Revolutionizing Recycling Equipment Manufacturing
Bollegraaf's Success with Voortman V310
Testimonial Bollegraaf Recycling Solutions
- Location:
- Staff:
- Recycling systems installed:
- Machine:
- Appingedam, The Netherlands
- 300
- +4.000
- Voortman V310
“The V310's ability to drill and tap around 300 holes per baler, which previously required labor-intensive manual work, now saves us an impressive 3.5 days in construction time per baler.”
AN EFFICIENCY LEAP WITH THE VOORTMAN V310
For over six decades, Bollegraaf Recycling Solutions stands as one of the leaders in recycling installations and equipment, crafting solutions that turn today's waste into tomorrow's resources. With a team of 300 professionals spread across various locations, it’s all about innovation, sustainability and making an impact on how the world recycles. Their specialty? Creating efficient and impressive large balers.
“We really should have done this much earlier!” explained Pascall de Boer – Team lead CNC Programming at Bollegraaf - enthusiastically. He was referring to the purchase of their Voortman V310 plate drilling and cutting machine with a 24 meter long cutting bed. It is almost unbelievable that less than four years ago they were doing all the marking, drilling and tapping by hand. Of course, the dedication to craftsmanship was there, but the time it took was immense.
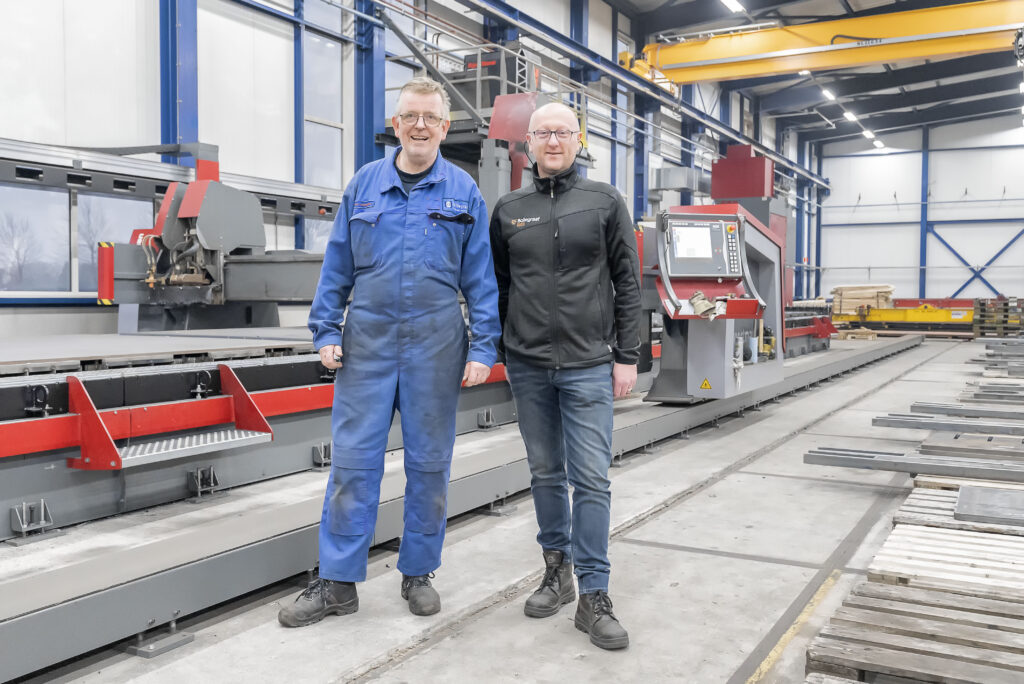
AUTOMATION: A TOTAL GAME-CHANGER
Pascall experienced firsthand the transition from manual to automated processes. The V310 quickly proved to be a game-changer, transforming the way Bollegraaf operates, significantly boosting their efficiency and productivity. “The V310's ability to drill and tap around 300 holes per baler, which previously required labor-intensive manual work, now saves us an impressive 3.5 days in construction time per baler.”
