Voortman V325
Heavy plate drilling, cutting & milling (passthrough)
With a massive drilling head and 20-station automatic toolchanger, the Voortman V325 is a must-have heavy plate drilling, cutting and milling machine. It’s capable of processing thick plate steel up to 100 mm (4”) and drilling holes up to 70 mm (2-3/4”), saving you time compared to milling large diameter holes in heavy plates. Rapidly increase your capacity and level of automation with features like automatic part removal, automatic deburring, 3D plasma bevel and oxy-fuel 4.0 cutting. You can count on the V325 to be the workhorse your production facility needs to grow.
Heavy plate drilling
Drilling and milling thick plates
DRILLING DIAMETER UP TO 70 MM (2-3/4") PLUS EXTENDED MILLING CAPABILITIES
The V325 is equipped with a massive SK50 / CAT50 drilling head. The powerful 610 Nm torque spindle effortlessly drills holes up to 70 mm (2-3/4”) with carbide, and optimized milling adds the capabilities to mill even larger slots and other openings. Dual 10-station tool changers can be loaded with 20 tools with various applications to provide a vast array of common processes like drilling, thread tapping, counter sinking and counter boring.
PROCESSING THICK PLATES WITH 3D BEVEL PLASMA AND OXY-FUEL
Process steel plates up to 100 mm (4”) thickness with the V325 drilling, cutting and milling machine’s massive drilling unit, 3D bevel plasma system and revolutionary oxy-fuel torch.
High quality & automation
Automatic underside deburring & automatic part removal
REDUCE SECONDARY OPERATIONS WITH AUTOMATIC DEBURRING
Deburring is an important part of the workflow in order to meet current quality standards and produce products that are immediately available after processing. The V325 comes equipped with an automatic deburring unit, which can reduce total costs per part up to 30% versus running deburring and edge finishing operations on precision parts manually. The deburring unit also help extend drill lifetime, since you don’t need to replace drill consumables with the first signs of burr from worn down drills. Products are ready for immediate handling without risk of injury from burrs.
AUTOMATIC PART REMOVAL CONVEYOR
Finished parts are dropped from the skeleton using an automatic product discharge table with a motor driven conveyor belt to further automate material handling. The Voortman V325 can run independently longer without requiring part removal by an operator. Nesting bridge cuts can save even more processing time by discharging entire rows of parts to the conveyor together.
High Productivity
Optimized cut-to-cut movement & reduced risk for downtime
INSTANT CUT TECHNOLOGY
The V325 is equipped with Voortman’s breakthrough Instant Cut Technology. It was developed to reduce cut-to-cut idle movements by ensuring optimized motion paths each time the torch moves from one operation to another, doubling production capabilities. Time savings exponentially increases when production consists of small product with holes, as each time the torch moves position between cuts you’ll save valuable seconds that will add up to meaningful increases in production in a short amount of time. Instant Cut Technology is built in to VACAM control software, which creates the optimal production mix between speed and quality automatically.
EASY TORCH REMOUNTING WITH 3D COLLISION
The V325 comes equipped with a unique magnetic torch collision system. When a torch collides with an object such as a cut-out product on the table, remounting the torch usually takes some time, and some designs even require spare parts. The Voortman 3D torch collision system minimizes downtime with easy magnetic torch remounting to get your machine up and running in no time.
