Kundenbericht Bollegraaf Recycling Solutions
- Standort:
- Personal:
- Installierte Recyclingsysteme:
- Maschine:
- Appingedam, Die Niederlande
- 300
- +4.000
- Voortman V310
"Die Fähigkeit des V310, rund 300 Bohren und Gewindeschneiden pro Ballenpresse durchzuführen, was früher arbeitsintensive Handarbeit erforderte, spart uns jetzt beeindruckende 3,5 Tage Bauzeit pro Ballenpresse."
EIN LEISTUNGSSPRUNG MIT DEM VOORTMAN V310
Seit mehr als sechs Jahrzehnten ist Bollegraaf Recycling Solutions einer der führenden Anbieter von Recyclinganlagen und -ausrüstungen und entwickelt Lösungen, die den Abfall von heute in die Ressourcen von morgen verwandeln. Mit einem Team von 300 Fachleuten an verschiedenen Standorten dreht sich bei Bollegraaf alles um Innovation, Nachhaltigkeit und einen Einfluss auf die Art und Weise, wie die Welt recycelt. Ihre Spezialität? Die Entwicklung effizienter und beeindruckender Großballenpressen.
"Wir hätten das wirklich schon viel früher tun sollen", erklärt Pascall de Boer - Teamleiter CNC-Programmierung bei Bollegraaf - begeistert. Er bezog sich dabei auf die Anschaffung der Voortman V310 Bohr- und Schneidemaschine für Bleche mit einem 24 Meter langen Schneidebett. Es ist kaum zu glauben, dass man vor weniger als vier Jahren noch alles Markieren, Bohren und Gewindeschneiden von Hand gemacht hat. Natürlich war das handwerkliche Engagement vorhanden, aber der Zeitaufwand war immens.
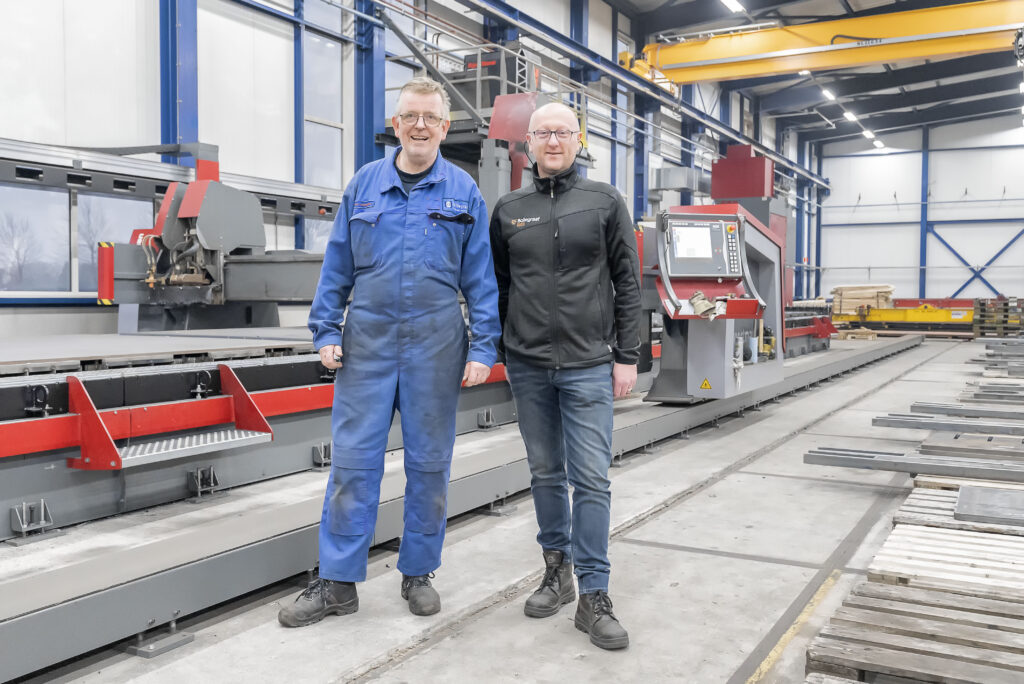
AUTOMATISIERUNG: EIN VÖLLIG NEUER ANSATZ
Pascall erlebte den Übergang von manuellen zu automatisierten Prozessen aus erster Hand. Das V310 erwies sich schnell als ein Wendepunkt, der die Arbeitsweise von Bollegraaf veränderte und die Effizienz und Produktivität erheblich steigerte. "Die Fähigkeit des V310, rund 300 Bohren und Gewindeschneiden pro Ballenpresse durchzuführen, was früher arbeitsintensive manuelle Arbeit erforderte, spart uns jetzt beeindruckende 3,5 Tage Bauzeit pro Ballenpresse."
