THE WELL-KNOWN VOORTMAN CUSTOMER SERVICE
Experience
world-class Voortman customer service with our global network of subsidiaries,
warehouses, and service points. No matter where you are, we are always near you, ensuring prompt assistance. We are renowned for our
unwavering dedication to customer satisfaction - we never let you down. In
fact, 90% of issues are resolved remotely through our 24-hour online support. We prioritize your needs above all. Your success is
our accomplishment.
Call customer service
+31 (0) 548 536 399
Email customer service
service@voortman.net
Email Parts & Consumables
parts@voortman.net

WHAT WE DO
Get world-class support no matter where you are. With dedicated teams in Australia, The Netherlands, and the USA, we provide round-the-clock assistance. Our global network ensures quick and efficient service, with local support, well-stocked spare parts, and state-of-the-art production facilities. We offer a range of Service Label Agreements tailored to your needs. Plus, we prioritize building personal connections by assigning you a dedicated point of contact. Experience our training options at your location or at our Voortman Experience Center.
- Round-the-clock assistance
- Service Label Agreements
- Dedicated point of contact
- Training options on-site
WHAT YOU CAN DO
Boost productivity and minimize disruptions by investing in preventive maintenance. Find the ideal Service label to suit your requirements. Maximize production performance with skilled operators. Don't settle for anything less than peak efficiency and output – opt for trained employees. Effortlessly monitor and manage stock levels from your office using our innovative RTS-system software.
CLEAN-AND-MAINTAIN
Regular maintenance not only prolongs the life of components but also guarantees uninterrupted operation and a neat working environment.
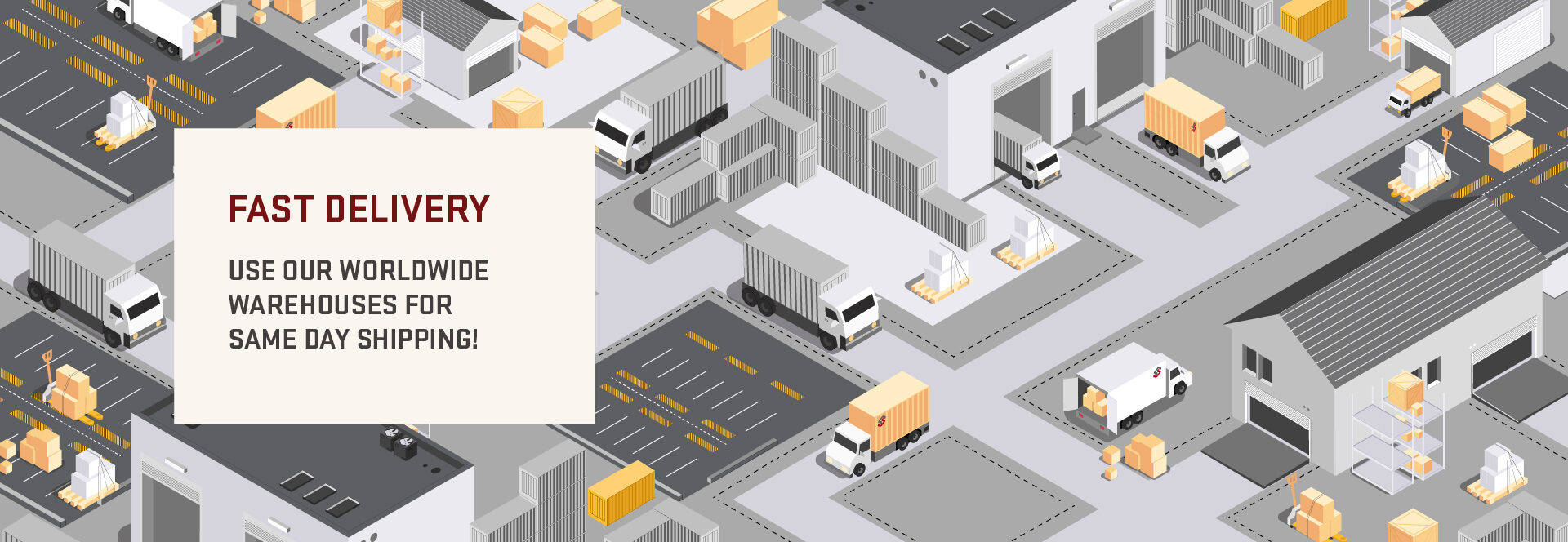
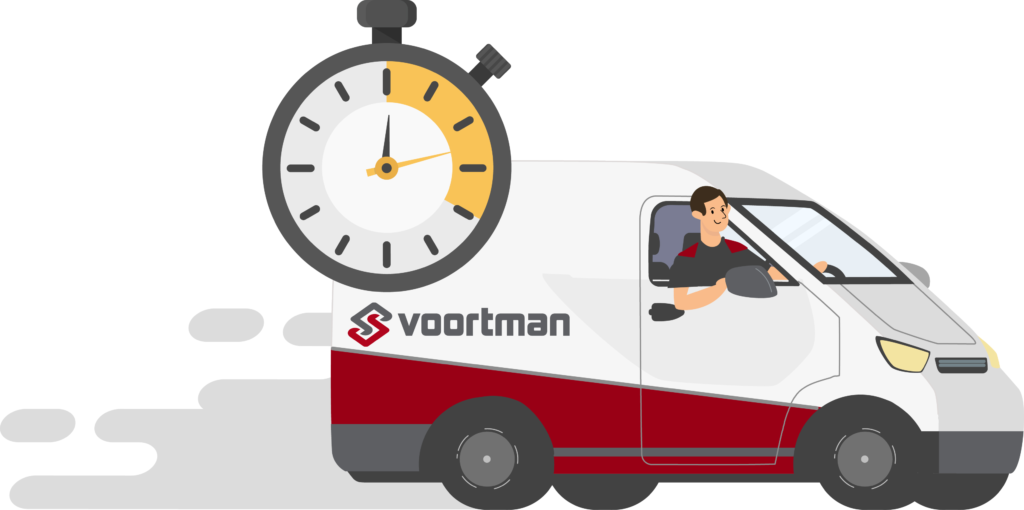
ALWAYS NEAR TO YOU
No matter where you are, we aim to be as close as possible to you. Our team of locally-based engineers isn't just familiar with your area - they understand your needs and speak your language.
Highly trained and academically skilled, they are ready to answer any question you might have. And if they don't have the answer right away? They won't stop until they find someone who does. That's how committed we are to maintaining short, efficient lines of communication.