Beyond automating drilling, the machine also handles text and location markings seamlessly. “In the past, it was all marked manually and now that just comes off the machine, ready to go.” It saves Bollegraaf a lot of time in the construction department and ensures precision that manual methods couldn't achieve.
On top of that is the machine’s 3D bevel cutting head significantly improves precision, allowing for spot-on bevel cuts without programming or operator knowledge. “The machine runs fully automatically. After setup in SigmaNEST, the machine takes over the data and runs smoothly. Easy peasy!”
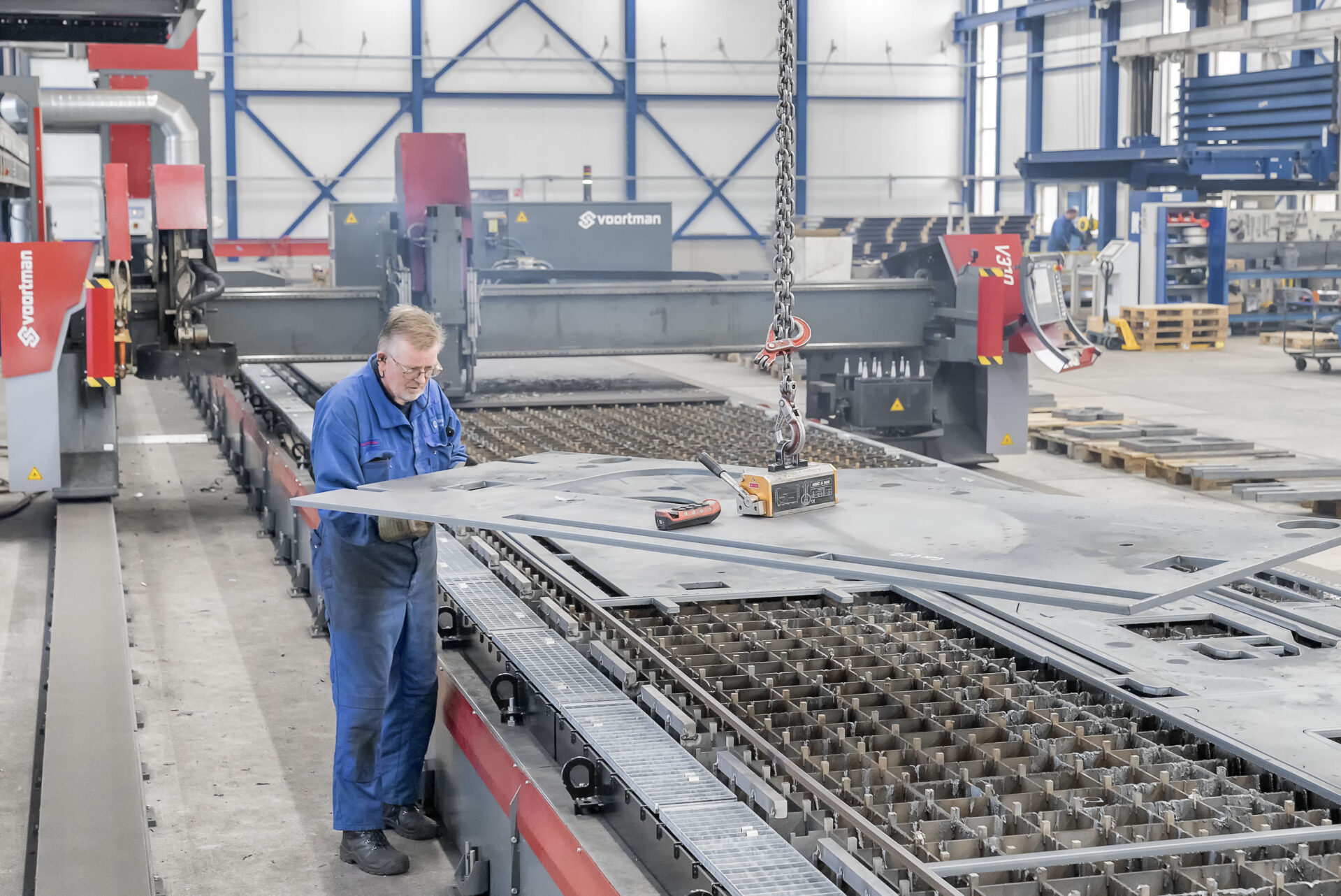
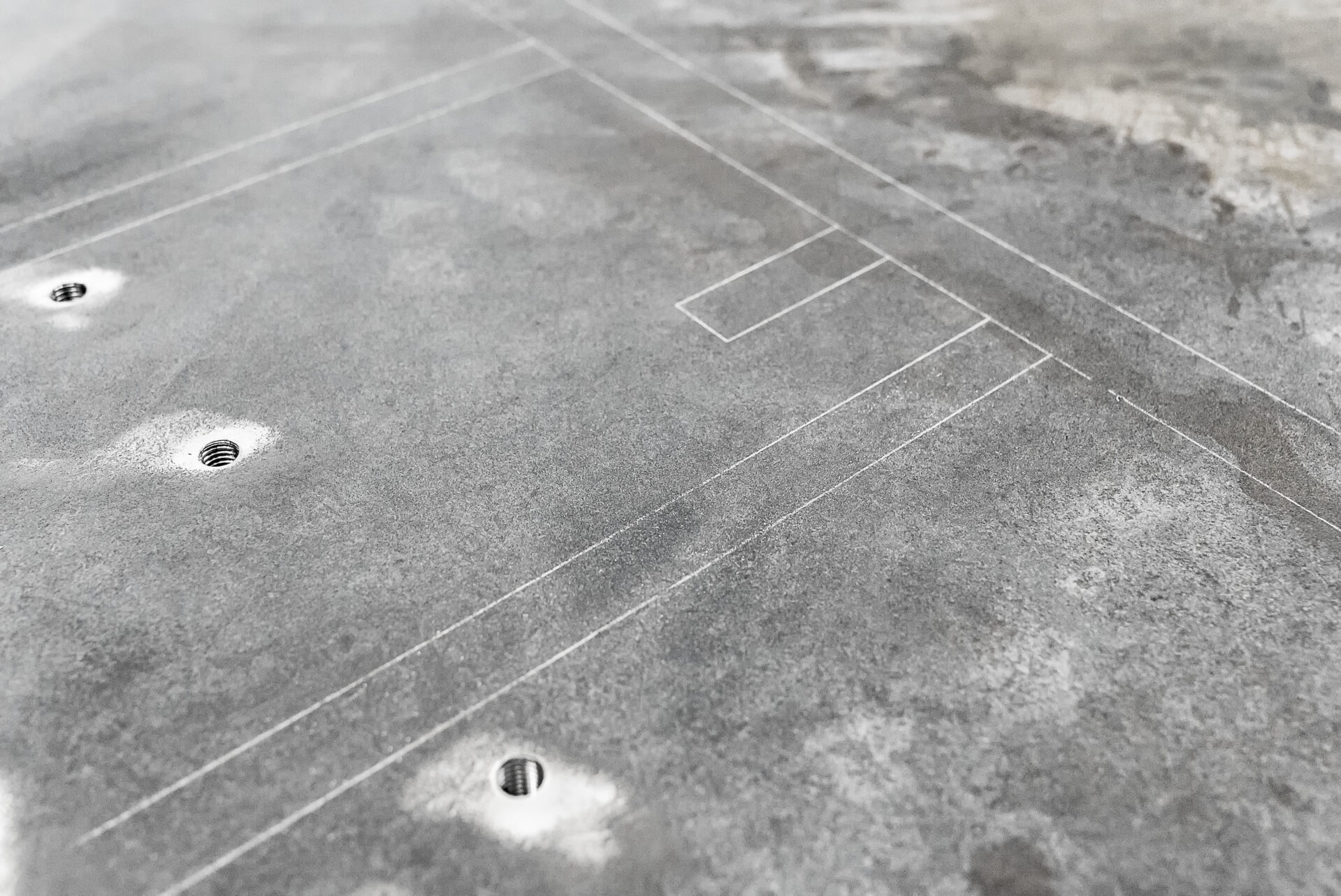
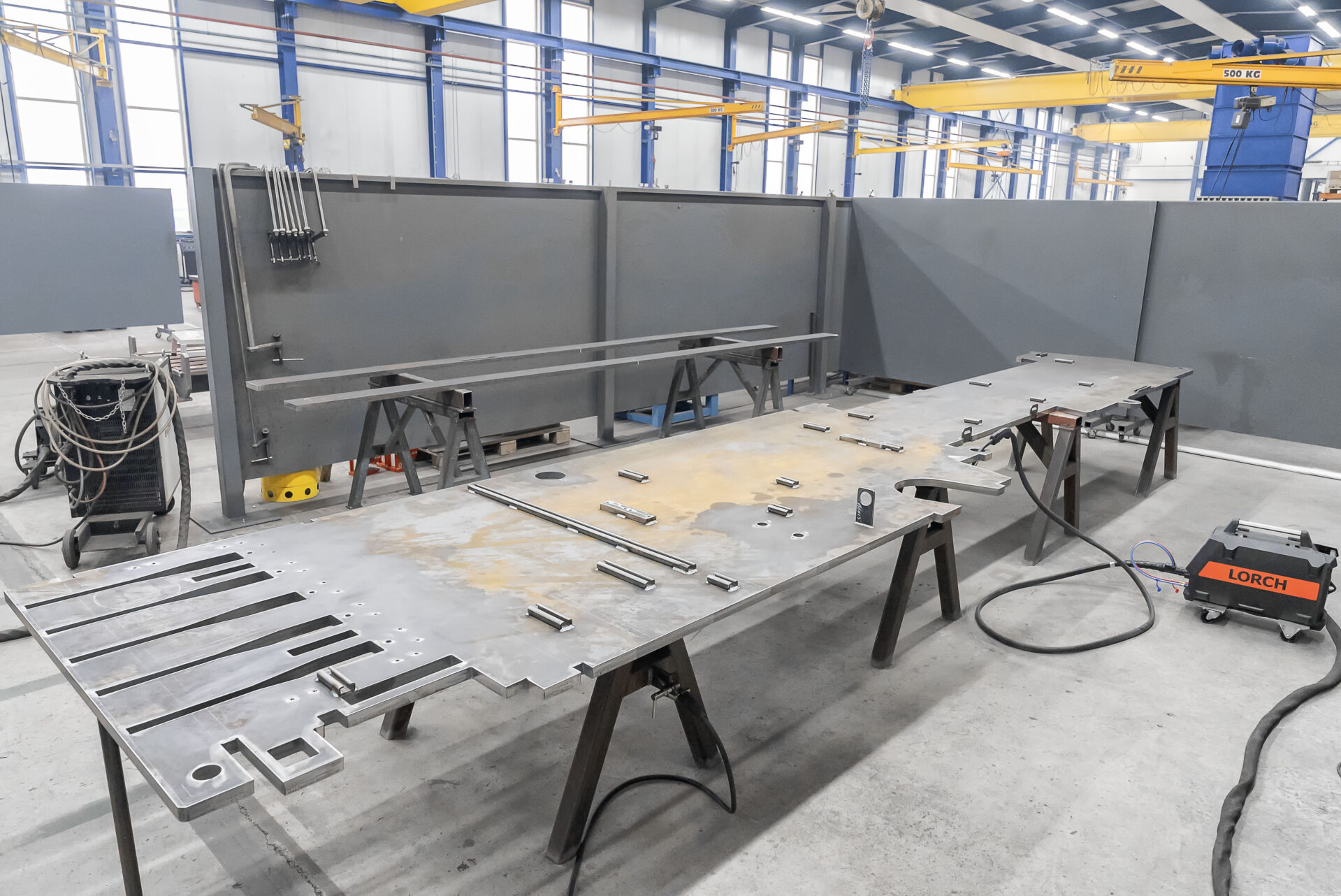
Plate loading and unloading can be done while the machine is still processing at another section of the table.
