FLEXIBLE PLATE CUTTING AND MARKING
In a compact area
Looking for a compact yet flexible plate cutting and marking machine packed with thoughtful features? Then we would like to introduce you to our Voortman V303 and V304. These twin machines offer identical features and benefits, but with one key distinction: the V304 enables multi-oxy torch cutting, from 3 to 6 torches.
Both machines feature next-level VACAM Software that automates plate production and provides plenty of real-time feedback. With the
largest touch panel available in the market and a user-friendly interface,
operators can effortlessly navigate through the entire cutting procedure. Our
focus remains on delivering exceptional quality while minimizing manual
intervention, ensuring maximum efficiency. Thanks to the "Xtensive Bevel
Cutting technology," even the most complex bevel cuts are now fully
automated, eliminating manual corrections or pre-cutting, saving you time and
effort. These are just some of the many benefits of the V303 and V304. Keep
scrolling for more remarkable capabilities!
MEET THE MOVING-GANTRY PLATE RANGE
Voortman presents a diverse selection of moving-gantry plate processing machines, designed to meet various production requirements. Discover the range, compare supported processes, and select the ideal machine to accomplish your processing objectives.
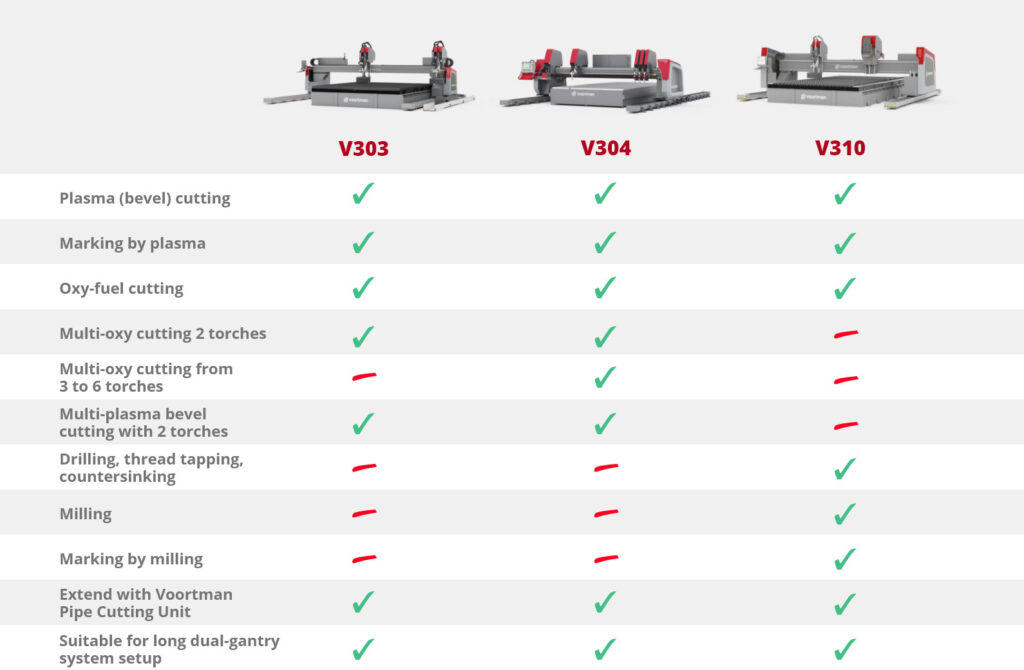
UNLOCK THE POWER OF MULTI-OXY TORCH CUTTING
With the Voortman V304
Ever thought about boosting your production with multiple oxy-fuel torches? Meet the game-changer – the Voortman V304! As the proud sibling of the V303, the V304 shares all similar renowned specifications, but with a twist – it allows for multi-oxy operation from 3 to 6 torches, bringing a plethora of benefits.
