HOW FAST CAN
YOU GET MATERIAL FROM A - Z?
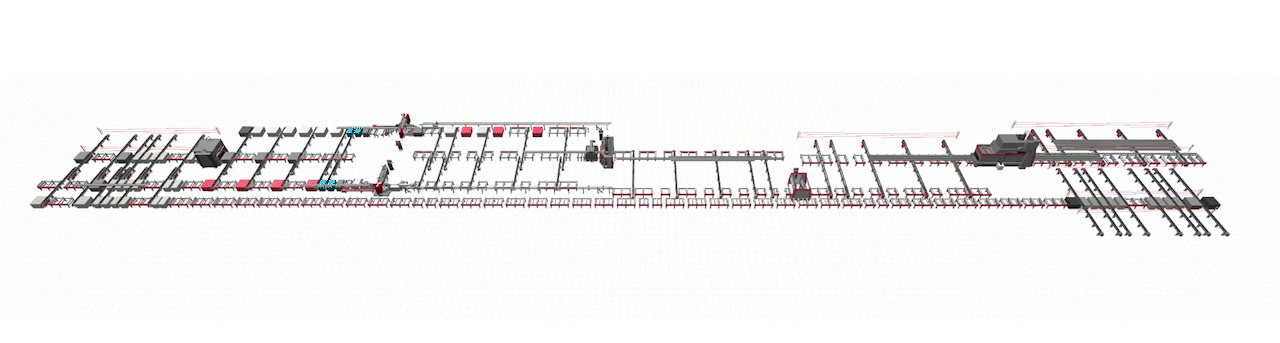
Very fast and efficient - as you can see...
With a Voortman profile processing line packed with high-quality hardware and intelligent software, a door opens to fully automated production and intra-logistic processes. We call it Multi System Integration. Machines are seamlessly connected via our VACAM-software, cross transports, roller conveyors, product buffers and material sensors. Time-consuming material movements and bottlenecks are eliminated and complicated logistics are a thing of the past. Raw lengths go on the infeed, and fully processed products come off the outfeed. Machines communicate with each other and each machine is capable of producing unmanned for long periods—a single operator can oversee several machines at once.
Thanks to our intelligent buffer management, the system is able to work autonomously for long periods of time with maximum throughput. Our VACAM software knows where which profiles are in the line and our load balancing principle optimizes the material routing through the line for maximum efficiency. Simply let the system do the work and reap the benefits of Voortman's MSI and solutions.
When the profiles have been processed with high speed and efficiency, this efficiency continues at the unloading section of the line by means of our Smart Unloading. At a glance, your operator sees on a large screen all the information (e.g. lengths) needed to sort processed profiles quickly and correctly. Less error-sensitive and a lot more efficient!
Some of our high-impact solutions for your business
Blast and paint profiles to perfection!
In many simulations carried out at reputable steel distributor, there's a VSB Shot blaster included in the profile processing line. The VSB Shot blaster is one of the most automated blasting machines on the market. With Voortman's unique batching functionality, profiles are automatically positioned at the correct distance and spacing from each other. 6 turbines with automatically adjustable grid radius reach all sides of the material. There is no need for extensive knowledge or manual adjustments. Our software recognizes all essential parameters for the blasting process and adjusts automatically.

How about a complete blasting-painting system?
If your production data and our data-driven analysis shows that a lot of material needs to be painted, the optimal lay-out can be extended by placing a Voortman VP Range Painting machine directly behind the VSB Shot blaster. This complete surface treatment line saves a considerable amount of space, time and money. Speaking of cost savings, the Voortman VP automatically detects the material and only sprays when material is present. The automatic height adjustment also ensures that the process is highly accurate, which results in perfectly blasted and painted profiles. The infeed and outfeed of the entire blasting-painting system is fully automatic, allowing your operator to focus solely on loading and unloading profiles.
Rainham Steel is running at full capacity
A major steel distributor in the UK
Rainham Steel, a major steel distributor in the UK since 1973, is committed to meeting its customers' demands in a timely and complete manner. With this in mind and the need to increase capacity, the company invested in a Voortman MSI line. A shot blasting and painting line combined with a drill-saw, blasts, drills and cuts profiles to length in full automation. Now that the system is running at full capacity, Rainham can take on more jobs than ever before and is even looking to expand further!
Designing a perfect fit!
To get to such an optimal lay-out with maximum efficiency, we use a data-driven approach combining your input and requirements with real data while keeping future expectations into account. Let's see what this lay-out design looks like!
Our data-driven approach
YOUR REQUIREMENTS!
The first step in the process is where we sit down with our customer to discuss requirements and restrictions for specific processes, workflows or logistical improvements.
ANALYZING YOUR NEEDS
Our next step is to determine how many machines the customer requires, based on current production, but also including future expectations. It's important to understand what kind of operations a system will have, so we can tailor its design.
COLLECTING PRODUCTION DATA
To determine the most ideal machines and processes, we work with existing production data from a complete year of production.
DATA ANALYSIS & CONFIGURATION
With the
chosen machines and processes, the next step is to design a lay-out where all
machines fit within the given space and correct loading and unloading zones. We
believe that all movements in between these points must be automated.
PROOFING LAYOUT
Using simulation software as a digital twin helps us identify bottlenecks in the system. We put real production data into a virtual reality simulation in order to check the functionality in different scenarios and identify areas that delay production. By resolving these areas, we can increase the capacity of the whole system.
TAILORED PROPOSALS
The requirements, constraints and data analysis ultimately lead to multiple proposals. With these proposals we start discussing with a final design as a result.
THE OPTIMAL LAY-OUT
The outcome is the most optimal simulated and designed profile processing line fully packed with high-quality hardware and intelligent software.
Curious what your optimal lay-out with maximum processing efficiency looks like? Then challenge us!
LET'S DESIGN THE OPTIMAL LAYOUT
Let us automate your intra-logistics processes, increase efficiency and gain valuable insights. From start to finish - our consultants work with you and challenge you to find the best solution to increase your productivity. What else are you waiting for?