Automated Plate Processing Redefined!
Introducing the Voortman V320, your gateway to advanced, uninterrupted plate processing - a machine that always keeps going. Engineered for peak efficiency, the V320 transforms your production process with continuous automated workflows, featuring a robust, fast dropdoor table, a wide conveyor belt, and automatic chip removal.
Request your quote right away!
Read moreWE KNOW IT'S A LOT
SO, HERE IS THE VOORTMAN V320 IN A NUTSHELL
Discover the unique aspects of the V320, as Ben Morrall gives you a concise overview of its standout features. Join him directly from the production floor of GB Structures, where the V320 is demonstrating its remarkable capabilities and transforming their operations.
MAXIMIZING PRODUCTIVITY
AND MINIMIZING MANUAL INTERVENTION
The machine autonomously unloads parts up to 500x500 mm (20"x20"), weighing up to 75 kg (165 lbs), minimizing manual intervention for longer periods. Operators are free to concentrate on other important duties, only returning for specific manual tasks or to sort the parts that have been automatically dropped into the parts bin. The V320's innovative gripper system, minimizes the dead zone, allowing you to cut extremely close to the grippers, maximizing material yield.
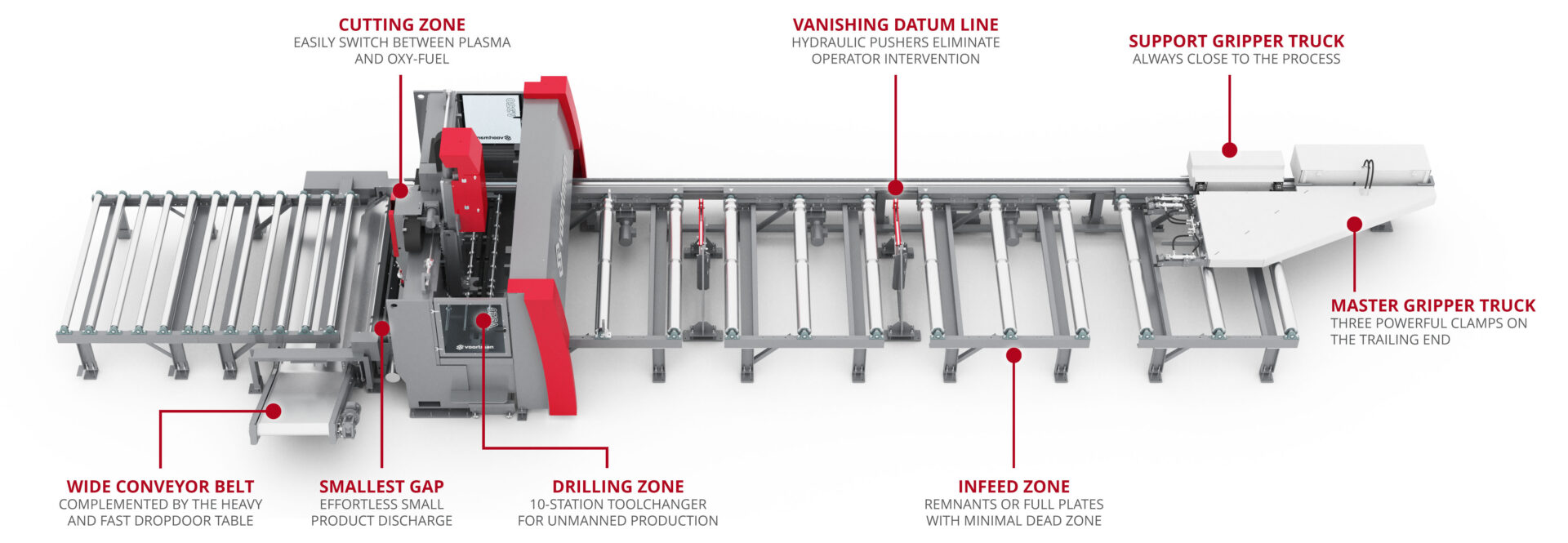
REDUCE YOUR COSTS PER PART
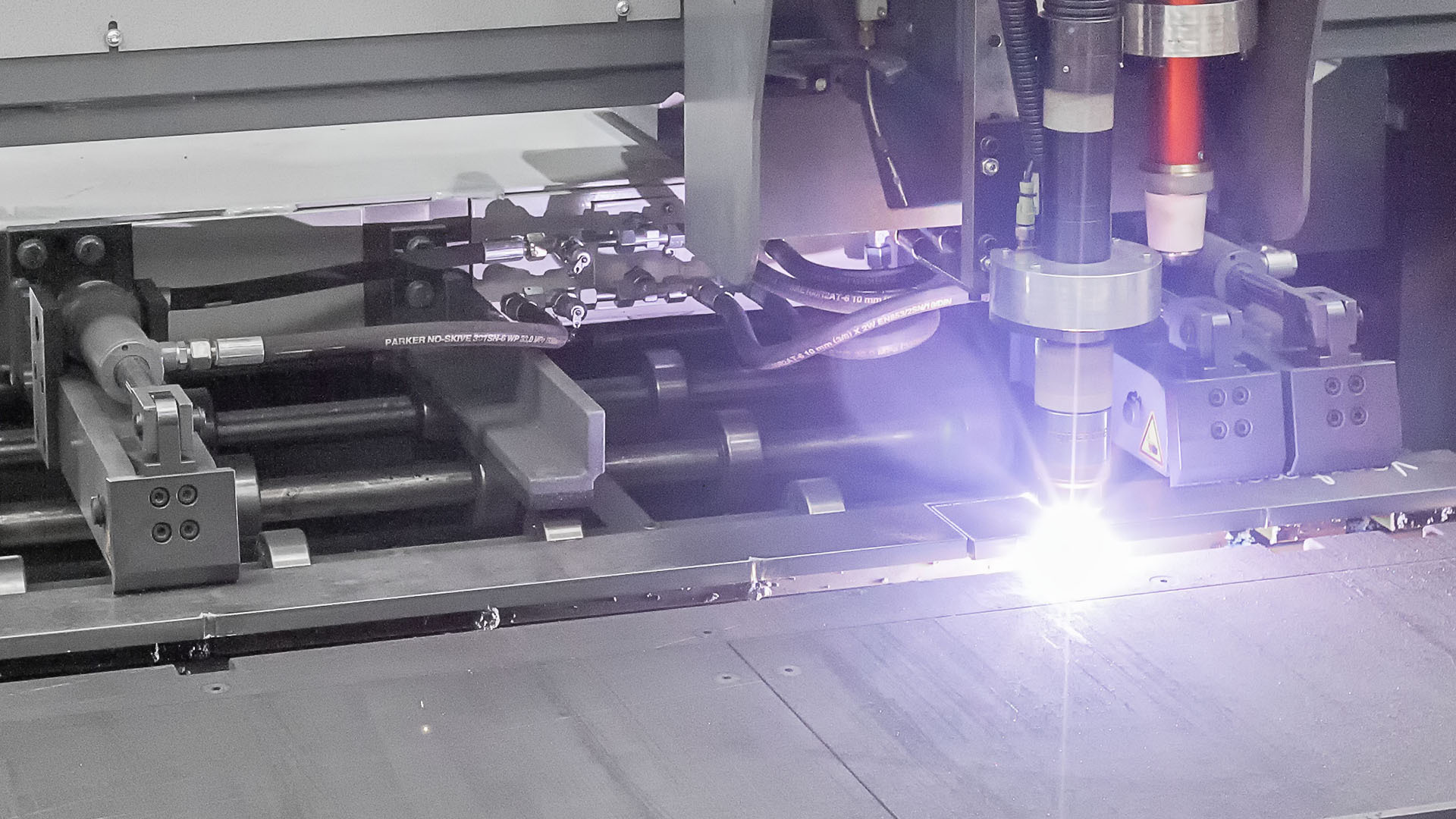
REDUCED DEAD ZONE
The V320 offers a reduced dead zone, enhancing your material usage. It processes entire plates, including areas between gripper truck clamps, with a design that permits the side gripper truck to release from the plate in the final processing, thereby maximizing material yield.
