Testimonial Canam-Bridges
- Location:
- Facilities:
- Staff:
- Annual Capacity:
- Quebec City - Canada
- 12 plans
- 3.500 employees
- 381.000 tons
"The initial quality was outstanding, with great attention to detail in all the mechanical assemblies. This emphasis on quality is crucial in ensuring the longevity and reliability of the machinery, which is essential in the demanding field of bridge construction"
STURDY BRIDGES WITH QUALITY ASSURANCE
In the world of engineering, few projects are as demanding and intricate as bridge construction. Félix Bélanger, a project engineer at Canam-Bridges (part of Canam-Group), sheds light on the complexities and achievements of his company in this field. With three years at Canam, Félix has seen the company evolve and take on challenging projects across the globe.
Canam-Bridges has been part of significant projects, including the renowned Champlain Bridge in Montreal. Félix proudly mentions their current major project, the Gordie Howe International Bridge, connecting Windsor to Detroit. Emphasizing their commitment to quality, he states, "We make no compromise on quality. Every part must be 100% within the standards we've set in the industry."
The process of bridge building at Canam is meticulous and precise. Félix describes the journey of a steel plate turning into a part of a bridge: "It starts with a full metal plate that we receive by train, which eventually leaves as a complete girder or box. We handle everything from cutting to assembly and painting here on-site." This integrated process ensures quality control and efficiency.
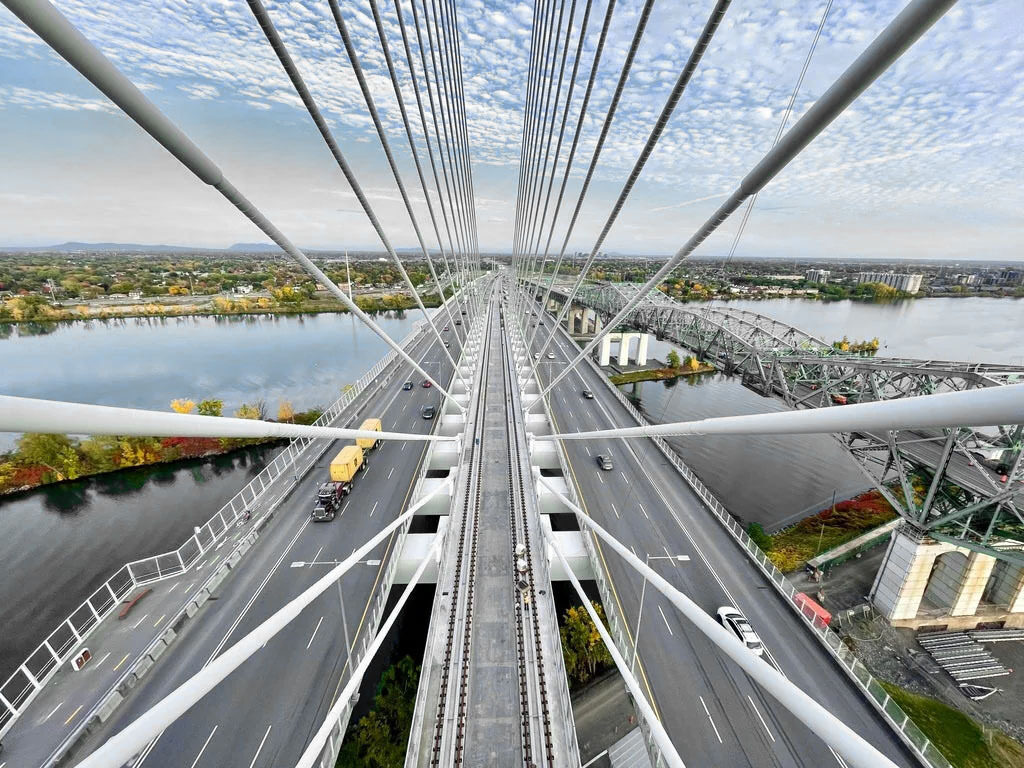
Canam-Bridges has been part of significant projects, including the renowned Champlain Bridge in Montreal
AUTOMATION: A GAME CHANGER
At the heart of Canam-Bridges' innovation is a beam line consisting of a V633 drill unit and a VB1250 saw. Félix explains the significance of this setup: "One of the main benefits is the ability to machine copes inside of the beam, saving a lot of time that would otherwise be spent on manual operations." This technological advancement streamlines the process, reducing reliance on manual labor for tasks like marking, cutting, and grinding.
The automation of this system is a key advantage, as Félix notes: "We can accumulate material outside of the drill and feed them into the saw as needed. This gives us great versatility and optimizes our operations." The automation not only speeds up the process but also allows for more precise and efficient work.
With the machine's automatic capabilities, the role of operators has evolved. "Operators are now more oriented towards working with the machine. The Human-Machine Interface (VACAM) provides a clear visual indication of the machine's layout and the status of different parts," says Félix. This change has led to less need for manual intervention and increased overall efficiency.