We understand that downtime can be devastating, which is why we do everything in our power to minimize it. Trust us to be there when you need us most.
DID YOU KNOW?
WE SOLVE 90% ONLINE!
We are seamlessly integrated into your system. We've installed cameras within your machinery that allow us to monitor live production and sift through historical data to identify specific occurrences. If you're a customer with a RED service label, we have the capability to view real-time insights from your production dashboards. This allows us to swiftly react to any potential issues and, if necessary, dispatch a service engineer immediately.
We pride ourselves
on our global support network, with departments in Australia, The Netherlands, Germany and the USA working in harmony to provide round-the-clock assistance. This
24-hour coverage ensures that no matter where you are in the world, you'll
receive consistent, high-quality support.
For remote support, TeamViewer Quick Support is used by our support engineers. This software enables them to access your machine control in order to solve any interruptions.
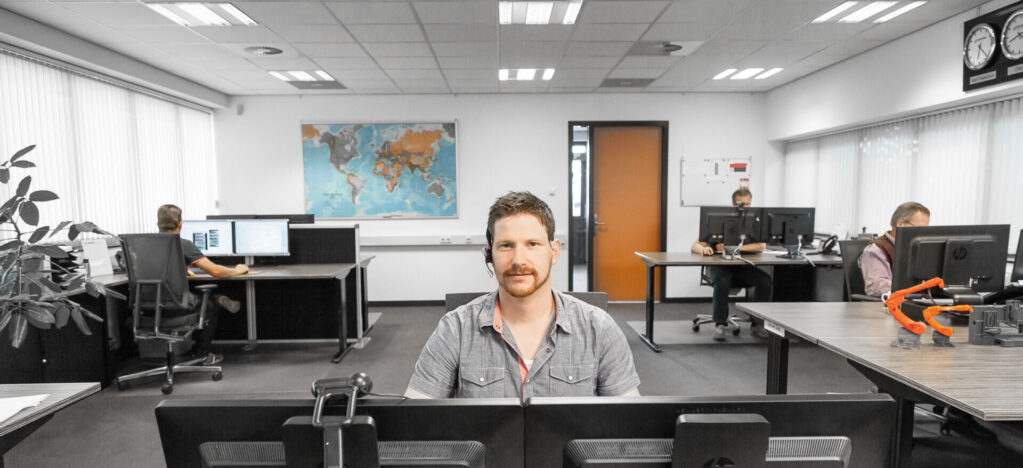
GOOD DAY, GUTEN TAG, MIŁEGO DNIA AND BONNE JOURNÉE!
Imagine having us by your side, no matter where you are. Our mission is to ensure we're always there for you in every possible way. We go the extra mile to expand our reach through local support, well-stocked spare parts and consumables, dedicated sales and service offices, and state-of-the-art production facilities. Now, let's introduce you to some of our seven global locations.
KEEPING YOU UP AND RUNNING
Unexpected downtime is never convenient. Minimize or predict downtime with a preventive maintenance agreement. Voortman offers a variety of different Service Label Agreements (SLA’s) to meet the individual needs of each customer. The labels differ in the amount of maintenance inspections, response time, training and parts and consumable discounts. The Red Label is the most comprehensive and best value for maintaining consistent production and finished part quality, making it the most popular Service Label Agreement. Find out which label suits you best.