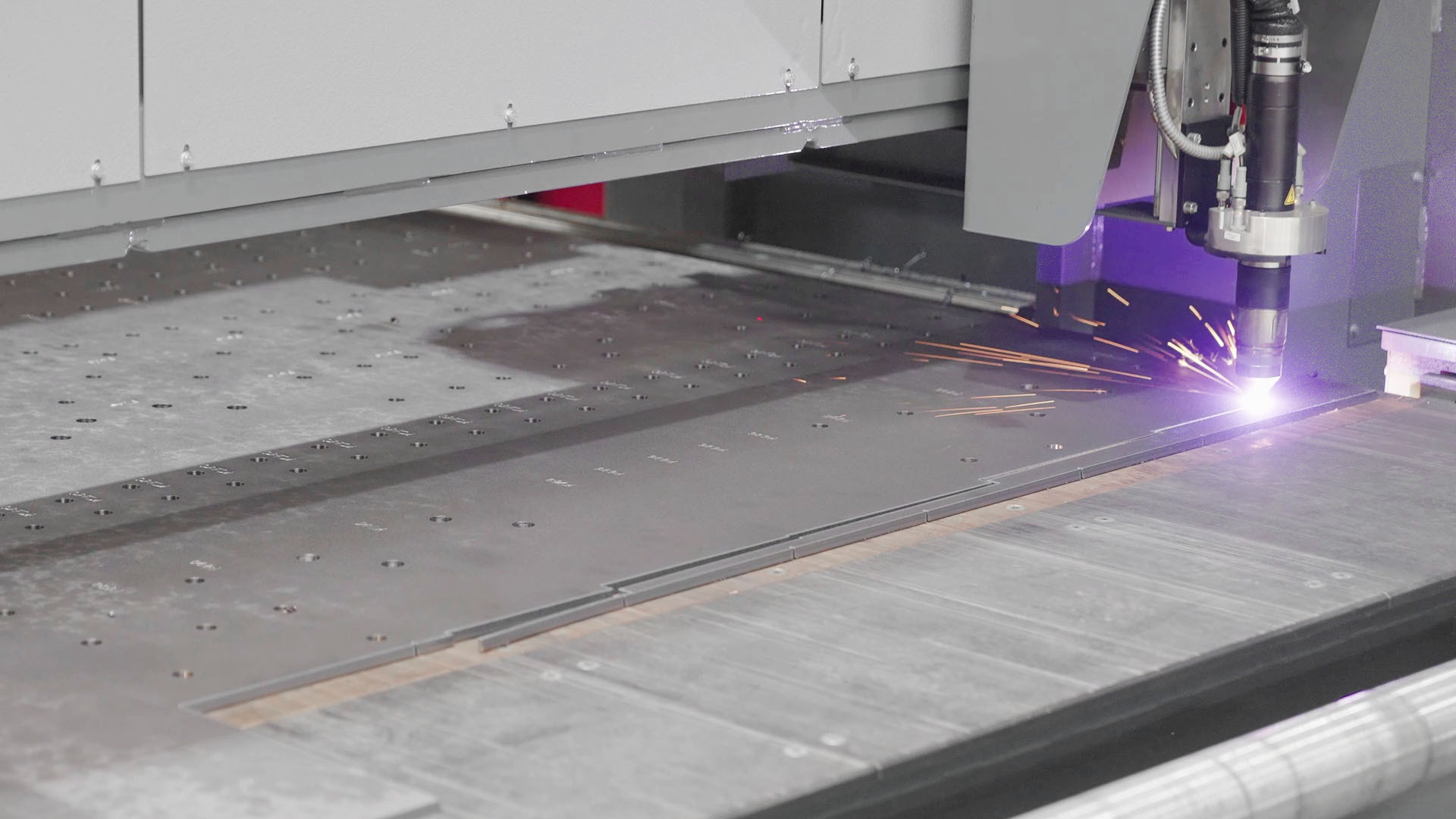
MINIMAL WASTE
Boasting efficient nesting in remnants and HD Multidrop, this machine excels in reducing material waste and operational expenses, optimizing the use of nearly the entire skeleton of the plate.