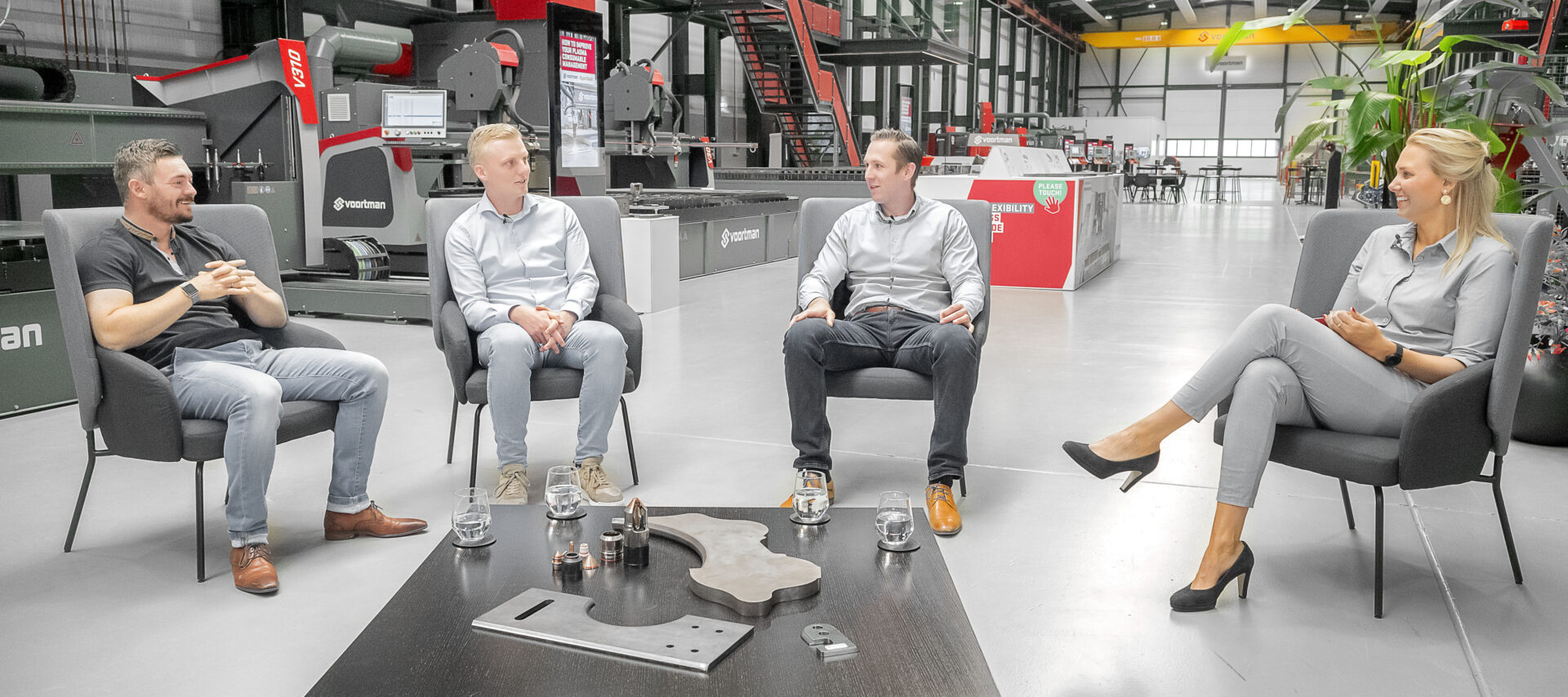
WEBINAR / Voortman & Hypertherm
HOW TO IMPROVE YOUR PLASMA CONSUMABLE MANAGEMENT
Finding that sweet spot for changing consumables is key, isn't it? In our webinar with Hypertherm, we discussed various topics related to improving plasma consumable management. Our experts shared actionable insights and clever strategies that you can immediately apply to your daily operations. Get ready to take your plasma consumable management to the next level with our webinar recording!
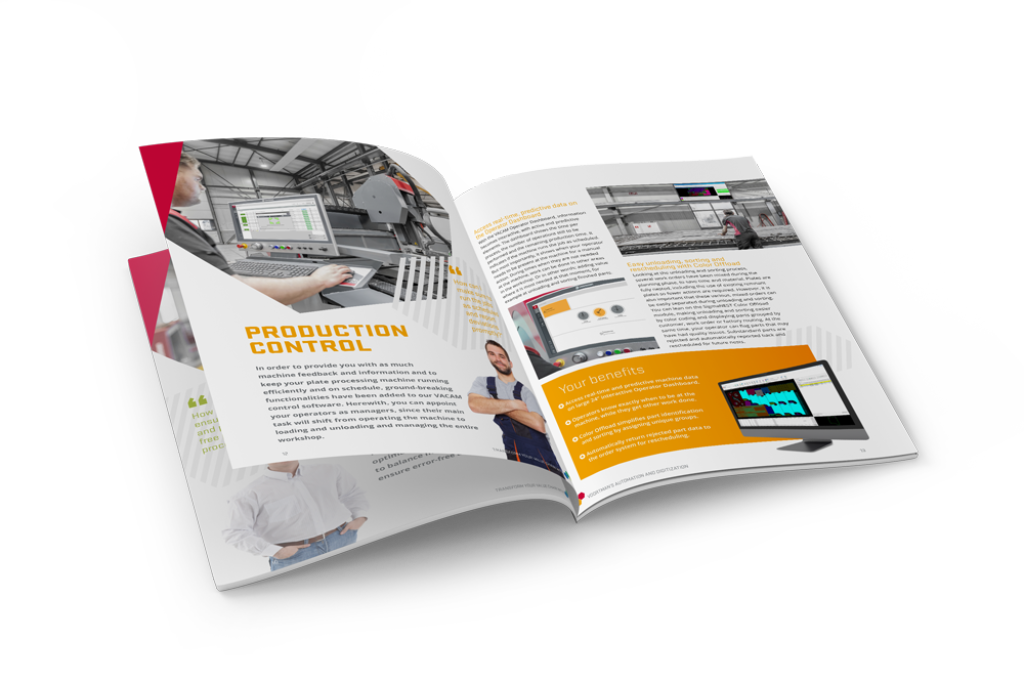
IN-DEPTH BROCHURE / Plate processing
Transform your value chain with Voortman's automation and digitization
Although our plate processing machines already provide remarkable optimization, you can also make strides in other areas of your business. By implementing automation and digitization, you can optimize your entire production process from work preparation to finished product, eliminating unnecessary elements and bottlenecks. See how Voortman and SigmaNEST's digital solutions enable you to gather, connect and analyze real-time data effectively, so you can make powerful decisions leading your business forward with confidence.
