- Plate
- Plasma
- Cutting
- Drilling
- Manufacturing
- Fabrication
- Automation
When can you improve your output with drilling vs. cutting holes?
Different variables affecting time
Do you know the ideal conditions for drilling vs. thermal cutting holes when producing holes in steel? The time it takes for plasma cutting holes in mild steel is predominantly affected by the thickness of the material and the hole size, while the time to drill holes mainly depends on the machinability and thickness of the material.
Both drilling and cutting are viable processes to create holes and each has certain application ranges where one is faster than the other. Let’s go through some examples in mild steel to get an idea of the time difference between drilling and cutting holes. This can help you lean towards one process or the other based on your specific production details.
Small holes? - drilling preferred
Drilling vs. cutting comparison: 14 mm | 9/16" & 22 mm | 7/8" hole diameters in 12 mm | 1/2" thick material
https://youtu.be/YTB0-ZDCcos
There are issues with plasma cutting quality when the hole diameter is smaller than the material thickness, so drilling is almost always preferred. Even from a time perspective, drilling is usually faster than cutting for small holes. For hole diameters smaller than 2x the thickness of the material, the cutting speed needs to be decreased to reduce hole taper to a minimum. Generally speaking, plasma cutting small holes increases processing time, while drilling small diameter holes can decrease the time it takes to produce your parts.
Thick material? - drilling preferred
Drilling vs. cutting comparison: 26 mm | 1" & 32 mm | 1-1/4" hole diameters in 25 mm | 1" thick material
https://youtu.be/h6znaml7stE
Thick materials need to have very large hole diameters in order for thermal cutting to be better from a time and quality standpoint. You can see from the video that time differences appear quite small per hole. However, in large nestings those small seconds can add up to significant time savings over the course of a full day of production. All additional options (such as clamping the plate or height sensing) are also included in the comparison.
It’s also important to note that a large number of holes usually means less space between each hole and less height sensing sequences with plasma cutting. The total difference for an entire nest could be less than just the difference between each hole, as the plasma torch can reduce the number of height-sensing probes needed during overall production.
Large variations in hole diameter? - plasma cutting preferred
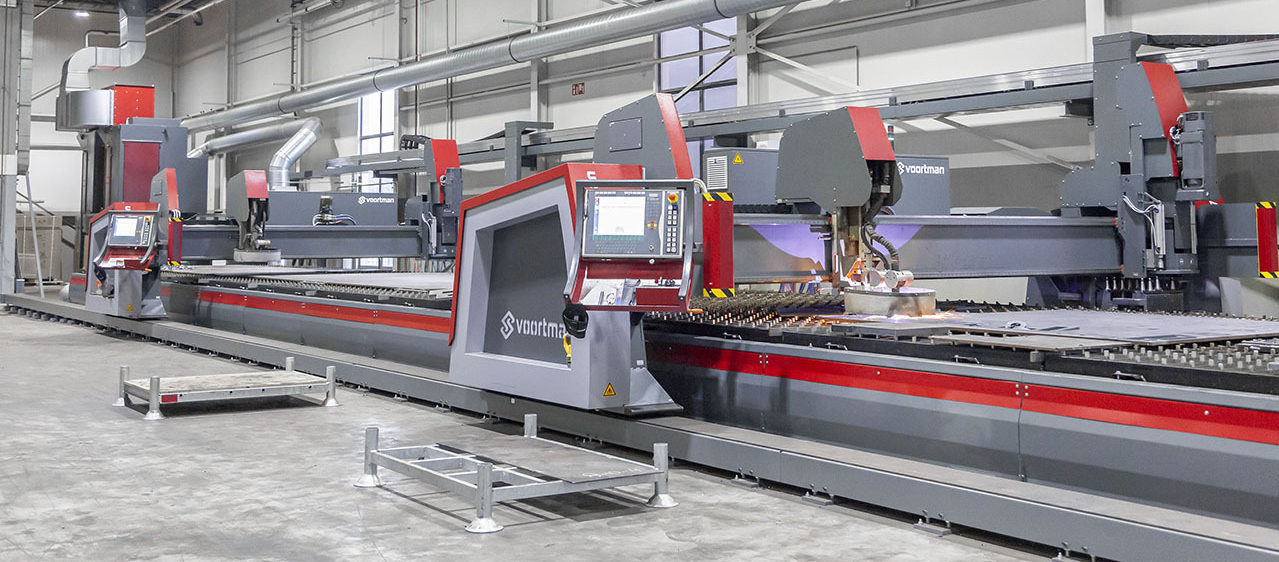
There are many reasons companies decide to plasma cut holes instead of drilling. If the part has many different hole diameters to produce, then drilling time increases because of the amount of tool changes required. Every machine also has a maximum number of tools it’s able to automatically change out without manual intervention.
The time difference in absolute values are quite small and there is a break-even point where the number of different diameters and tool changes required counteracts the time savings gained by drilling instead of cutting holes. For example: in 12 mm/.5-in thick material with an average 18 mm/.75-in hole diameter, the break-even point is estimated to be that a tool change is needed for every 10 holes drilled.
Compared to older technology
It’s important to mention that this is not a full overview of drilling vs. cutting. New technologies like pierce detection, increased average hole speed and reduced initial height sensing are the latest innovations present in Voortman plasma cutting machines and have led to reduced cutting time compared to drilling in some cases. Cutting holes with an older plasma model will show increased cutting time over newer models with today’s latest plasma technology.
Better machine design = better output
These time comparisons are heavily influenced by machine design. A low-end machine will likely have lower feed rates that affect drilling time significantly. Voortman ensures only the best quality components are used in the robust plate processing machine range, so you can drill and cut holes quickly without compromising the quality required for the project. Interested in our combined plate drilling and cutting machine solutions? Take a look at our new V310 and the V320 and V325. Interested in cutting only? Then the V303 or V304 plasma cutting machines might be interesting to explore!
Certifications, restrictions and desired output
Drilling versus cutting is compared here purely on output. One or the other process can also be preferred based on quality requirements. Comparing these two processes based on quality will be done in a different article so make sure you keep yourself posted and choose a process that fits your application the best!