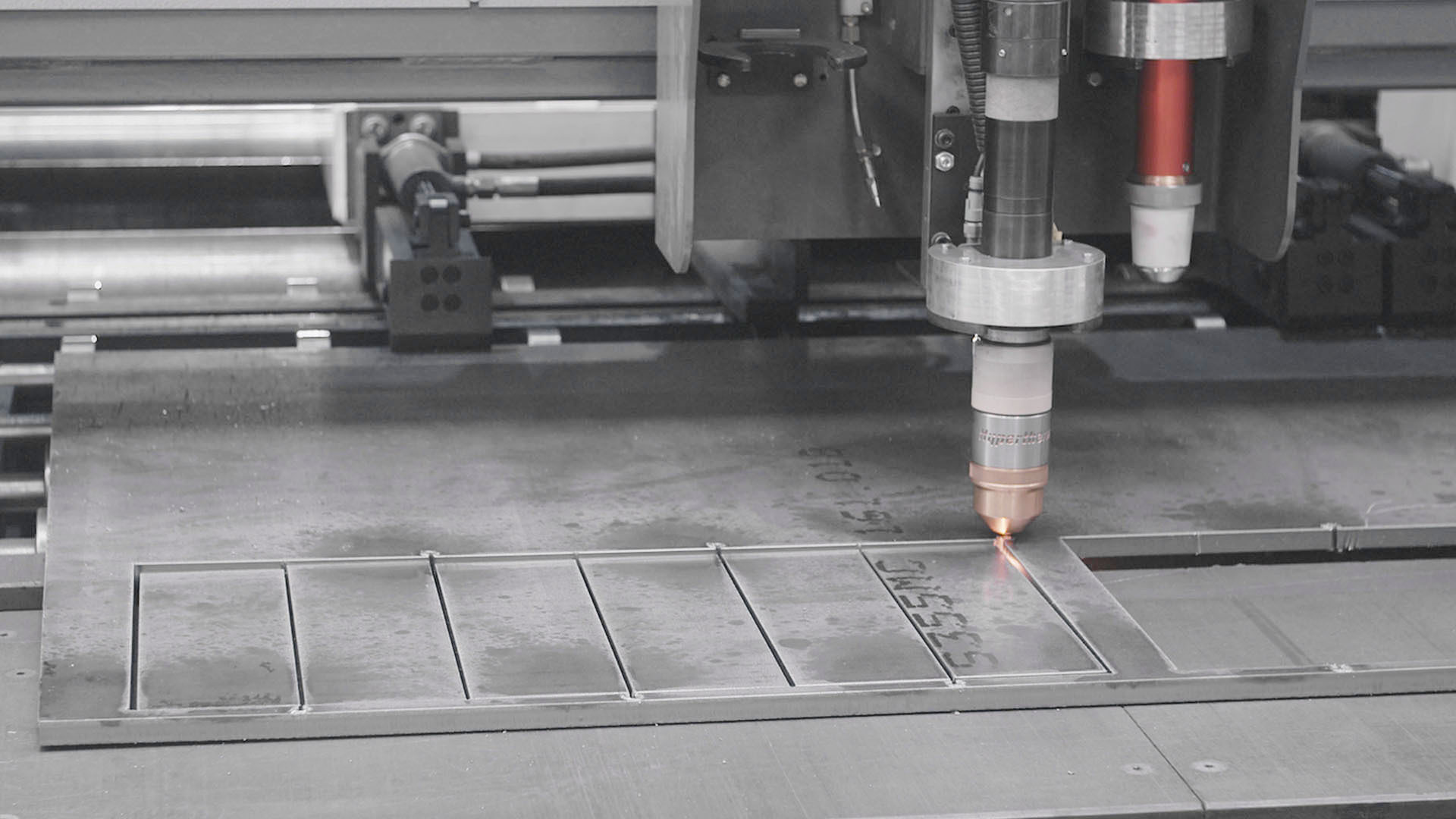
BRIDGE CUTTING
Nesting bridge cuts boost efficiency, saving up to 8 seconds per product by discharging a full row at once and minimizing plasma arc shutdowns. With fewer pierces required, it lowers consumable costs and improves material usage.
UNLOCK THE BENEFITS OF HD MULTIDROP
LESS WASTE - MORE EFFICIENCY
HD Multidrop ensures
that almost the entire skeleton of the plate is utilized in the most optimal
way, reducing waste.
It's innovative
approach sets new standards and provides these 3 main benefits:
1. MAXIMIZING MATERIAL YIELD
An
advanced nesting technique significantly improves material yield and efficiency
in plate cutting. Delivering cost savings and a more environmentally friendly
operation.
2. REDUCED CRANE USAGE AND MANUAL HANDLING
Given that the entire skeleton is comprehensively utilized, our workflow significantly enhances safety by mitigating the risks commonly associated with heavy lifting and manual material handling.
3. LESS CONSUMABLE WEAR, GAS AND POWER CONSUMPTION
HD Multidrop reduces operating costs by lowering the number of cut meters and thus reduced consumable wear and power and gas usage. It leads to fewer replacements, lower maintenance costs, and a more sustainable operation.
UNLOCK UNMANNED POTENTIAL WITH ADVANCED AUTOMATION
Experience the pinnacle of automation with our V320, designed for prolonged unmanned operation. The V320 leads the way in efficiency and continuous automated workflows, complemented by tools like the heavy and fast dropdoor table, a wide conveyor belt, automatic chip removal and more. The result? Minimal manual intervention, maximum productivity in unmanned settings. Find out more below.
SMALLEST GAP, BIG EFFICIENCY
EFFORTLESS SMALL PRODUCT DISCHARGE
Forget the time-consuming process of extracting lots of small products from the slag bin and enjoy long periods of unmanned operation. Thanks to the exceptionally small cutting gap, even products of 70 x 70 mm (2 - 3/4"x 2 - 3/4") are unloaded through the heavy dropdoor table onto the conveyor belt.
