RZEMIEŚLNICZA DOSKONAŁOŚĆ W PRODUKCJI DUŻYCH ZBIORNIKÓW CIŚNIENIOWYCH
dla globalnej branży naftowo-gazowej
„Mieliśmy do czynienia z różnymi maszynami do cięcia, ale żadna nie oferowała możliwości zbliżonych do tej maszyny”.
Referencje Energy Weldfab
- LOKALIZACJA:
- ROK ZAŁOŻENIA:
- POWIERZCHNIA:
- White Oak, Texas
- 1990
- 121.406 M2
„Mieliśmy do czynienia z różnymi maszynami do cięcia, ale żadna nie oferowała możliwości zbliżonych do tej maszyny”.
RZEMIEŚLNICZA DOSKONAŁOŚĆ W PRODUKCJI DUŻYCH ZBIORNIKÓW CIŚNIENIOWYCH
Energy Weldfab mieści się w zakładzie o powierzchni 12 000 m2, który stanął na działce o powierzchni ponad 1214060 m2 w White Oak w Teksasie. Fabryka zatrudnia dwustu pracowników pracujących w systemie 2-zmianowym, którzy z olbrzymią starannością produkują duże zbiorniki ciśnieniowe dla branży naftowo-gazowej. Są prawdziwymi ekspertami od gięcia metalu, spawania, wycinania otworów, pasowania rur oraz starannego wykańczania i malowania zbiorników przeznaczonych dla klientów na całym świecie. Ta rodzinna firma z dumną historią sięgającą prawie ćwierć wieku jest zaufanym dostawcą sprzętu do przetwarzania dla sektora ropy naftowej i gazu. Produkowane zbiorniki są wykonane z metalu o szerokim zakresie grubości od niespełna 0,25 cala do 8 cali. Ze względu na złożony charakter tych zbiorników charakteryzujących się wieloma punktami połączeń, ich produkcja wymaga intensywnego cięcia i spawania.
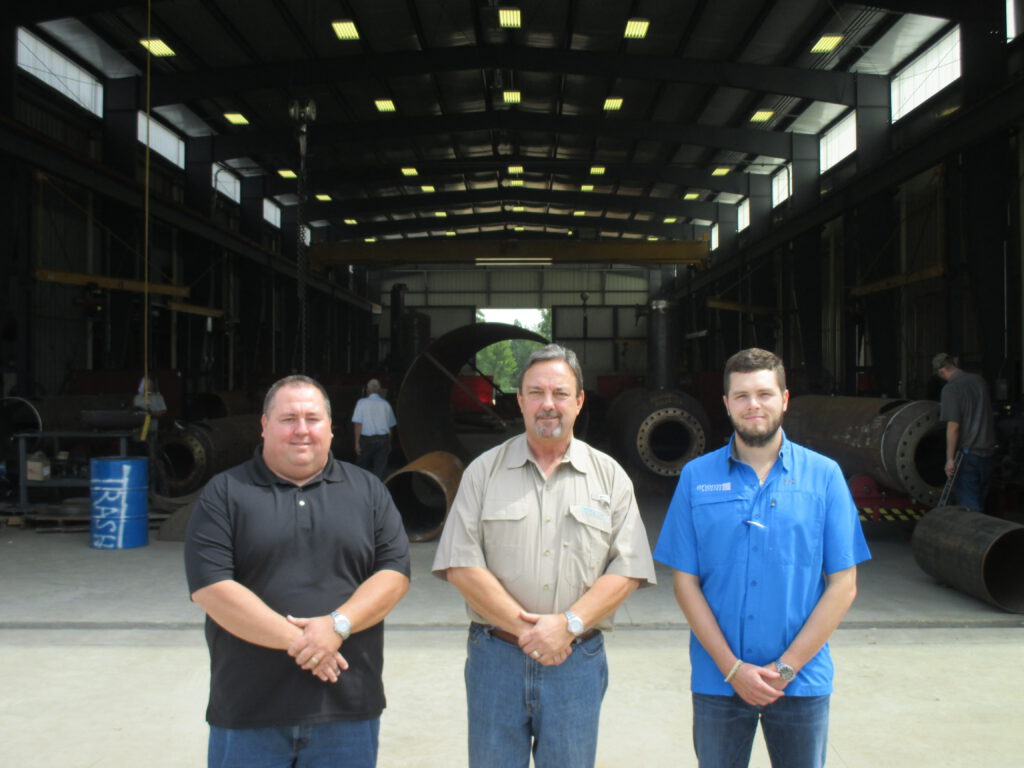
TRANSFORMACJA UKIERUNKOWANA NA ROZWÓJ
Do niedawna firma Energy Weldfab polegała na tradycyjnej metodzie ręcznego cięcia przy użyciu palnika tlenowego, co jest głęboko zakorzenioną praktyką w branży od czasu jej powstania. Wiceprezydent Stoney Lake wyjaśnia: — Od samego początku był to nasz standard branżowy. To było coś, co robiliśmy