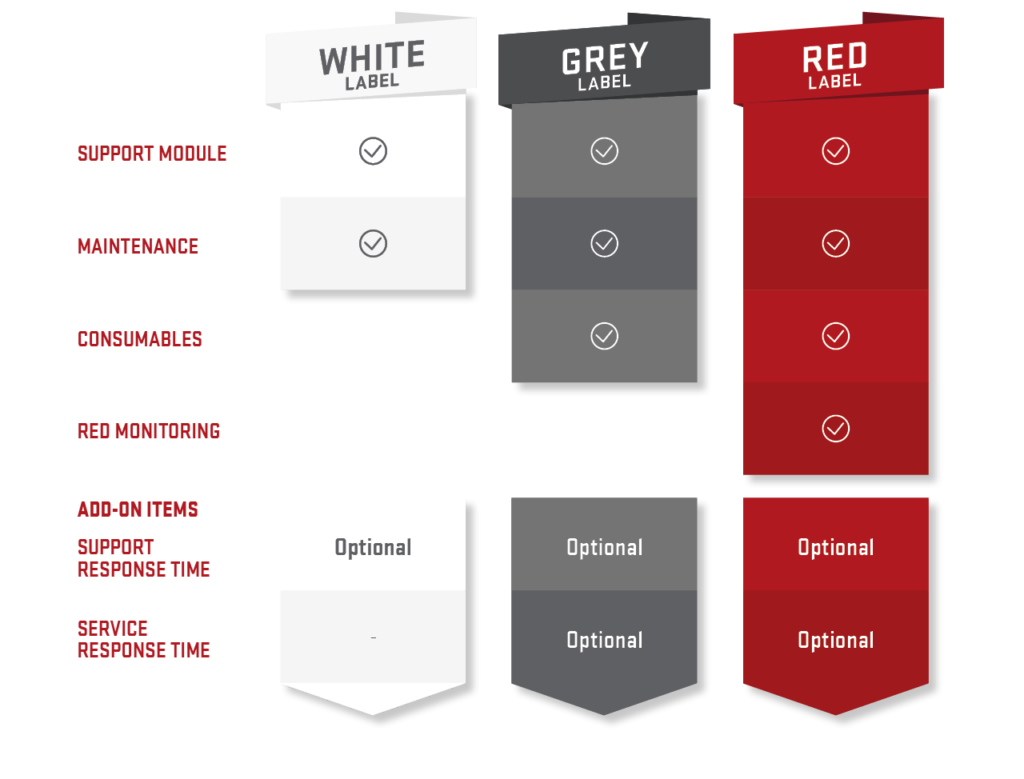
WHITE LABEL
Our White Label takes care of all the preventive maintenance needs for your machines. Get full support, periodic on-site check-ups, and enjoy discounts on support, service, and training. We've got you covered!
GREY LABEL
The Grey Label not only takes care of all your machine's preventative maintenance needs, but it also offers additional perks. By committing to a specific threshold value on consumable purchases, you'll receive an extra discount on the Support Module.
RED LABEL
Experience maximum benefits with our Red Label package. Enjoy lightning-fast response times, extensive discounts on support, service, and training, and comprehensive coverage for all your machine's preventative maintenance needs. Elevate your Voortman equipment with our inclusive monitoring system. With your permission, Voortman will remotely monitor and actively collect production data, ensuring optimal performance. By using this label, you'll receive the full discount on the Support Module.
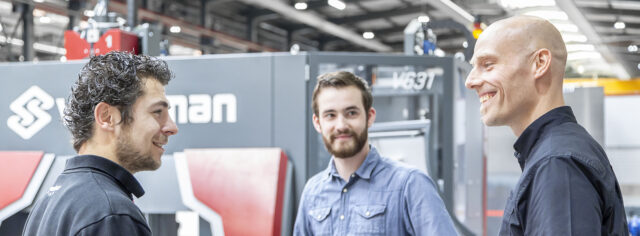
MINIMAL DOWNTIME WITH PREVENTIVE MAINTENANCE
To
ensure the longevity of your Voortman machinery and avoid any unnecessary
downtime, regular maintenance checks are crucial. By prioritizing proper
maintenance, you not only enhance the quality of your final product but also a
reliable continuation of your production.
Our team of specialized maintenance engineers conducts thorough inspections tailored to each machine type, allowing you to focus on your core business while we handle the planning and execution of maintenance tasks. Rest assured, our Customer Services Labels encompass all preventive check-ups and maintenance activities to keep your machinery running smoothly.