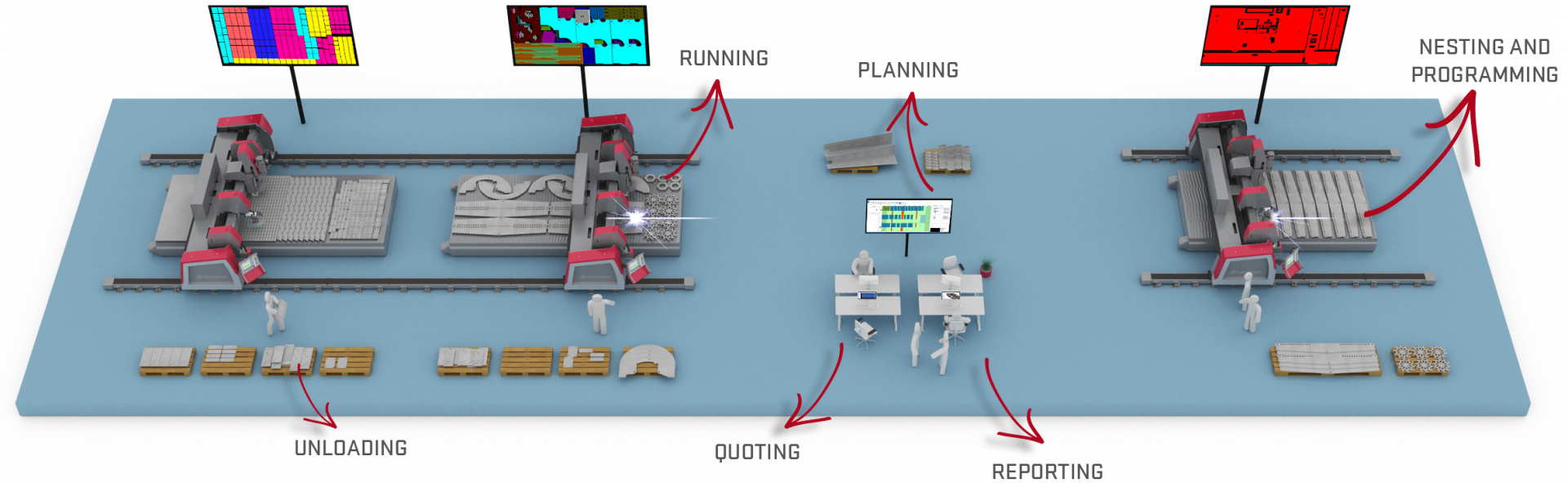
Integration in your workshop
Quoting
Generate quotes more effectively, faster and more accurately
Companies in the manufacturing industry as well as in steel fabrication benefit from quick and accurate quotations. The Quoting module gives you as a company an indication of how much work you expect to have in the future, but also which materials you need to have in stock, who your regular customers are and how many orders you may receive.
Voortman offers a simple quotation module whereby you can convert a quote to a work order without any effort. This module offers advanced functionalities with which quotations can be generated more effectively, faster and more accurately. Additionally, a CRM database is available where outstanding quotations can be followed up per customer. SigmaNEST, with Voortman machine processing information, automatically calculates processing times and allows for customizable costing calculations for any part or secondary process. This allows you to draw up an accurate customer-specific quotation based on your quick and exact cost price calculation!