od zawsze. Ponieważ jednak działalność firmy znacznie się rozwinęła, stare podejście okazało się niewystarczające do zaspokojenia rosnących wymagań. Zatrudnienie dodatkowych pracowników nie było opłacalnym rozwiązaniem z powodu niedoboru wykwalifikowanych pracowników. Lake wyjaśnia: — Naprawdę brakuje wykwalifikowanych pracowników. Nie jest tak, jak kiedyś, gdy ludzie, którzy mieli doświadczenie w montażu rur, walili do nas drzwiami i oknami. Teraz trudno jest znaleźć osoby, które potrafią ręcznie rozrysować zbiornik i precyzyjnie wyciąć otwory. Zdając sobie sprawę z potrzeby wprowadzenia poważnych zmian, aby kontynuować działalność, firma Energy Weldfab uznała rozwiązanie transformacyjne za konieczność.
NOWOCZESNA MASZYNA DO CIĘCIA PROFILI RUROWYCH
Aby rozwiązać ten problem, firma Energy Weldfab zainwestowała w najnowocześniejszą maszynę do cięcia profili rurowych 3D, która zastąpiła pracochłonny ręczny proces cięcia. Wybrana maszyna MO Heavy-Duty może ciąć rury o masie do 30 ton. Lake jest zadowolony z przyjętego rozwiązania: — Mieliśmy do czynienia z różnymi maszynami do cięcia, ale żadna nie oferowała możliwości zbliżonej do tej maszyny. Jej zdolność do obsługi większych cylindrów przewyższa wszelkie inne dostępne opcje. Ten w pełni zautomatyzowany system efektywnie profiluje okrągłe rury i opływowe końcówki (kopułki), wspomagany przez oprogramowanie, które płynnie koordynuje wymianę informacji między sześcioma osiami maszyny, palnikami tnącymi oraz oprogramowaniem CAD/CAM. System Energy Weldfab oferuje dwa palniki tnące wykorzystujące palnik tlenowy do cięcia rur o grubości do 6 cali oraz Hypertherm HyPerformance HPR400XD, system plazmowy 400 A o wysokiej rozdzielczości, stosowany głównie do cięcia części ze stali nierdzewnej oraz części o cieńszych ściankach.