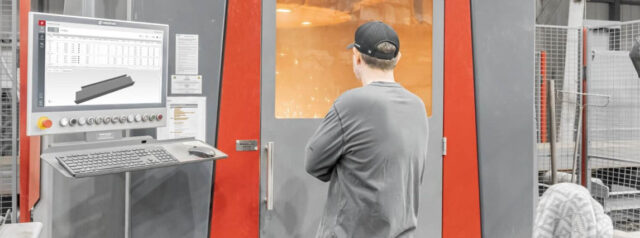
KEEP IT CLEAN AND ORDERLY FOR A LONG LIFETIME
Did you know our machines are crafted with your operator in mind? Not only do we prioritize a safe workplace, but we also make maintenance and operation a breeze. We take accessibility and reachability of modules and components into account right from the machine's design. With cleverly designed hatches, doors, and light curtains, your operator can effortlessly and safely perform maintenance tasks in no time. Regular maintenance not only prolongs the life of components but also guarantees uninterrupted operation and a neat working environment.
OFFERING THE BEST CONSULTS FOR THE BEST PARTS
WE KNOW YOU AS A CUSTOMER
BUILDING STRONG OEM PARTNERSHIPS
Experience top-notch quality with our wide range of high-quality consumables and parts, sourced directly from the Original Equipment Manufacturer (OEM), ensuring optimal performance for your Voortman machines. Our state-of-the-art warehouses are stocked with almost every part or consumable required for your machines, enabling efficient fulfillment of orders. Our dedicated specialists actively pursue long-term partnerships with manufacturers, fostering a collaborative environment for mutual learning, sharing, and product development. With such an approach, you reap the benefits of our dynamic engagement.
SPECIALISTS FOR YOUR PRODUCTION NEEDS
Our parts &
consumables department is fueled by a team of specialists who are passionate
about guiding you to find the perfect parts and consumables for your equipment
and production needs. With their expertise in various languages and extensive
knowledge of specific parts & consumables, they ensure seamless
communication across the globe. Our multicultural team hails from the United
States, Australia, Germany, France, and the Netherlands, making international
interactions easy. By providing our customers with tailored advice on
consumables, we strive to maximize uptime and maintain impeccable production
quality. Let's achieve this common goal together!
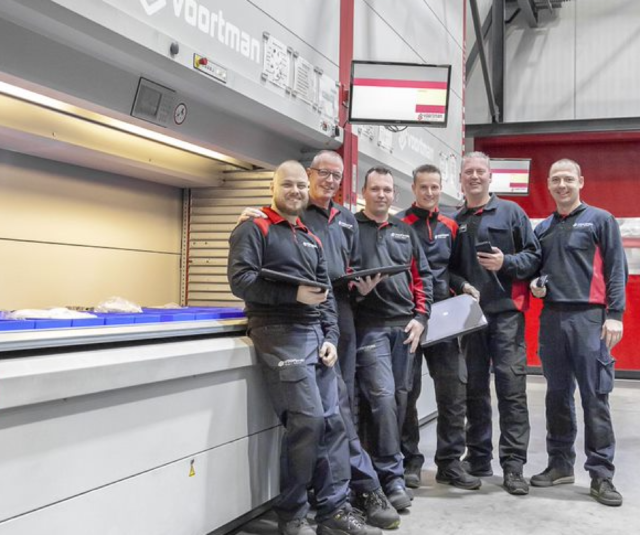
Sourced directly from the Original Equipment Manufacturer (OEM), ensuring optimal performance for your Voortman machines.
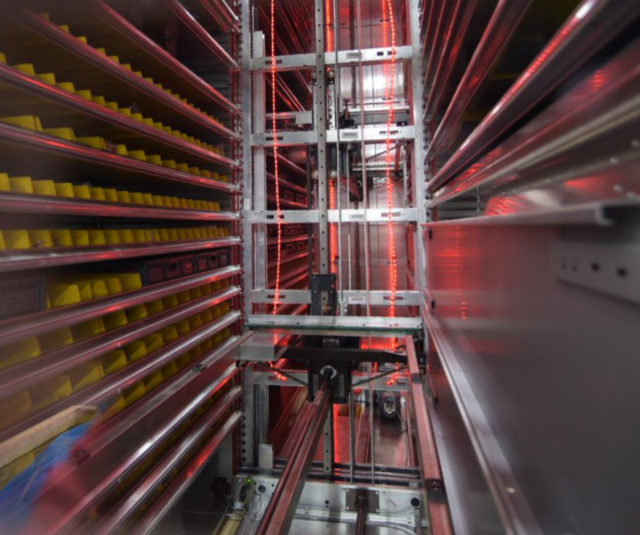
State-of-the-art warehouses are stocked with almost every part or consumable required for your machines, enabling efficient fulfillment of orders.