Die Maschine automatisiert nicht nur das Bohren, sondern kann auch Text und Markierungen nahtlos verarbeiten. "In der Vergangenheit wurde alles manuell markiert, jetzt kommt das einfach von der Maschine und ist sofort einsatzbereit." Das spart Bollegraaf viel Zeit in der Konstruktionsabteilung und gewährleistet eine Präzision, die mit manuellen Methoden nicht erreicht werden könnte.
Hinzu kommt, dass der 3D-Fasenschneiden-Kopf der Maschine die Präzision erheblich verbessert und punktgenaue Fasenschnitte ohne Programmier- oder Bedienerkenntnisse ermöglicht. "Die Maschine läuft vollautomatisch. Nach dem Einrichten in SigmaNEST übernimmt die Maschine die Daten und läuft reibungslos. Easy peasy!"
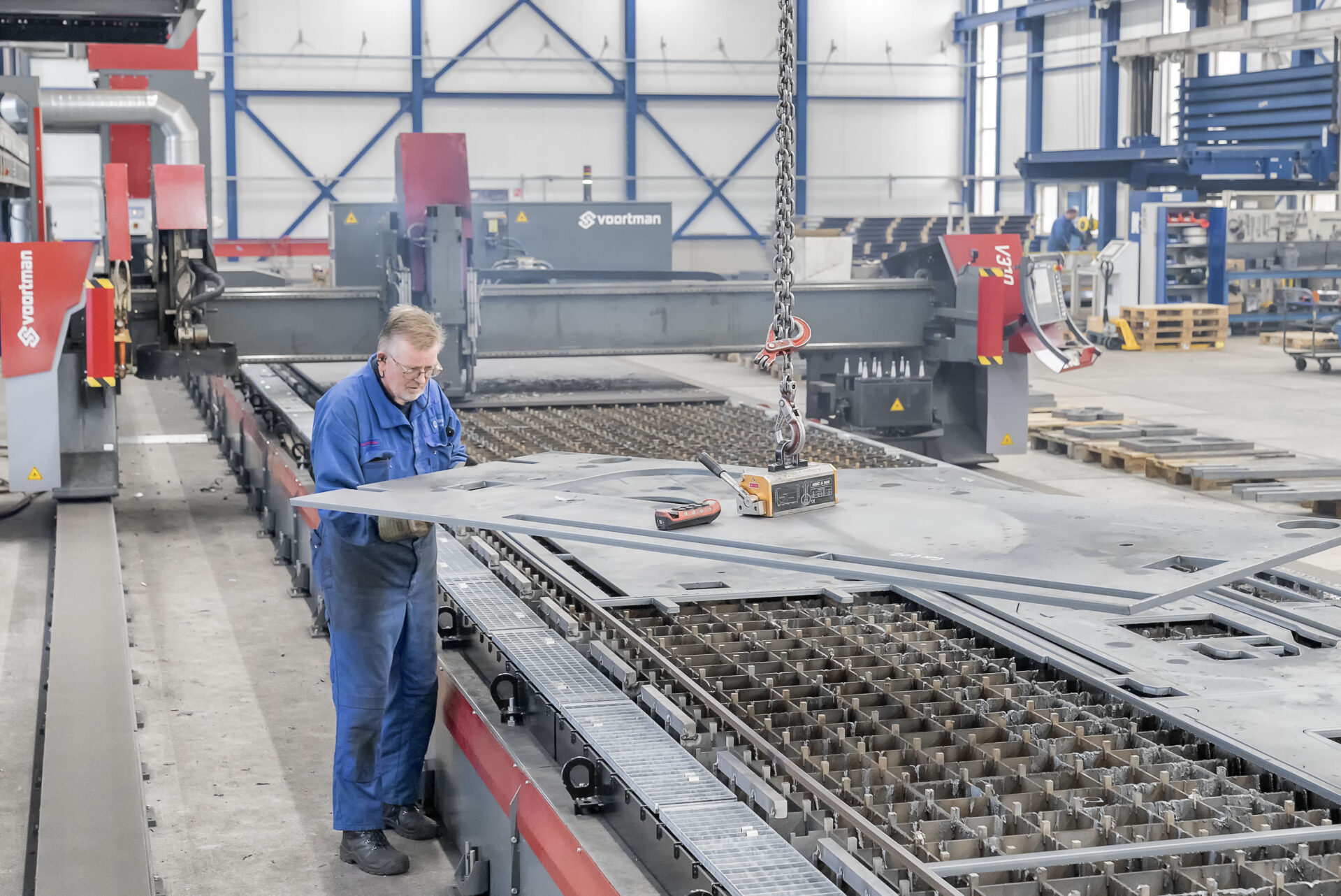
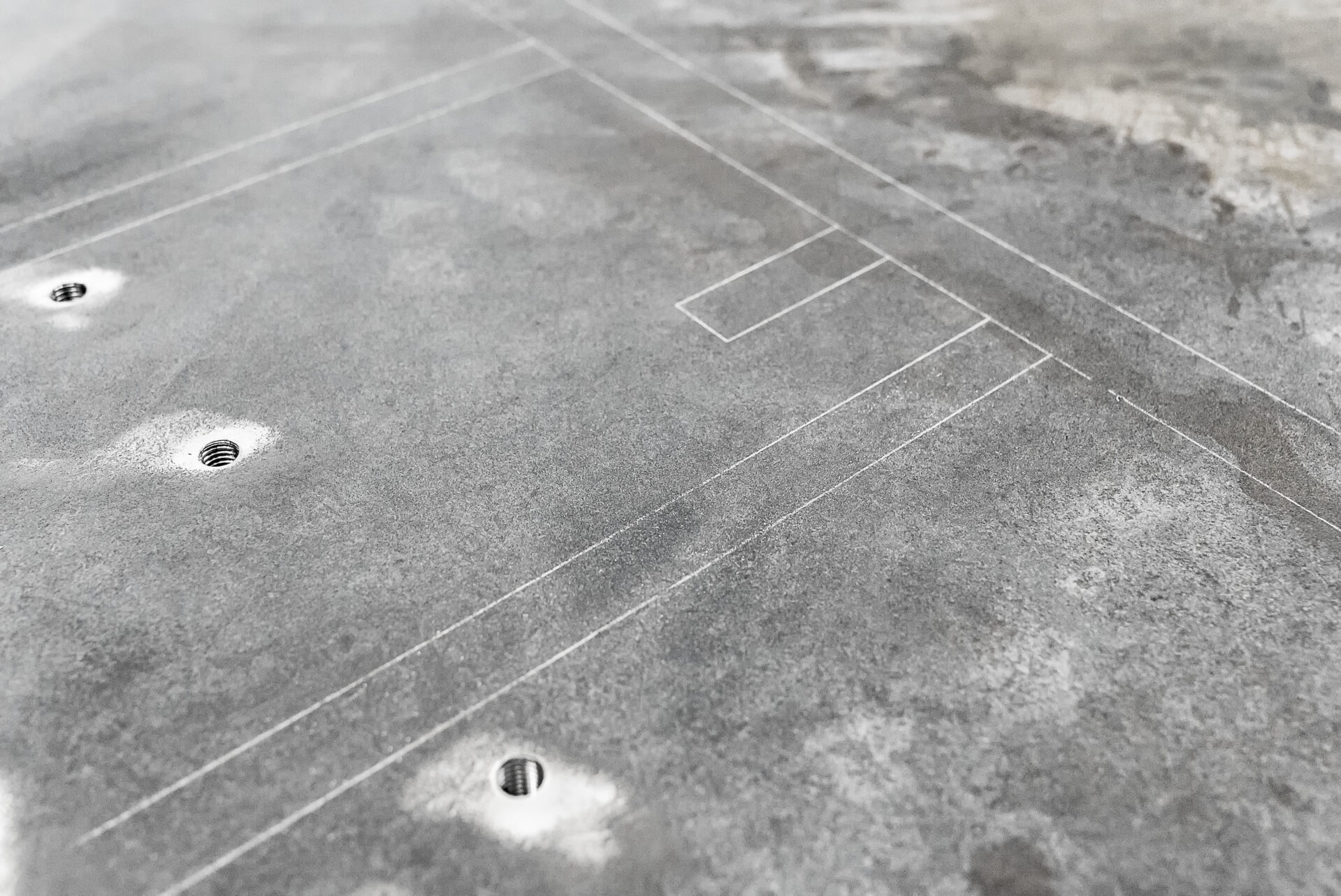
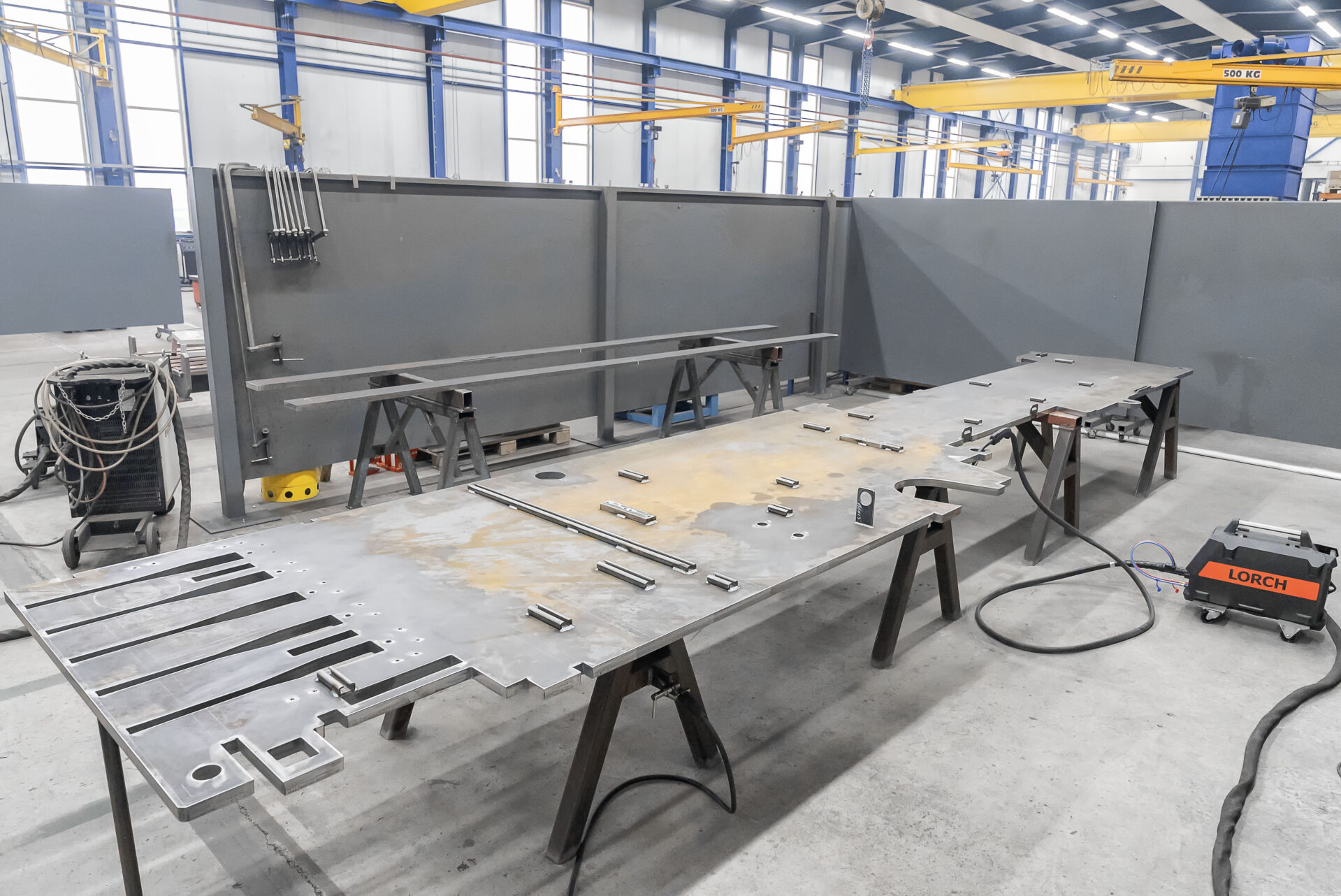
Das Be- und Entladen der Bleche kann erfolgen, während die Maschine an einer anderen Stelle des Tisches noch bearbeitet wird.
Das V310 erzeugt automatisch hochwertige Bohrungen und Gewindebohrungen sowie präzise Markierungen.