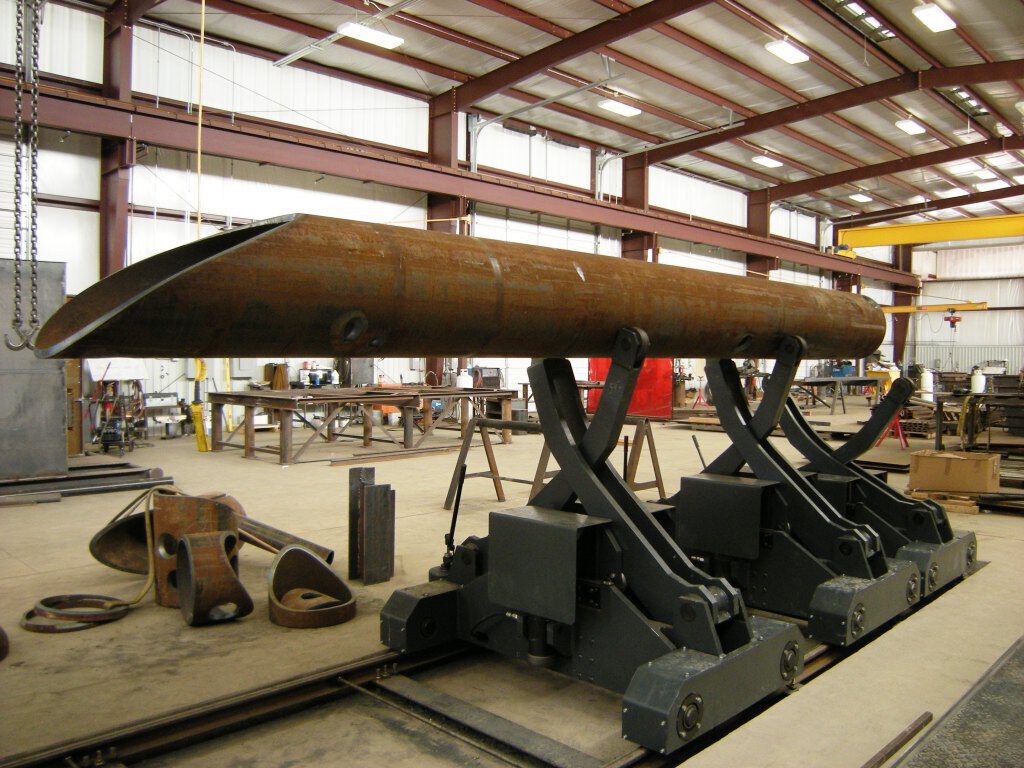
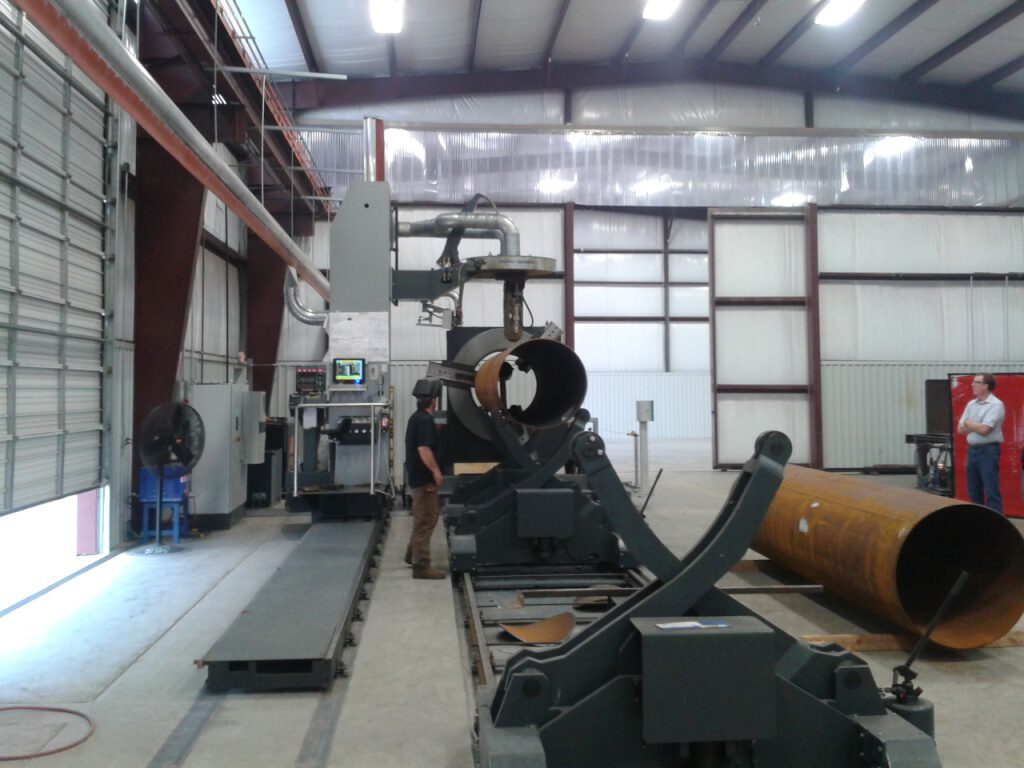
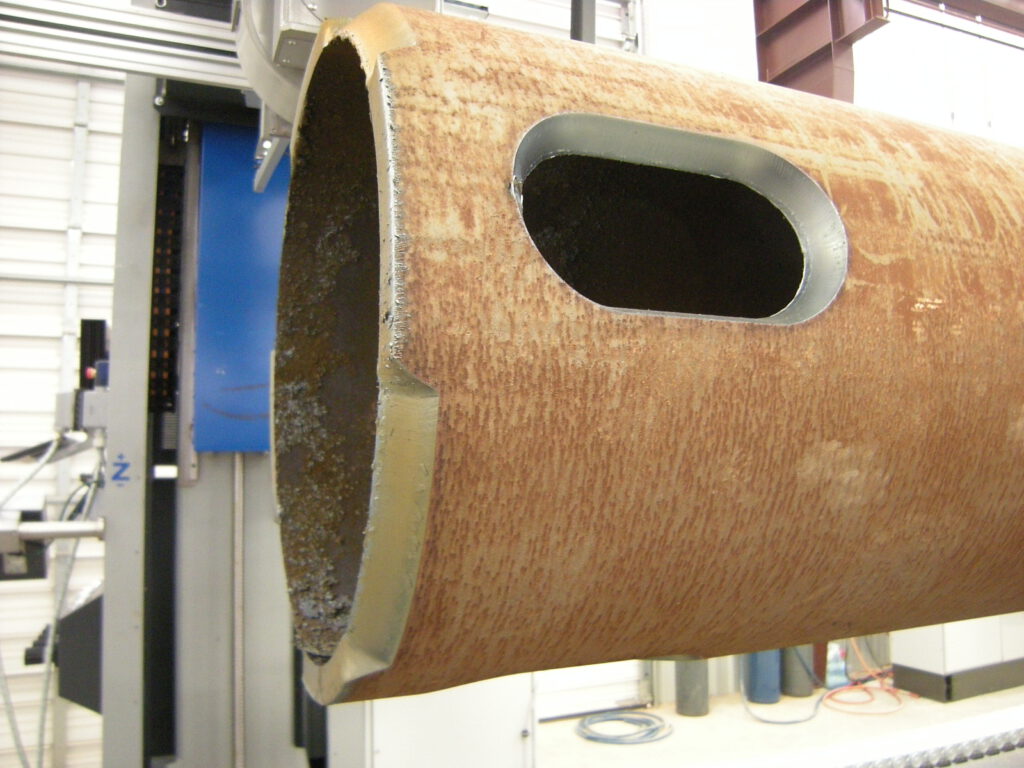
NIEZRÓWNANA PRECYZJA I WYDAJNOŚĆ
Przedstawiciele firmy uważają, że efekty działania maszyny były wyjątkowo dobre, zwłaszcza ze względu na znaczną poprawę precyzji i produktywności. Zadanie, które kiedyś wymagało dwóch osób i sześciu godzin pracy, teraz można wykonać w zaledwie 18 minut. Lake wyjaśnia poprzedni proces: — Wcześniej potrzebowalibyśmy dwóch pracowników, aby rozrysować linie i zaznaczyć otwory do wypalenia. Następnie prosiliśmy dział kontroli jakości o weryfikację wymiarów i orientacji. Po zatwierdzeniu dwóch pracowników przystąpiłoby do wycinania otworów i czyszczenia krawędzi. Na koniec trzeba było jeszcze wykonać kolejną kontrolę jakości. W dzisiejszych czasach nasza maszyna do cięcia rur bezproblemowo wykonuje wszystkie te zadania, łącząc pięć kroków w jeden. Ponadto wdrożenie nowego systemu doprowadziło do zredukowania odchyleń w jakości detali. „Jakość cięcia jest zaskakująco wysoka, a cięcia kątowe są wręcz idealne”.