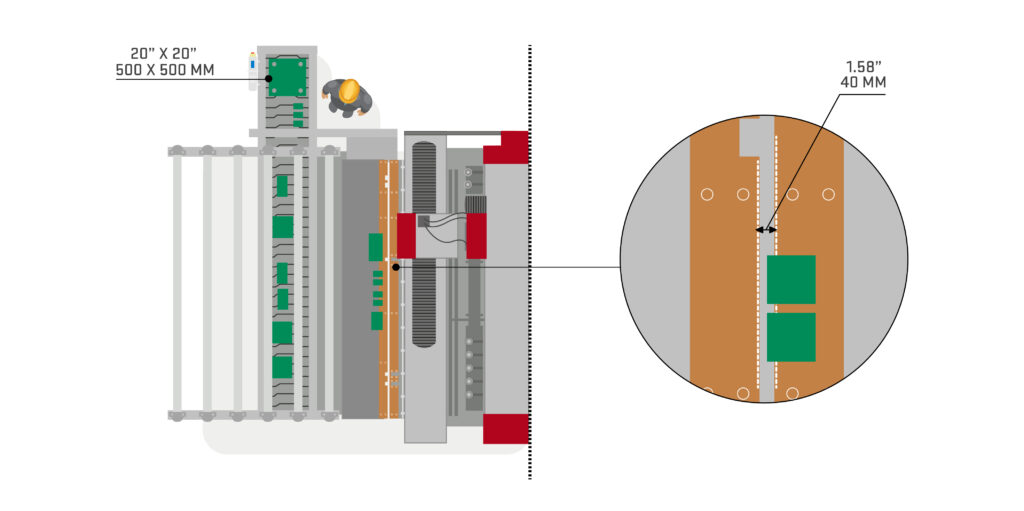
ONLY BE THERE WHEN NEEDED
The Voortman Operator Dashboard shows the time per process, the number of operations still to be performed and the remaining production time. But most importantly; it shows when an operator needs to be present at the machine for a manual action. During times when operators are not needed at the machine, work can be done in other areas in your workshop. Or in other words; adding value where it is actually most needed at that particular moment.
GET THE HIGHEST THROUGHPUT
Maximize your production throughput with Voortman's advanced technologies equipped on the V320. Our magnetic mounting system ensures swift operation and minimal downtime, while the fastest height control drastically reduces cut-to-cut times. Voortman's Resume Cutting functionality provides quick, high-quality restarts when needed, and our leading discharge table accelerates processing, significantly boosting overall productivity.
QUALITY AND UPTIME AT THE FOREFRONT
The V320 is engineered to excel in both quality and uptime. Every component and feature is meticulously designed to serve these key objectives. Notably, our software solutions empower you to execute advanced cuts with increased efficiency, all while maintaining or improving product quality.
V320'S DUAL GRIPPER TRUCKS
PRECISION PLATE MOVEMENT FOR QUALITY RESULTS
The V320's innovative gripper system minimizes the dead zone, allowing you to cut extremely close to the grippers, maximizing material yield. The V320 features two measuring gripper trucks for precise plate movement. The master gripper truck uses three clamps to secure the trailing end, and the support gripper truck, with two clamps, holds the plate at the datum line. This dual-gripper system ensures accurate processing of the entire plate and flat bar lengths, enhancing your end product quality.