Ein Teil des Ballenpressenrahmens wurde zusammengebaut, wobei Layoutmarkierungen die Platzierung der Teile vorgeben.
PRÄZISION AUF ABRUF: BEHERRSCHUNG VON JUST-IN-TIME UND FIRST-TIME-RIGHT
Beim V310 dreht sich alles um die Herstellung erstklassiger Teile mit perfekten Schnitten und Löchern, die sicherstellen, dass alles genau richtig sitzt. Das bedeutet weniger Fehler und weniger Nacharbeit bei der Montage. Und das ist genau das, was sie wollen, denn sie streben eine "First-Time-Right"-Produktion an. Dadurch werden Testprodukte überflüssig und Rücksendungen fehlerhafter Teile vermieden.
Dieser Ansatz passt perfekt zu ihrer "Just-in-Time"-Produktionsstrategie. Die Lagerhaltung wird übersprungen und die Produkte werden genau dann geliefert, wenn das Montageteam sie für einen bestimmten Kundenauftrag benötigt.
Und wissen Sie was? Die Nachfrage der Kunden steigt weiter an...
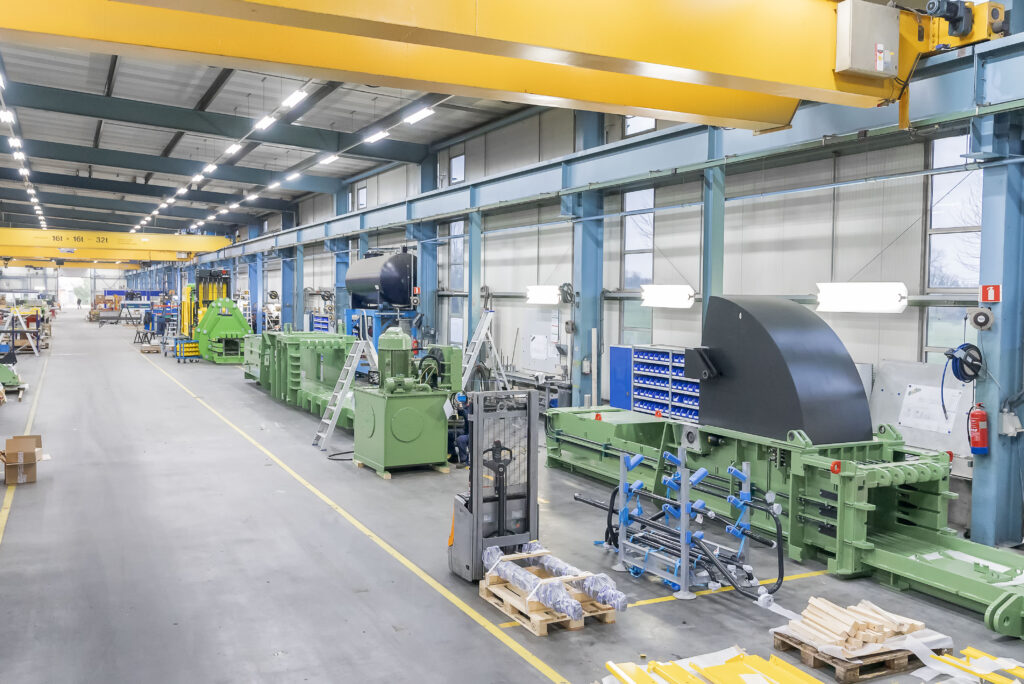
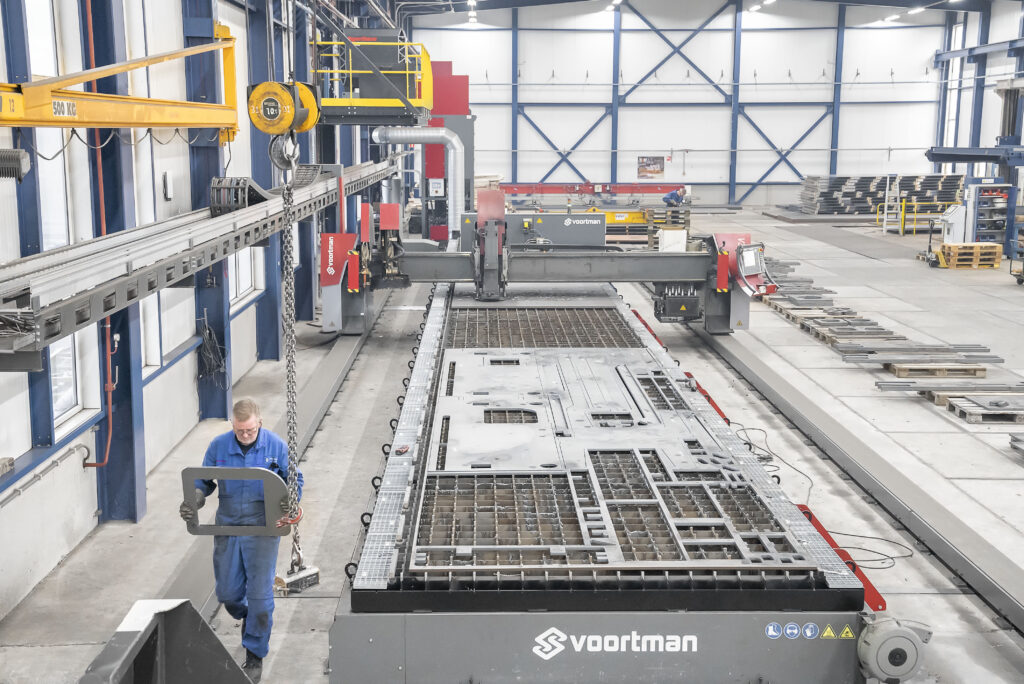
DAS GEHEIMNIS EINES REIBUNGSLOSEN UND EFFIZIENTEN ÜBERGANGS VON EINEM ARBEITSPLATZ ZUM ANDEREN
Die Entscheidung des Unternehmens, ein 24 Meter langes Schneidbett zu verwenden, das zwei primäre Blechgrößen für eine Ballenpresse (13 Meter und 8 Meter) aufnehmen kann, ermöglicht einen unterbrechungsfreien Betrieb und eine Steigerung der täglichen Leistung. Die Maschine wechselt zwischen den Blechen wie ein Profi, ohne Ausfallzeiten! Sie läuft 8 Stunden lang von allein und schneidet Bleche mit einer Dicke von 15 bis 60 mm sowohl mit autogenem Brennstoff als auch mit Plasma.