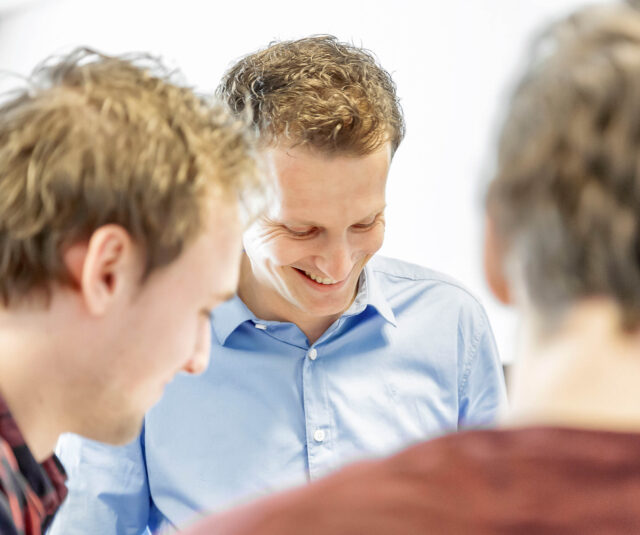
Fueled by a team of specialists who are passionate about guiding you to find the perfect parts and consumables for your equipment and production needs.
WHAT HAPPENS AFTER BUYING A MACHINE?
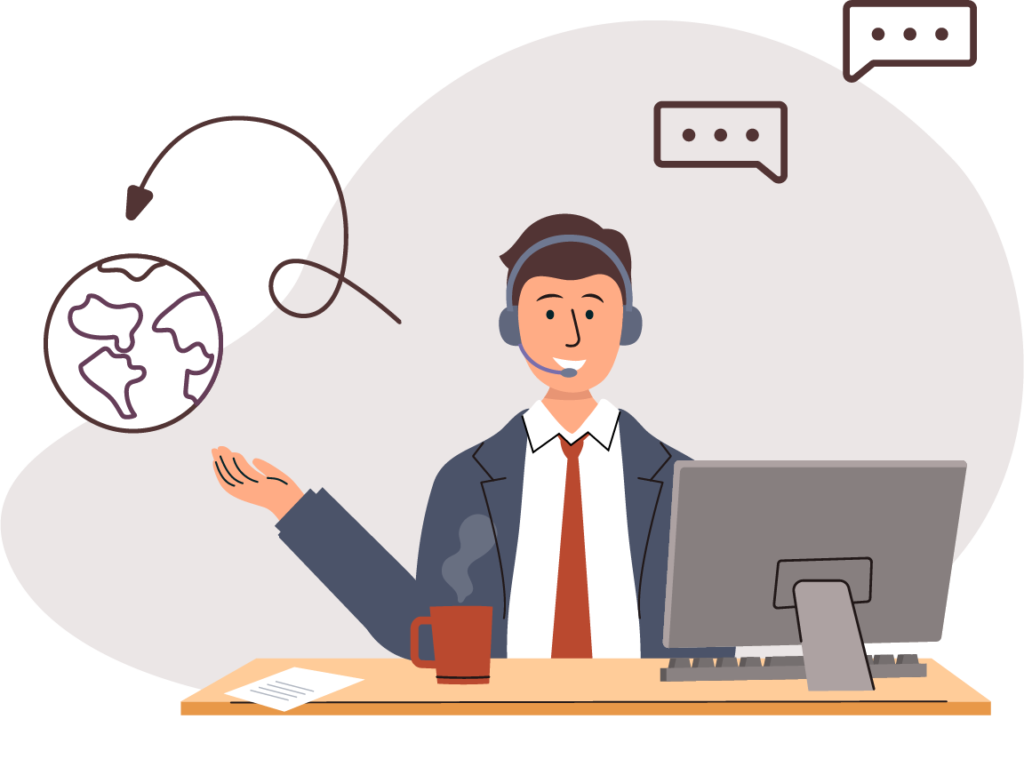
SINGLE POINT OF CONTACT
Building strong personal connections is a top priority for us, which is why we assign you a dedicated point of contact for all future events after purchasing a machine. Your trusted contact will handle everything internally, ensuring clear, efficient communication.