The V310 automatically produces high-quality drilled and tapped holes, along with precise layout markings.
A section of the baler frame has been assembled, with layout markings guiding the placement of parts.
PRECISION ON DEMAND: MASTERING JUST-IN-TIME AND FIRST-TIME-RIGHT
The V310 is all about creating top-notch parts with perfect cuts and holes, making sure everything fits just right. This means fewer mistakes, less tweaking during assembly. And that is exactly what they want, because they strive for 'First-Time-Right’ production. It eliminates the need for test products and prevents returns of faulty parts.
This approach aligns perfectly with their ‘Just-In-Time’ production strategy. They're skipping the inventories and going straight to delivering products exactly when the assembly team needs them for a specific customer order.
And guess what? The demand from customers just keeps on growing...
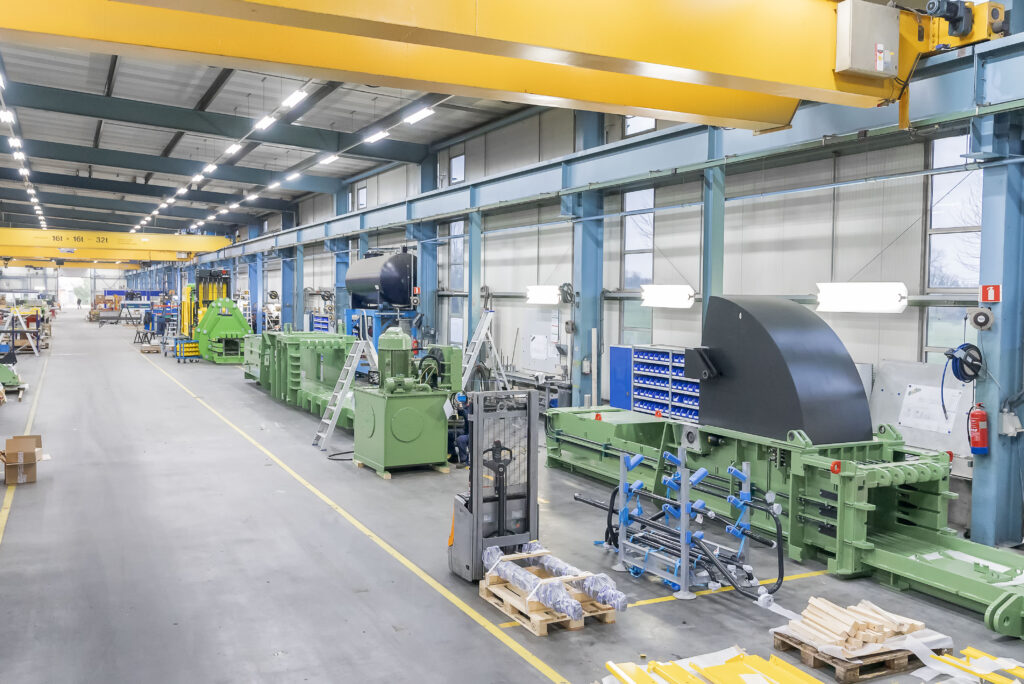
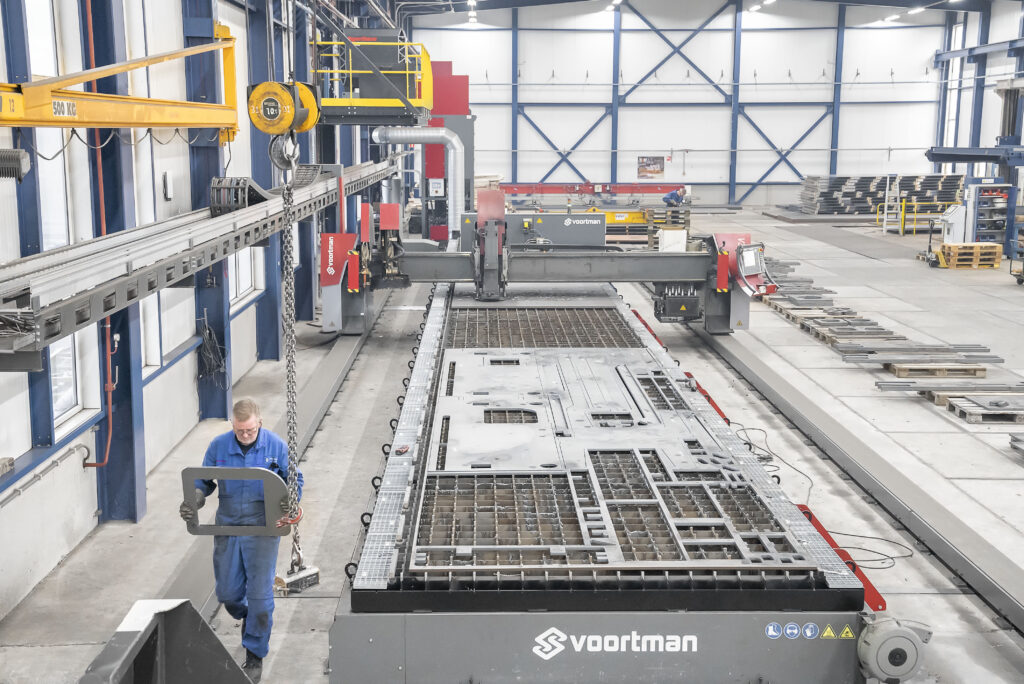
THE SECRET BEHIND SMOOTH AND EFFICIENT JOB TO JOB TRANSITIONS
The company's decision to utilize a 24-meter long cutting bed, capable of loading there two primary plate sizes for a baler (13 meter and 8 meter), facilitates uninterrupted operation and boosting daily output. The machine switches between plates like a pro, no downtime! Running on its own for 8 hours, it slices through plates ranging from 15 to 60 mm thick using both oxy-fuel and plasma cutting.
A valuable addition was the introduction of a supplementary 20-piece tool changer, developed in collaboration with Voortman, which is added to the standard 10 tools within the machine. “There are so many holes in the baler that we wouldn't want to change manually”. Manual tool changes and potential downtime are now minimized and job to job transitions are running smooth.
UNMANNED RUNNING WITH A MACHINE THAT NEVER SLEEPS