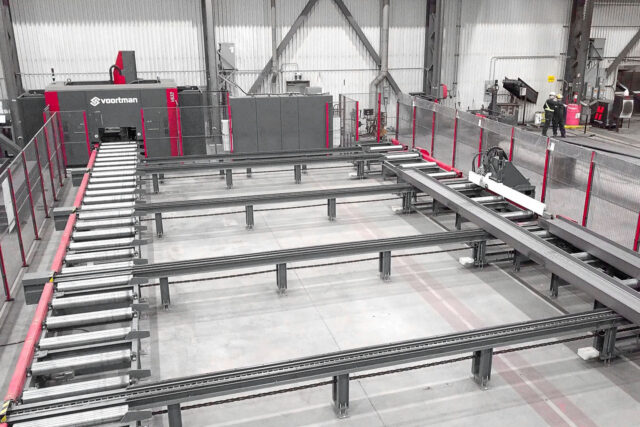
At the heart of Canam-Bridges' innovation is a beam line consisting of a V633 drill unit and a VB1250 saw.
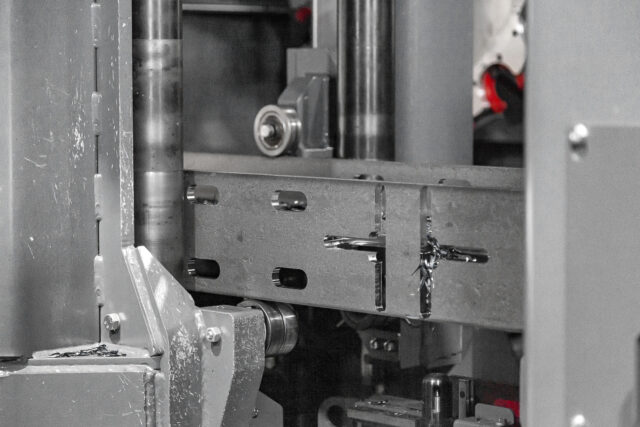
One of the main benefits is the ability to machine copes inside of the beam.
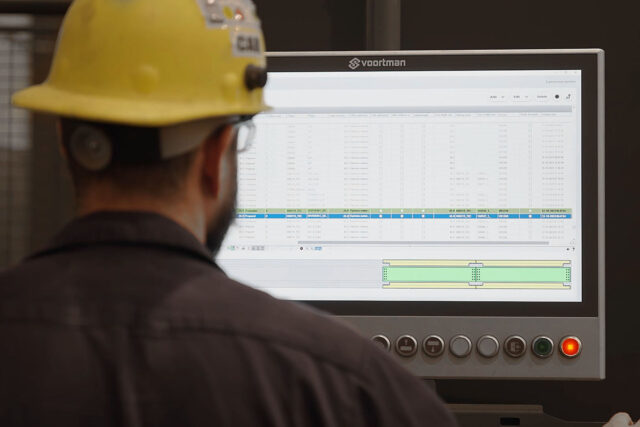
Operators are now more oriented towards working with the machine.
SUB-AXIS MACHINING FOR GREATER VERSATILITY
Félix highlights the independent sub-axes of the Voortman V633: "By not having the part move while machining, we can machine more than one side at a time. This adds great versatility, especially for larger or longer machinery, as it allows us to move the beam while machining."
The machine's impact on the quality of parts is significant. "It delivers outstanding quality in the parts we need to produce," Félix asserts. The machinery's adaptability is also crucial, as it can handle various materials and shapes, catering to the unique needs of each project.