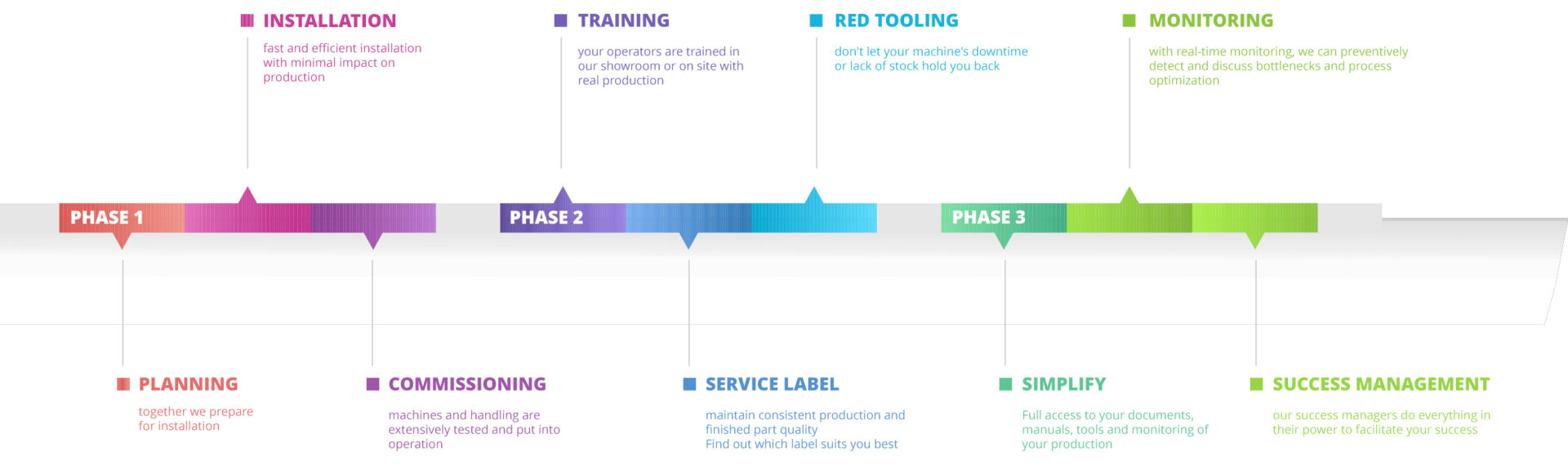
WE WANT YOU PRODUCING WITH MAXIMUM UPTIME
Unlock the true potential of your Voortman machine with skilled operators. While our machines are highly automated, the expertise of an operator is essential for optimal performance. Our intuitive software handles complex programming and offers ease of use, but a deep understanding of logistical flows and efficient production is still crucial. Don't settle for anything less than trained employees who can maximize efficiency and output. It's about overcoming the industry's biggest challenge: attracting and keeping top talent. We understand the struggle - you're not alone.
MAXIMIZE YOUR SKILLS WITH OUR ONLINE AND ONSITE TRAINING MODULES
Introducing our
customized program that caters to machine operators' experience and
availability. We provide training options on-site or at the Voortman Experience
Center. The benefits of training at our center include undivided attention and
a distraction-free environment. Our comprehensive operator training covers
Software, Application, and Operation. For Voortman plate cutting machines, we
also offer specialized SigmaNEST training for optimal software usage on plate
processing machines.
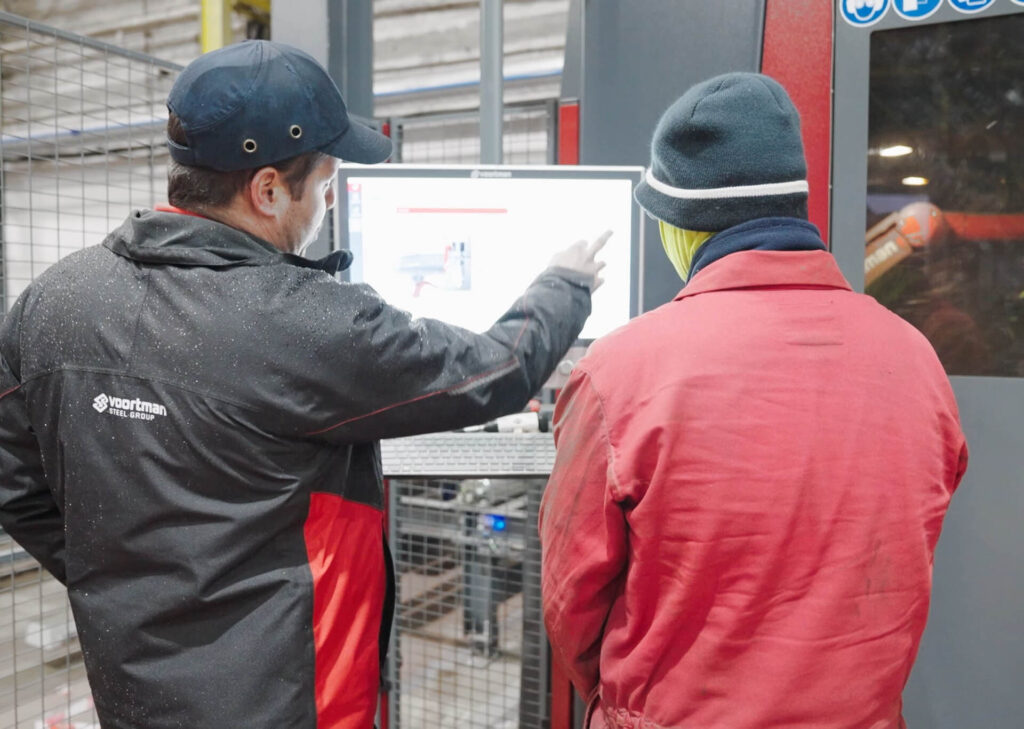
PREVENT FROM RUNNING OUT OF STOCK WITH OUR RED TOOLING SYSTEM
Are you tired of wasting time searching for the right tools to complete your job? Don't let your machine's downtime or lack of stock hold you back. Time is money, and the quality of your end product relies on the tools you use.