Nesting and programming
One nesting solution that supports all your machines
An excellent nesting program is almost as important as the machine itself. That is why all Voortman plate cutting machines are equipped with one of the most advanced nesting software programs available: SigmaNEST. Together with Voortman, SigmaNEST offers a wide range of modular and customizable functions to get the most out of your production processes. This automatic nesting software is installed on an office computer after which it is used to import files and nest them automatically into standard sized or remnant plates.
The software offers the possibility to import the most common file formats in the metal industry. The CAD import module can be added and used to directly import native formats to ensure all the information is maintained and duplicate work will be eliminated. SigmaNEST generates specific CNC-outputs for the machine, which will be converted to all required operations via VACAM software. Streamline your production process and get ready-made parts out of your machine with this nesting software!
Planning
Nest more efficiently & save time and material
All machines and associated machining programs can be read in a graphically displayed calendar timeline and managed from this central dashboard. This makes it possible to assign work orders to a specific machine automatically or manually based on type of operation, such as drilling and/or cutting or based on capacity. This planning tool enables optimum productivity through proactive machine scheduling and load analysis tools!
When Load Manager is used in conjunction with the Color Offload module, schedules are updated in real time to accurately reflect shop floor status and the operator can see what the next job is. Workflow optimization is guaranteed!
Running
Track progress and meet deadlines
Once the planning has been made, programs are sorted in the planning queue by program number, material type or thickness, machine and estimated run time and then production is started by the operator. When the program has started, the machine gives the operator instructions for correctly assembling the tools and consumables. Technologies such as cutting parameters, drilling parameters and milling parameters are fully integrated into our proprietary VACAM software and are automatically applied based on the information in the program. Therefore, the operator can focus on the manual operations around the machine.
The estimated machining time is displayed and the planning is updated when the module is running, allowing you to make a forecast of production per day, week or month. It becomes directly visible when a certain program starts or stops and the next one begins, what the capacity of your production is, whether certain programs still need to be split, whether deadlines can be met and whether outsourcing is the best option.
Unloading
Easy unloading and real-time tracking
In the planning phase, several work orders have been co-mingled which saves time and material since nesting is done more efficiently. Plates are fully nested, including the use of existing remnant plates so fewer actions are required. However, it is also important that these various, mixed orders are able to be easily separated during unloading. The Color Offload module is an intelligent tracking and offloading solution that eliminates operator confusion by displaying nested parts in colors that can be assigned by customer, work order or factory routing.
In addition, information is provided to the operator such as part details or dimensions so the operator is able to do a direct quality check before parts move on to the next work station. When a part has been cut wrong because, for instance, consumables fail, the operator can select and reject parts in the nesting software program. This information can be fed into Color Offload and the part automatically reappears in the work order list in the nesting program, enabling it to be remade.
Reporting
Create full integration with MRP/ERP systems and other software packages
SimTrans is an online transaction manager that bridges the gap between different software systems from CAD/CAM nesting to shop floor automation to other business systems (MRP or ERP). SimTrans makes it possible for you to work with industry standard database formats (SQL), interfaces or CSV/TXT file interfaces and makes the set-up with an MRP/ERP system fairly simple and standardized.
SimTrans enables you to obtain the right information from different software systems at different moments in the process by means of a continuous mutual data flow. All data generated in SigmaNEST can be send back to MRP/ERP packages. Data such as estimated processing times, estimated processing costs, plates used, waste rates and status updates about programs. This automation allows constant work order tracking through real-time updates and feedback. But also vice versa, if changes in work orders, stocks, delivery times or customer information are made in the MRP system, these data are automatically updated in SigmaNEST.
Specifications
Voortman V325 | ||
---|---|---|
Voortman V325 | ||
Operating range | feet | 10 x 20 |
feet | 10 x 30 | |
feet | 10 x 40 | |
Thickness | inch | 1/4-4 |
Positioning weight | lbs | 20,000 |
Drilling and positioning | Servo motors | |
Positioning speed X | f/min | 98-1/2 |
Positioning speed Y | f/min | 88-1/2 |
Positioning speed Z | f/min | 59 |
Marking | milling/plasma | |
Drilling and plasma 3D bevel units | 1 | |
Maximum torque drill head | lbf*ft | 450 |
Speed drill head | rpm (stepless) | 0 - 3,500 |
Tool changer | 2 x 10 | |
Drill holder | CAT50 | |
Drill diameter | inch | 13/64 - 2-3/4 |
Thread tapping | M6 - M36 | |
Plasma | up to (amp) | 400 |
Oxy-fuel | 1 | |
Machine weight (base) | lbs | 31,000 |