Eine wertvolle Ergänzung war die Einführung eines zusätzlichen 20-teiligen Werkzeugwechslers, der in Zusammenarbeit mit Voortman entwickelt wurde und der zu den standardmäßigen 10 Werkzeugen in der Maschine hinzukommt. "Es gibt so viele Löcher in der Ballenpresse, die wir nicht manuell wechseln wollen". Manuelle Werkzeugwechsel und potenzielle Ausfallzeiten werden nun auf ein Minimum reduziert, und die Übergänge zwischen den Aufträgen verlaufen reibungslos.
UNBEMANNTES LAUFEN MIT EINER MASCHINE, DIE NIEMALS SCHLÄFT
Bei einer Maschine, die rund um die Uhr ohne Pause arbeitet, steht der mannlose Betrieb im Vordergrund. "Wir sind bestrebt, unsere Effizienz zu maximieren, indem wir das volle Potenzial der Maschine ausschöpfen, auch über unsere regulären Arbeitszeiten hinaus." Eine einzigartige Späneblasfunktion, die ebenfalls in Zusammenarbeit mit Voortman entwickelt wurde, bläst Späne und Ablagerungen ab, so dass Bohren, Gewindeschneiden und Markieren ohne menschliche Aufsicht erfolgen können. "Sie können nach der Arbeitszeit bohren und Gewinde schneiden und dann am Morgen mit einem einfachen Knopfdruck weitermachen."
EINFACHES ARBEITEN IN DER WERKSTATT
Die Arbeit in der Werkstatt ist ein Kinderspiel! Die niedrige X-Schiene der Maschine erleichtert den Bedienern die Arbeit, da keine hohen Stufen mehr zu überwinden sind. Eine bemerkenswerte Verbesserung gegenüber dem Vorgängermodell, das mehr Aufwand erforderte und Sicherheitsrisiken mit sich brachte.
Color Offload rationalisiert den Arbeitsablauf weiter, indem es eine visuelle Rückmeldung darüber gibt, welche Teile zu welchem Auftrag gehören und fehlerhafte Teile frühzeitig im Prozess identifiziert. "In der Werkstatt können die Bediener fehlerhafte Teile markieren, wodurch automatisch eine neue Verschachtelung ausgelöst wird, um das Teil neu zu erstellen. Echtzeit-Rückmeldungen über den Werkzeugstatus und Auftragsdetails helfen den Bedienern bei der effizienten Planung und Wartung. "Die Anzeige der Bearbeitungszeiten für jede Verschachtelung direkt an der Maschine vereinfacht die Planung und ermöglicht es den Bedienern, Aufgaben für optimale Effizienz und Maschinenauslastung zu priorisieren."
GEMEINSAM VORWÄRTS: EINE PARTNERSCHAFT, DIE AUF VORAUSDENKEN UND VERTRAUEN BERUHT
Bei der Entscheidung für Voortman ging es um mehr als nur um Maschinen; es ging um eine Partnerschaft. Bollegraaf machte einen ausführlichen Rundgang durch die Voortman-Zentrale, und es wurden sehr komplexe Formen als Testprodukte geschnitten. Dieser Test wurde mit Bravour bestanden, aber die lokale Präsenz von Voortman und das Gefühl der Verbundenheit, das das Team empfand, unterschieden Voortman von anderen. "Wir hatten alle das Gefühl, dass wir es in Bezug auf das Unternehmen mit einem Bruder oder einer Schwester zu tun hatten. Wir haben einfach perfekt zusammengepasst." Neben den offensichtlichen logistischen und kulturellen Vorteilen stach die Servicequalität von Voortman hervor. "Der Service ist hervorragend. Ein Anruf und Sie haben sofort eine Antwort. Die Planung ist auch immer genau richtig. Wort ist Wort. Taten sind Taten."