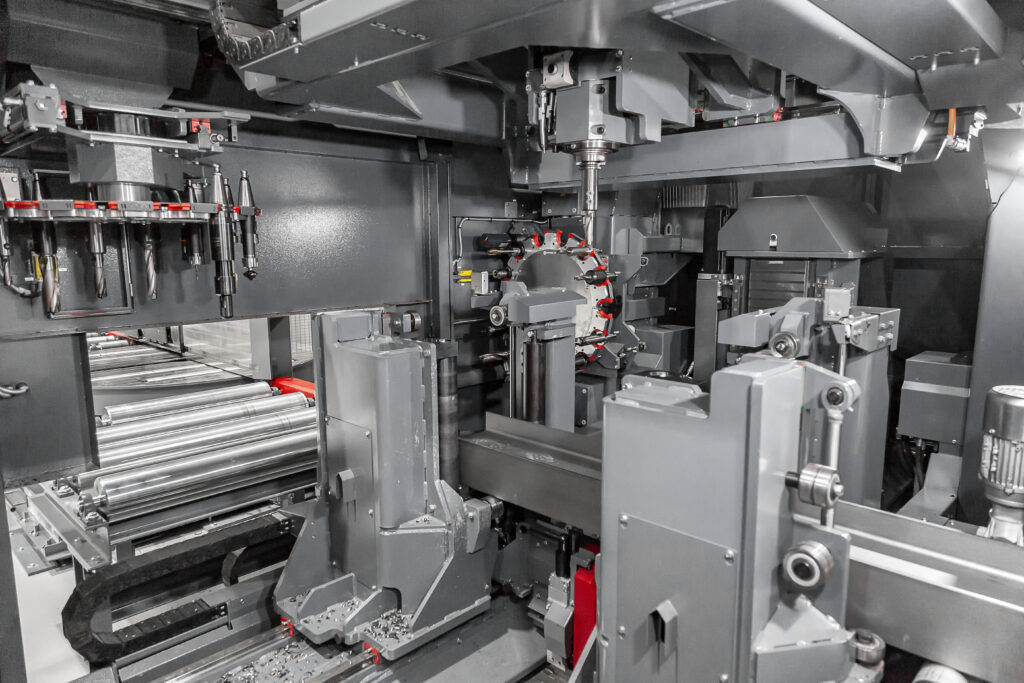
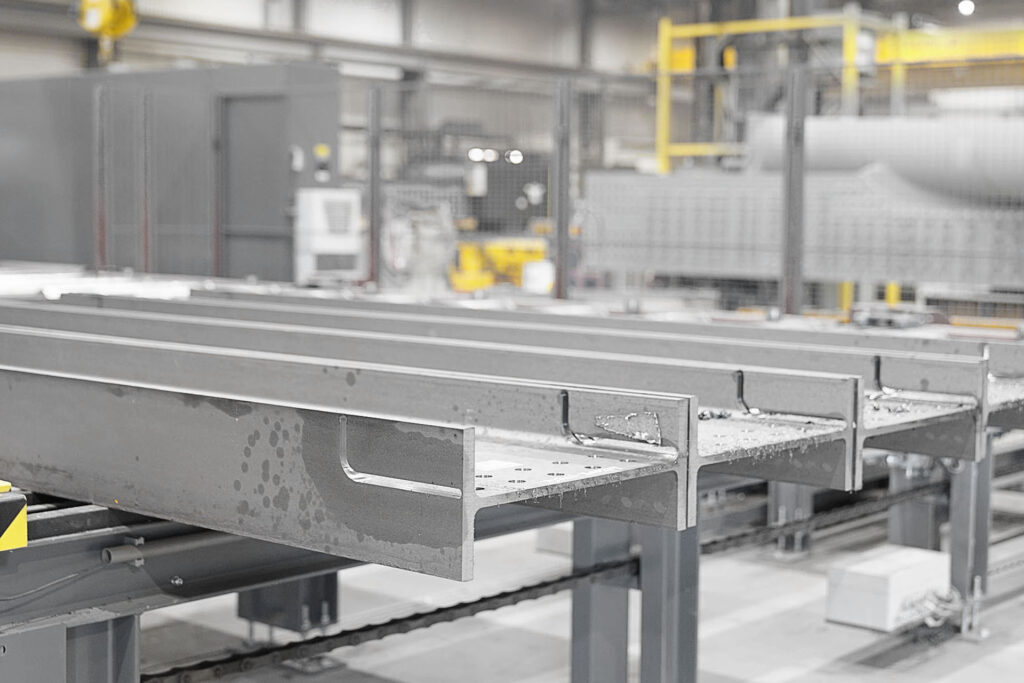
ENHANCED OPERATOR EFFICIENCY
The new system also minimizes the need to stop operations for various reasons, such as storing small parts. "With the transfer system and small parts sorting, operation stoppages have significantly reduced," Félix points out. This continuous operation capability is crucial in meeting tight project timelines.
Flexibility is another critical feature of Canam-Bridges' machinery. "We need to be able to switch programs and change raw materials quickly. This machine provides that ability, reducing scrap and enhancing efficiency in our process," Félix emphasizes.
EFFICIENT AND CLEAR INSTALLATION PROCESS
The installation process of the new machinery at Canam-Bridges was remarkably efficient, as described by Félix. "I was quite astonished at how fast the installation was. All sections were clearly identified, and there was no ambiguity during the installation," he says. This smooth process is attributed to the machine's design, which, although disassembled, was straightforward enough to avoid any confusion.
Félix highlights the exceptional quality of the machine: "The initial quality was outstanding, with great attention to detail in all the mechanical assemblies." This emphasis on quality is crucial in ensuring the longevity and reliability of the machinery, which is essential in the demanding field of bridge construction.
Proactive and Collaborative Support from Voortman
The team at Voortman received high praise for their proactive and collaborative approach. Félix states, "They've been very responsive to our needs and adjustments. While they don’t always have immediate answers, their willingness to work towards solutions is commendable." This level of support is crucial for Canam-Bridges, as it ensures that the machinery can be tailored to meet their specific requirements.
The installation of this new equipment represents a significant step forward for Canam-Bridges. With the proactive support of the Voortman team and the machinery’s high quality, Canam-Bridges is well-equipped to enhance its operational efficiency and continue delivering high-quality bridge construction projects.