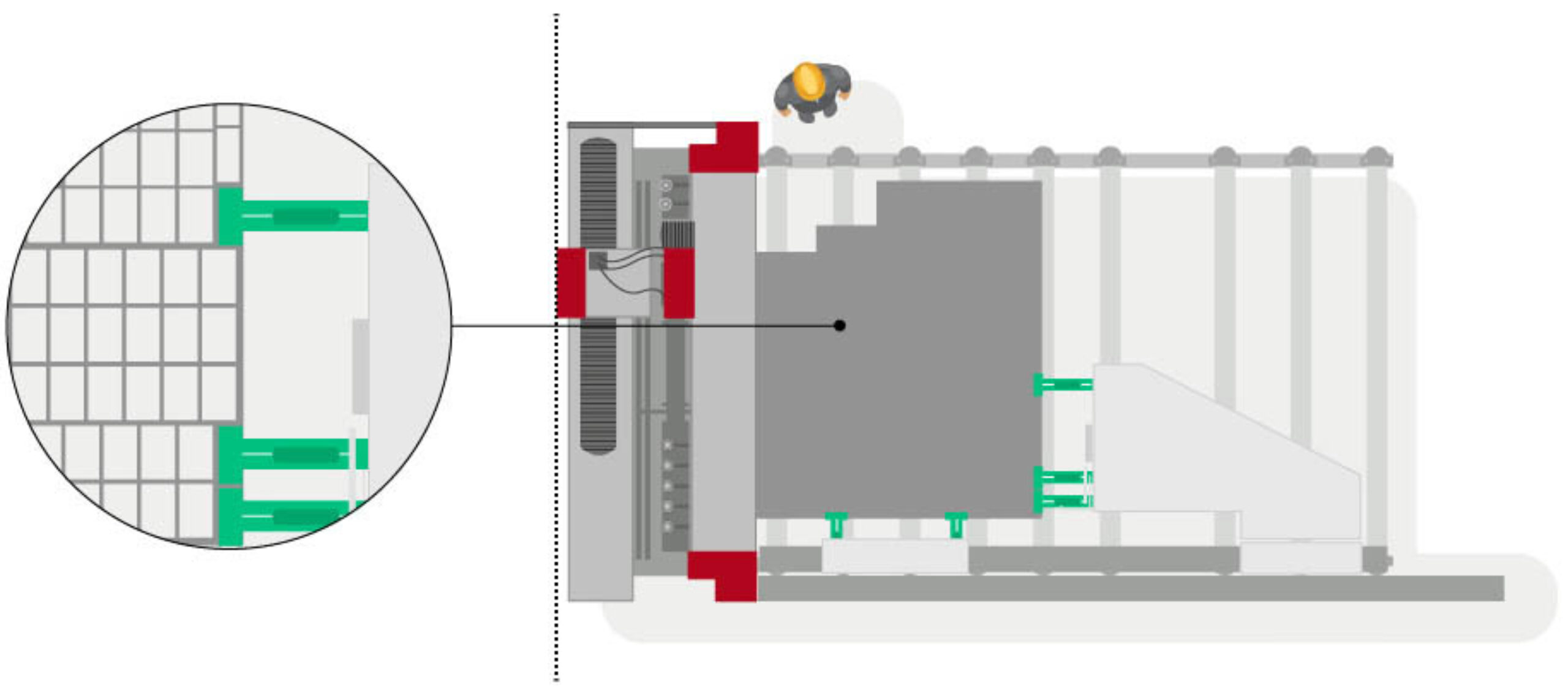
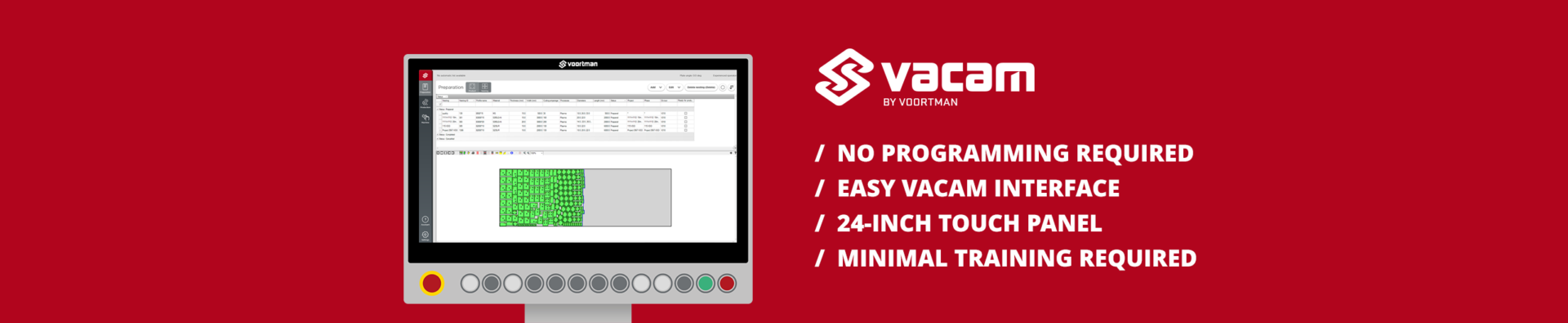
MAXIMIZING MATERIAL YIELD AND REDUCING CONSUMABLE COSTS
The V320 is a game-changer in material utilization and cost-saving solutions. With its innovative design, the dead zone is minimized, maximizing material yield. The integrated VACAM Software aids in optimal consumable management, balancing cost and quality. Enhanced by features like efficient nesting in remnants and HD Multidrop, the V320 significantly reduces material waste and operational expenses.