Introducing the RTS, a stock cabinet that ensures you have all the necessary tools and consumables for your business operations. With the RTS-system's smart software, you can easily monitor and maintain your stock levels from your office. When it's time to replenish your stock, we'll be there to assist you with our automatic ordering process. You'll always have the tools you need to keep your machines running smoothly and ensure the continuity and quality of your production process. Focus on delivering the best quality without worrying about interruptions or delays.
KEY BENEFITS AT A GLANCE
- Maintain stock levels
- Increase processing up-time
- Ensure product quality
- Centralize tools locations
- Always the right tool
- Fully automated ordering
- Gain insights with dashboarding
- Combine with Service labels
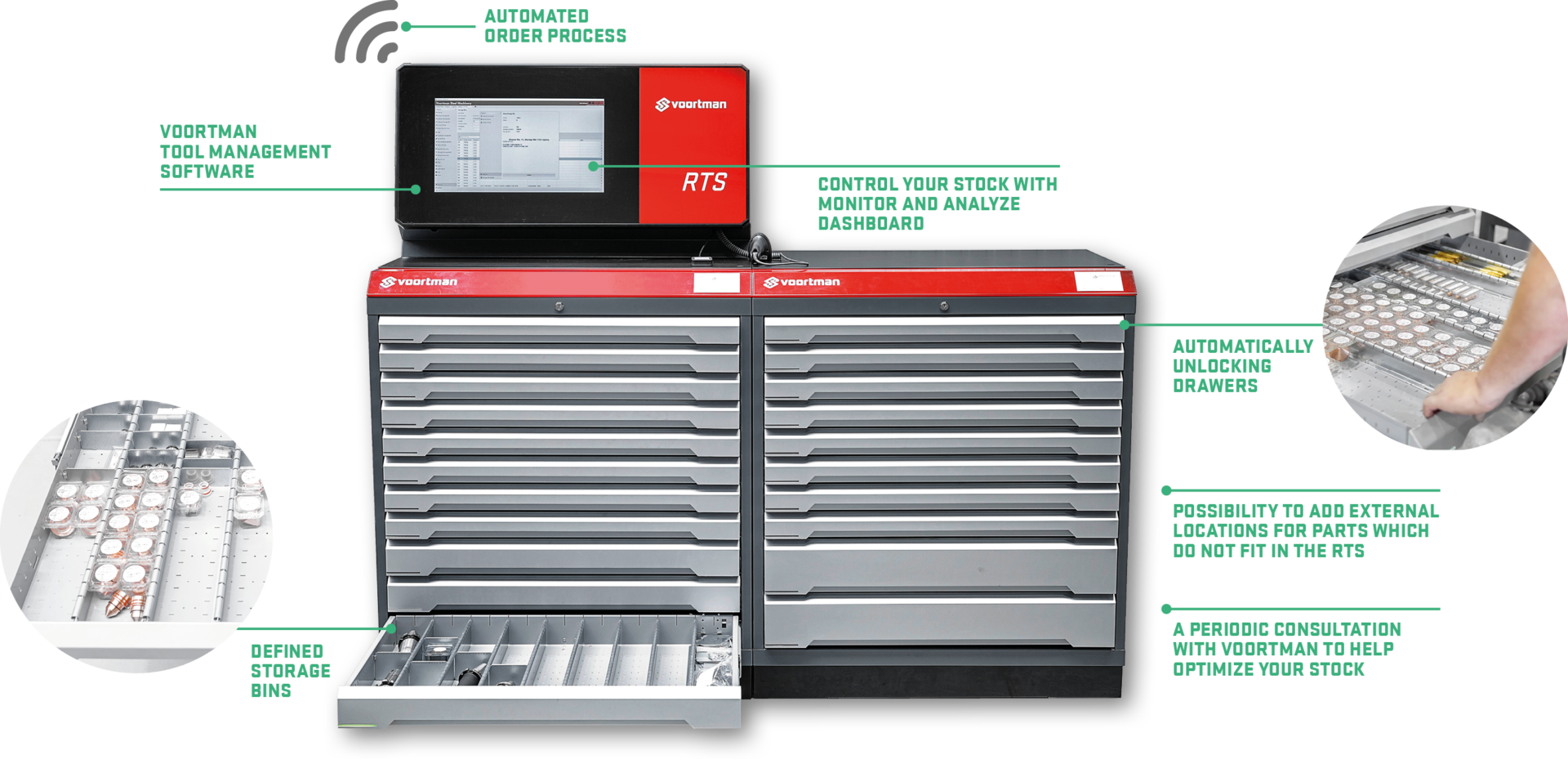
EXTENDED VOORTMAN INSIGHTS (EVI)
OPTIMIZING MACHINE PERFORMANCE AND PRODUCTIVITY
Stay informed, empowered, and productive with EVI. Wherever you are and whatever state your machine is in, EVI keeps you connected. Whether through the convenient EVI app on your mobile device or tablet, or by logging in to the EVI webpage on your laptop, staying in the loop has never been easier.