1. INTERACT WITH YOUR MACHINE
A perfect synergy between machine and shopfloor
In order to provide you with as much machine feedback and information and to keep your plate processing machine running as efficiently as possible, some ground-breaking functionalities have been added to our VACAM control software. Herewith, you can appoint your operators as managers, since their main task will shift from operating the machine to loading and unloading and managing the entire workshop. How? Read more below!
Optimize your entire production process
A perfect fit with SigmaNEST modules
All new functions on the V303 and V304 that contribute to more interaction and feedback, align very well with existing SigmaNEST modules. Using SigmaNEST advanced nesting solution in combination with Voortman machines, allows you to optimize your whole fabrication process from work preparation to end product thus improving your business profitability. Let’s dive somewhat deeper into the specific SigmaNEST modules and the benefits you gain from it.
2. GUARANTEED THE HIGHEST POSSIBLE QUALITY
Without manual intervention
With the new 'Xtensive Bevel Cutting technology', even the cutting of complex bevels is fully automated and require no manual correction or even pre-sample cutting. Combined with our Dross Inhibitor, for minimizing slag during piercing, TrueVolt Technology and Xtensive Hole Technology, the V303 and V304 are able to cut the most complex products fully automatically. Driven by experience and innovation.
ADD-ON / Voortman Pipe Cutting Unit
Increase flexibility by adding our Voortman Pipe Cutting Unit
Easy to integrate and add to your existing or new V303, V310 or V304 plate processing machine.
BEST CUTTING QUALITY
IN THE MARKET
EASILY INTEGRATED
AND USABLE
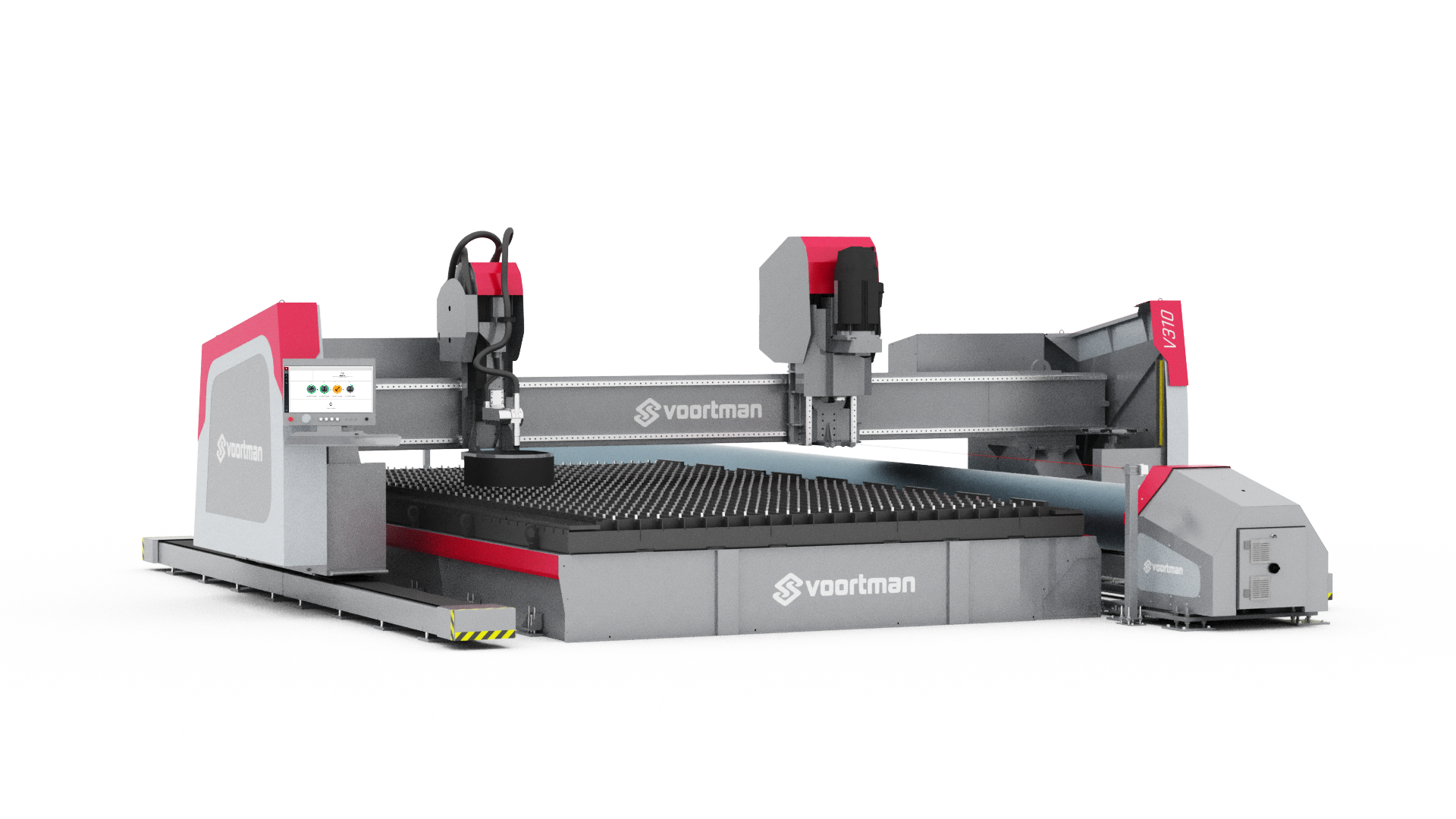
SAVE TIME
ON LOGISTICS
LESS DEPENDENT
ON SUPPLIERS
3. MAKE THINGS EASY
For your shop floor manager
Of course, there are still times when your shop floor managers notice that they have to perform manual operations on or around the machine. In that case, let's