Das V310 hat den Produktionsprozess bei Bollegraaf wirklich verändert. Weniger manuelle Arbeit, mehr Präzision und erstklassige Qualität für ihre Ballenpressen. Die Investition zeigt, wie sehr sich Bollegraaf der Innovation und Effizienz verschrieben hat, und sorgt dafür, dass das Unternehmen weiterhin an der Spitze der Recyclingbranche steht.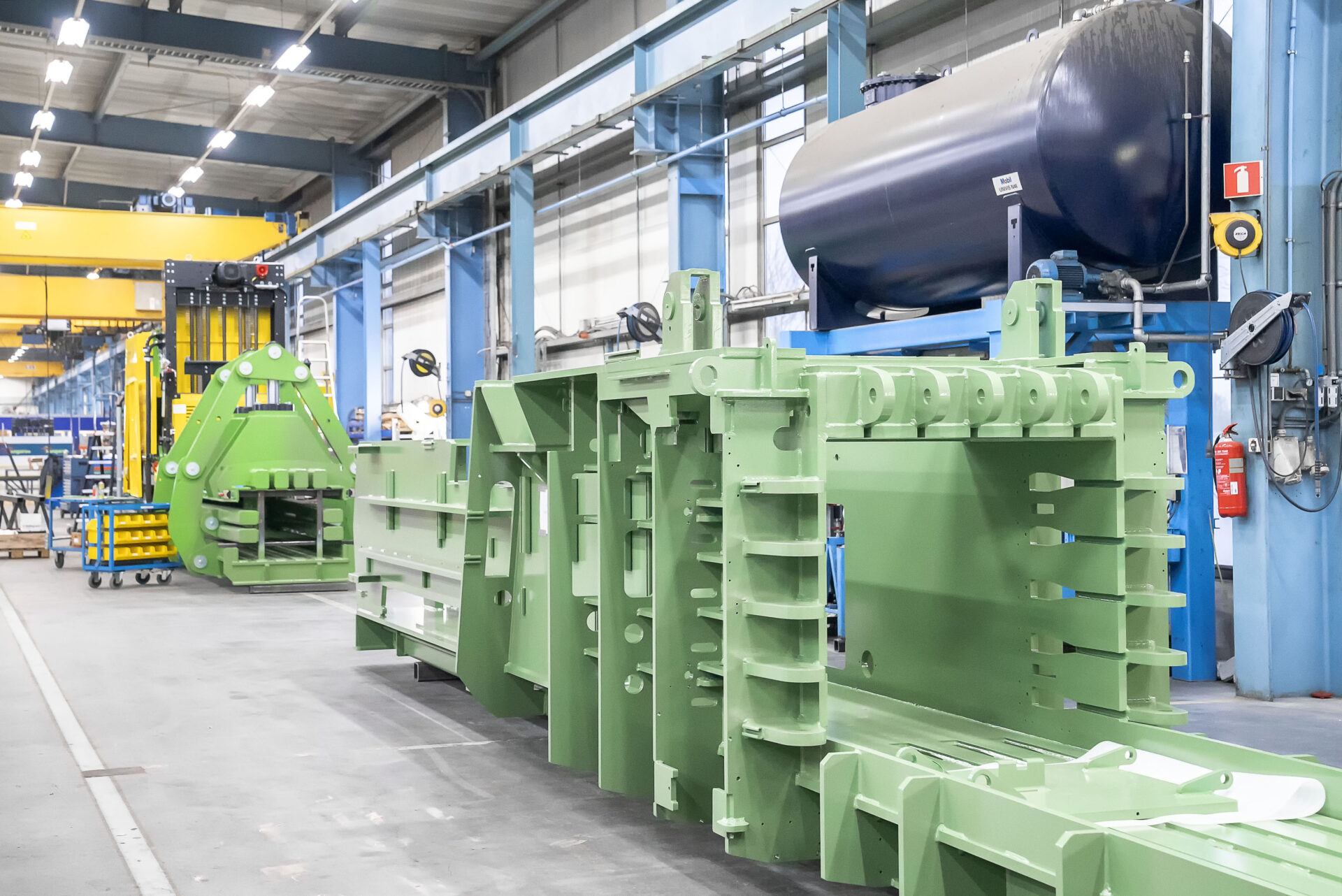