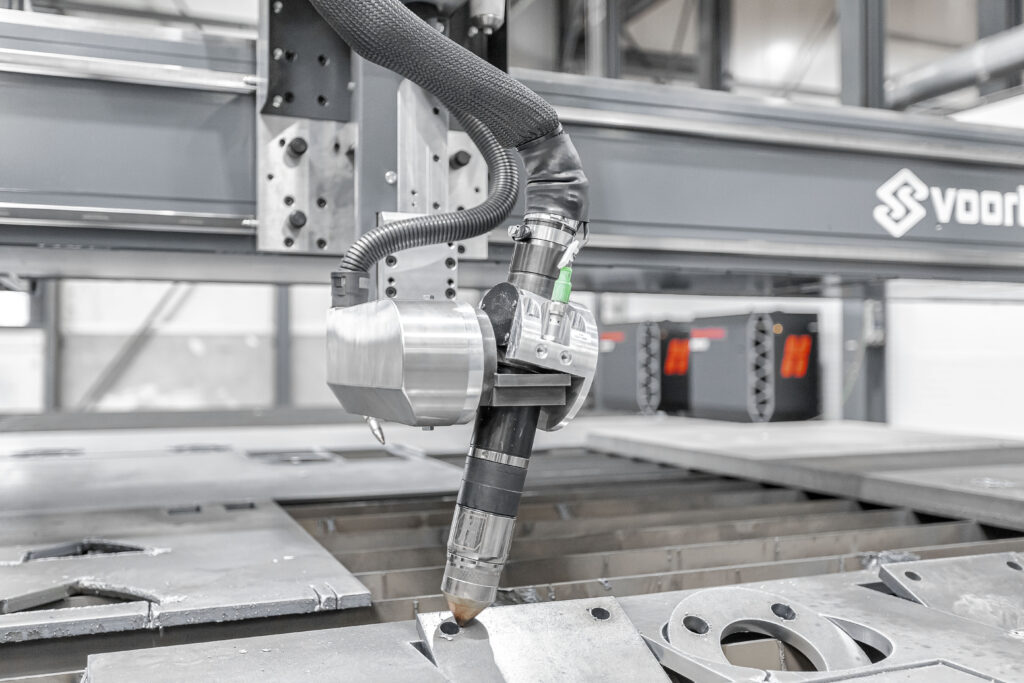
EINFACHER NEUSTART NACH EINER KOLLISION
Bei einer Kollision kann Ihr Bediener den Brenner mit einem Magnetsystem wieder montieren und die Maschine im Handumdrehen wieder in Betrieb nehmen. Mit der gleichen Leichtigkeit können Sie schnell zwischen verschiedenen Schnittdicken wechseln, indem Sie einfach die Brenner austauschen.