make it as easy as possible for them. Think of easy loading and unloading due to the low machine X-rail, easy cleaning of the cutting table due to Voortman's in-house developed cutting table and much more.
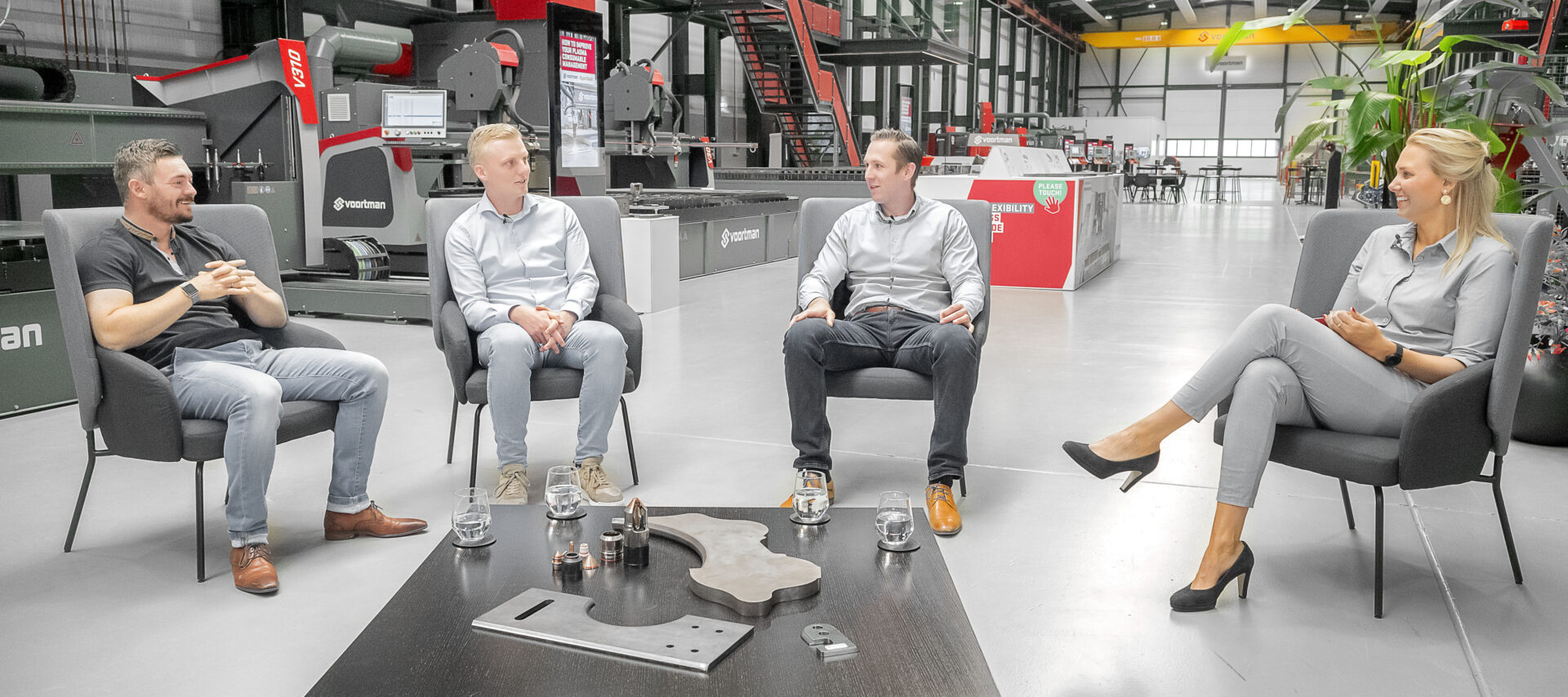
WEBINAR / Voortman & Hypertherm
HOW TO IMPROVE YOUR PLASMA CONSUMABLE MANAGEMENT
Finding that sweet spot for changing consumables is key, isn't it? In our webinar with Hypertherm, we discussed various topics related to improving plasma consumable management. Our experts shared actionable insights and clever strategies that you can immediately apply to your daily operations. Get ready to take your plasma consumable management to the next level with our webinar recording!
4. MAXIMUM UP-TIME AND CAPACITY
You are in full control
This machine enables you to support and streamline manual operations as well as possible. You will experience the shortest possible downtime with little or no influences on the cutting process and product quality. Our customer service experts are at your