Unmanned operations take the spotlight with a machine that operates around the clock without rest. “We strive to maximize our efficiency by utilizing the machine to its fullest potential, even beyond our regular working hours.” A unique blow chip function, again developed in collaboration with Voortman, blows off chips and debris, allowing for drilling, tapping, and marking to proceed without human supervision. “You can drill and tap after working hours and then resume cutting in the morning with a simple push of a button."
EASY WORKING AT THE SHOPFLOOR
Working on the shop floor is a breeze! The low machine X-rail makes things easier for operators, no more high steps to tackle. A notable improvement from their previous model that required more effort and posed safety risks.
Color Offload further streamlines the workflow by providing visual feedback of which parts belong to which order and identifying faulty parts early in the process. “On the shop floor, operators can flag incorrect parts, automatically triggering a new nesting to recreate the part”. Real-time feedback on tool status and job details aid operators in efficient planning and maintenance. "The display of processing times for each nest directly on the machine simplifies scheduling, empowering operators to prioritize tasks for optimal efficiency and machine utilization."
FORWARD TOGETHER: A PARTNERSHIP BUILT ON FORWARD-THINKING AND TRUST
Choosing Voortman was about more than just machinery; it was about partnership. Bollegraaf had an extensive tour at the Voortman headquarters and very complex shapes were cut as test products. This test passed with flying colors, but Voortman's local presence and the sense of connection felt by the team set Voortman apart from others. "We all had the feeling that we were actually dealing with a brother or sister in terms of the company. We just clicked perfectly." Beyond the evident logistical and cultural benefits, Voortman's service quality stood out. “The service is excellent. One call and you have an immediate answer. Planning is also always just right. Word is word. Deed is deed.”