WEBINAR / Voortman & Hypertherm
HOW TO IMPROVE YOUR PLASMA CONSUMABLE MANAGEMENT
Finding that sweet spot for changing consumables is key, isn't it? In our webinar with Hypertherm, we discussed various topics related to improving plasma consumable management. Our experts shared actionable insights and clever strategies that you can immediately apply to your daily operations. Get ready to take your plasma consumable management to the next level with our webinar recording!
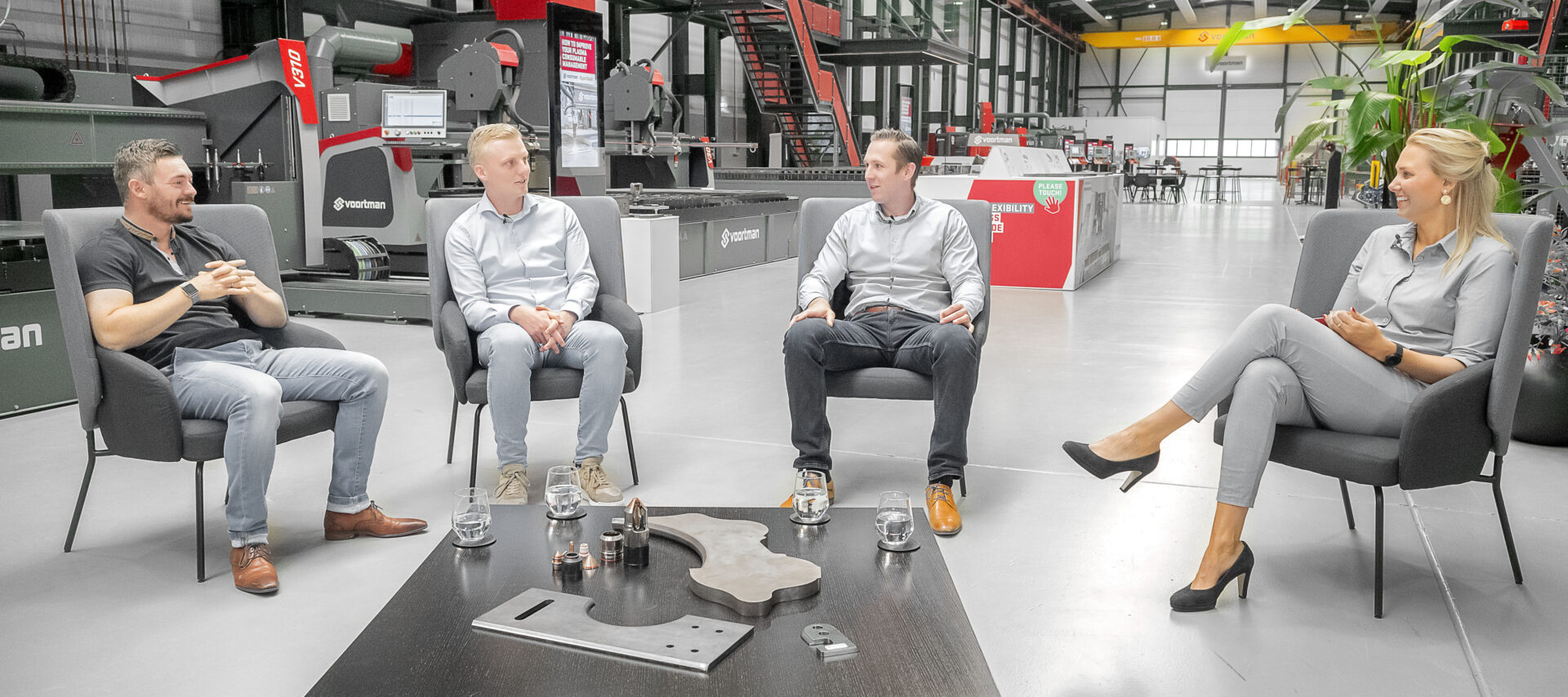
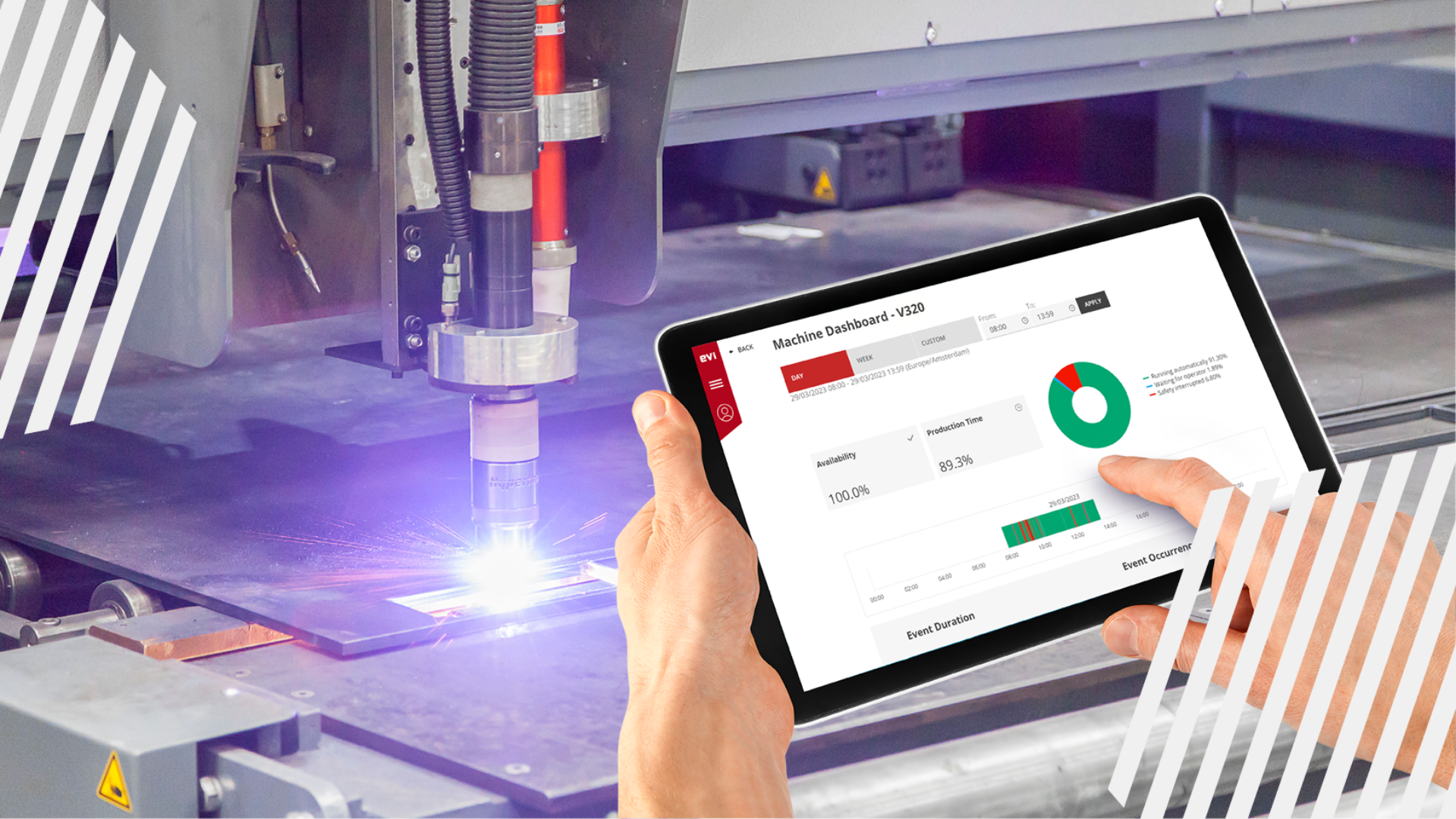
GAIN INSIGHTS IN UTILIZATION RATE AND PERIODS OF DOWNTIME
"What is the current utilization rate of my machines and what contributes to any downtime?"
Good question! Relying on operators’ and managers’ experience may suffice for daily operations, but for efficiency improvements, understanding real machine status and downtime reasons is crucial.
Lean on EVI Software to:
- Get insights into your machine production output and history.
- Easily determine why there was any downtime.
- Increase uptime of your machine.
Specifications
Voortman V320 | ||
---|---|---|
Voortman V320 | ||
Working width | ft | 6 or 10 |
Working length | ft | 20, 30 or 40 |
Maximum cutting thickness | inch | 3 |
Positioning weight | lbs | 16,500 or 19,850 |
Drilling and positioning | Servo motors | |
Positioning speed X | f/min | 65-1/2 |
Positioning speed Y | f/min | 98-1/2 |
Positioning speed Z | f/min | 98-1/2 |
Marking | milling/plasma | |
Drilling units | vertical | 1 |
Nominal power | Hp | 40 |
Speed drill head | rpm (stepless) | 0 - 2,500 |
Tool changer | 2 x 5 | |
Drill holder | SK40 | |
Drill diameter | inch | 13/64 - 1-9/16 |
Thread tapping | M6 - M30 | |
Plasma | up to (amp) | 400 |
Oxy-fuel torch | 1 |