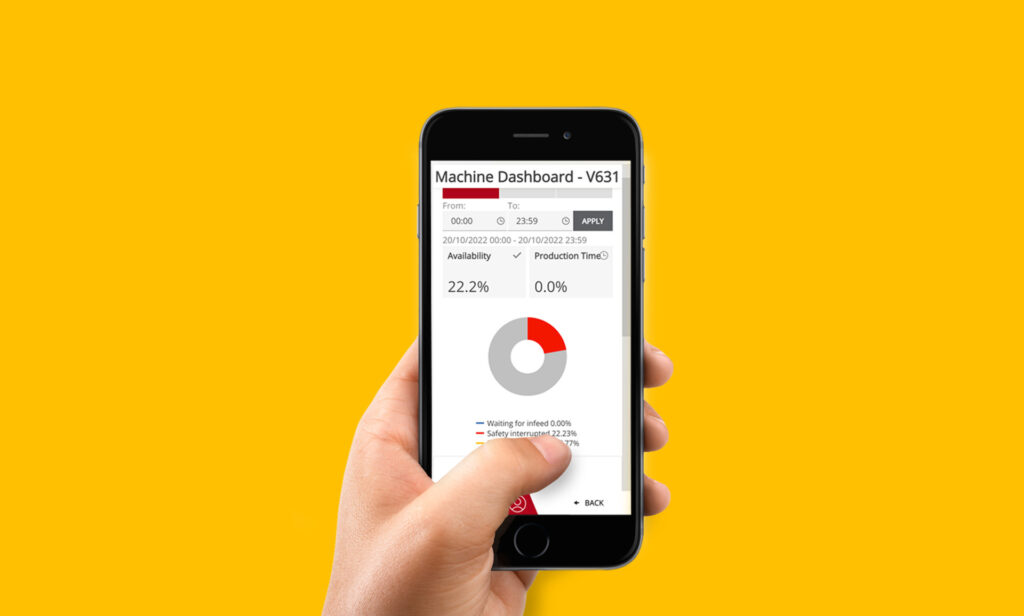
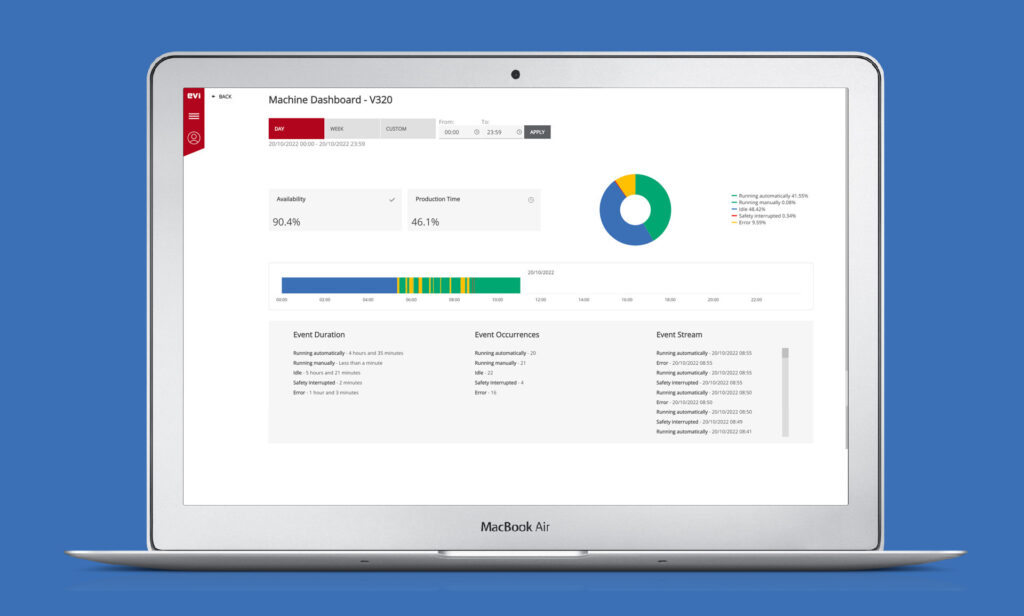