The V310 has really changed things up for Bollegraaf's production process. Less manual work, more precision, and top-notch quality for their balers. Their investment shows how dedicated they are to innovation and efficiency, keeping Bollegraaf at the forefront of the recycling equipment industry.
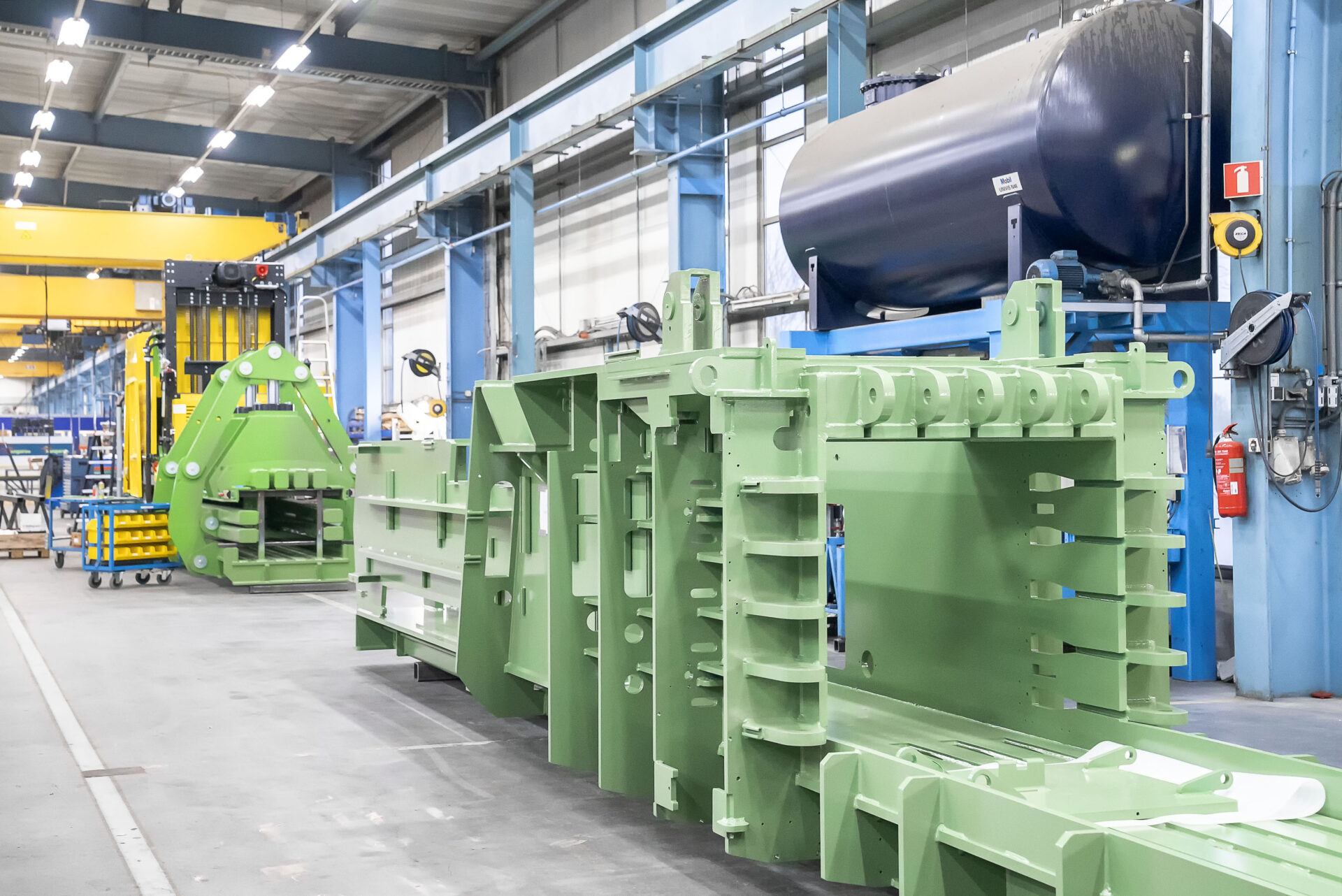