- Shot blasting
- Beam
- MSI
- Plate
- Fabrication
Automatic shot blasting: getting a clean steel surface
A clean steel surface
Shot blasting is a process which is used for steel profiles and steel plates to clean your steel surface before it is painted or welded. Shot blasting removes any metal oxide, mill scale and other contaminants from your steel surface, which is necessary for a reliant adhesion of a primer or paint afterwards. Instead of getting your steel surface optimally finished in a manual time-consuming way, Voortman provides the shot blasting process on the automatic Voortman VSB Range shot blasting machine. This machine is built on the wheel blasting principle, which means that an electrical driven turbine converts electric energy into high speed blasting with abrasive to clean your material. At a maximum speed this turbine can shot blast a 275 kg amount of abrasive per minute. These large amounts of abrasive ensure that your steel surface is cleaned with the best results at a very high speed, saving you a significant amount of time and increasing your efficiency.
After the steel surface is shot blasted, the steel is cleaned by a brush-/blow off unit, whereafter the abrasive is collected and any dust is filtered. The abrasive with the contamination from the steel is cleaned in a separator.
Shot blasting in an entire production line
Voortman’s VACAM control software takes care of all processes in the shot blasting machine, as well as all material transport in and out of the machine.
Furthermore, Voortman’s MSI (Multi System Integration) ensures a seamless connection of the VSB shot blasting machine with other equipment such as the sawing machine (VB Range) and the drilling machine (V613 / V630 / V631)
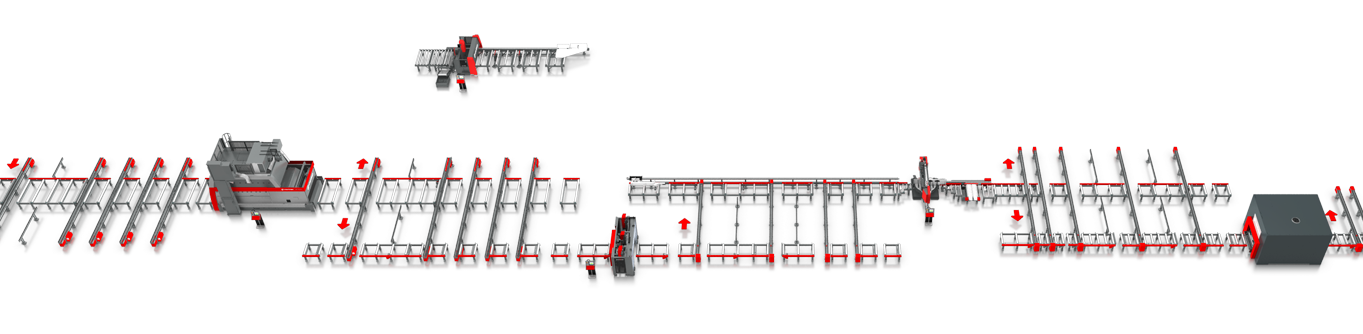