disposal 24 hours a day and we also offer many options to prevent possible downtime. Because all our gantry moving plate cutting machines use the same X-rails, it allows you to combine or run different processes simultaneously. There will always be a match with your desired capacity.
Specifications
Voortman V303 and V304 | |||
---|---|---|---|
Voortman V303 | Voortman V304 | ||
Working width | feet | 6 - 10* | 6-16* |
Working length | feet | 13 - 100* | 13 - 100* |
Cutting speed | f/min | 0 - 23 | 0 - 23 |
Rapid traverse speed | f/min | 65 | 65 |
Max. cutting thickness | inch | 1/8 - 8 | 1/8 - 8 |
Max. number of plasma (bevel) torches | 2 | 2 | |
Max. number of oxy-fuel units | 2 | 6 | |
* Wider width and longer lengths available on request |
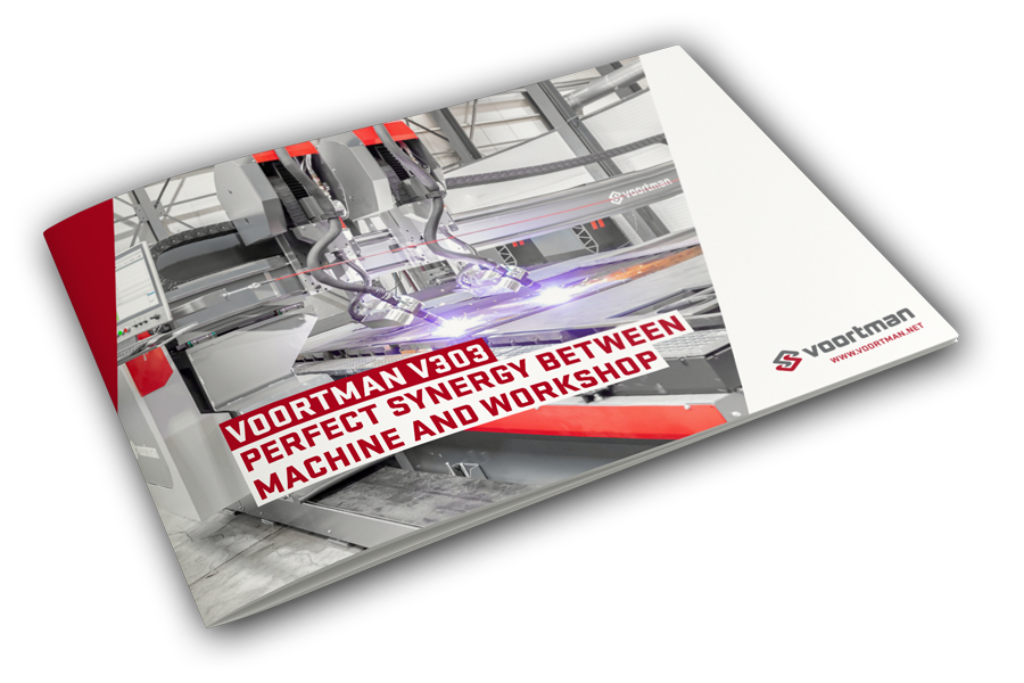
PRODUCT BROCHURE / V303
Interested in getting a quick overview of what the V303 is all about?
IN-DEPTH BROCHURE / Plate processing
Transform your value chain with Voortman's automation and digitization
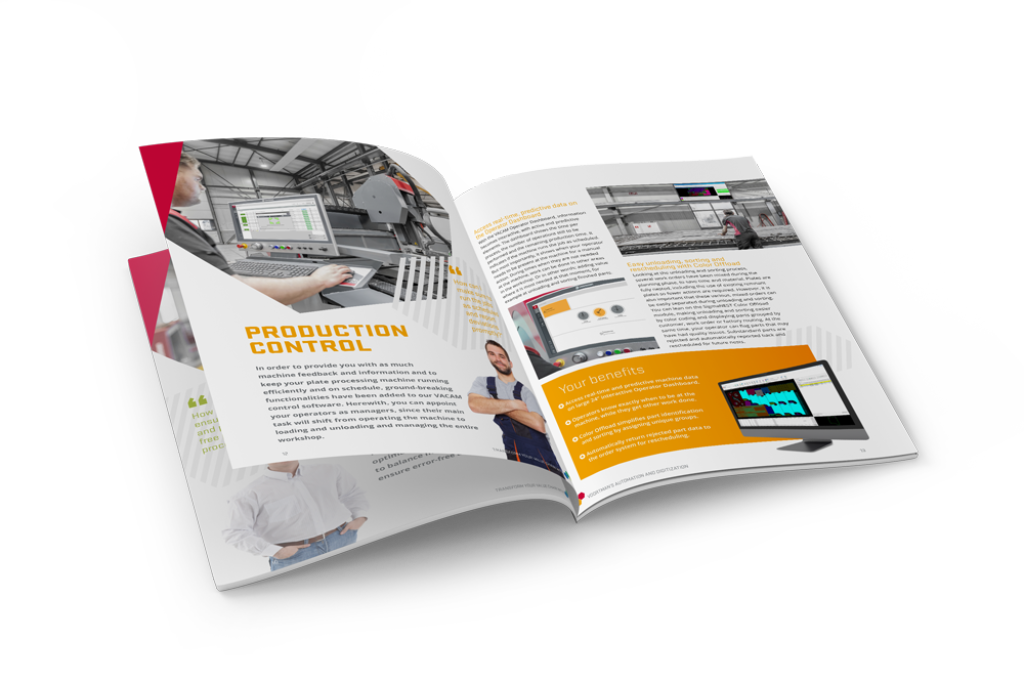