Multi System Integration
Fully automated integrated production line
MSI, also referred to as Multi System Integration, opens the door to fully automate your production by connecting machines with cross transports, roller conveyors, product buffers, and material sensors. Production data only needs to be imported once and then MSI automatically distributes the data to all machines integrated in your production system. Manually transporting materials through the production line is a thing of the past by creating one integrated production system. Equipped with VACAM, our own operating software that is installed on each machine, you gain the ability to track and monitor your entire production process in real-time.
Read moreAn Introduction to a Smart Factory
We specialize in designing and installing fully automated production lines across the globe, incorporating high-quality hardware and cutting-edge software. Our Multi System approach ensures that machines are seamlessly connected via our VACAM software, cross transports, roller conveyors, product buffers and material sensors.
But what does smart factory really mean? How are material flows set up and what choices are made based on analyzed data? Let's take an up-close look at fully automated production in this real smart factory!
Automated Material Handling
Reduced labor costs & increased efficiency due to automated material handling
The integration of automated material handling within an MSI machine line offers significant cost savings for structural steel fabricators. Skilled labor is increasingly hard to find, and it can be costly adding operators to your production process. MSI aims to reduce the number of manhours needed per ton produced to a minimum with built-in smart production algorithms in our own VACAM control software. Every Voortman machine runs on the same software and syncs with the master CNC controller, allowing your material to be rerouted and directed remotely without any manual intervention.
When first seeing a complete Voortman MSI production line, steel fabricators are often surprised at the large amount of material that is moving through the system with only a few people overseeing production. Customers quickly realize how the complete system is necessary for them to remain competitive and reduce their overall cost per ton.
The movement of materials is not just expensive but also time-consuming, potentially leading to bottlenecks in the production line. Relying on cranes to shift material from one machine to another is an inefficient practice. With MSI seamlessly connecting machines together in a fully automated system, several of your operations can be performed simultaneously, increasing production efficiency while reducing your man hours.
Below is an example of what an advanced automated production line looks like!
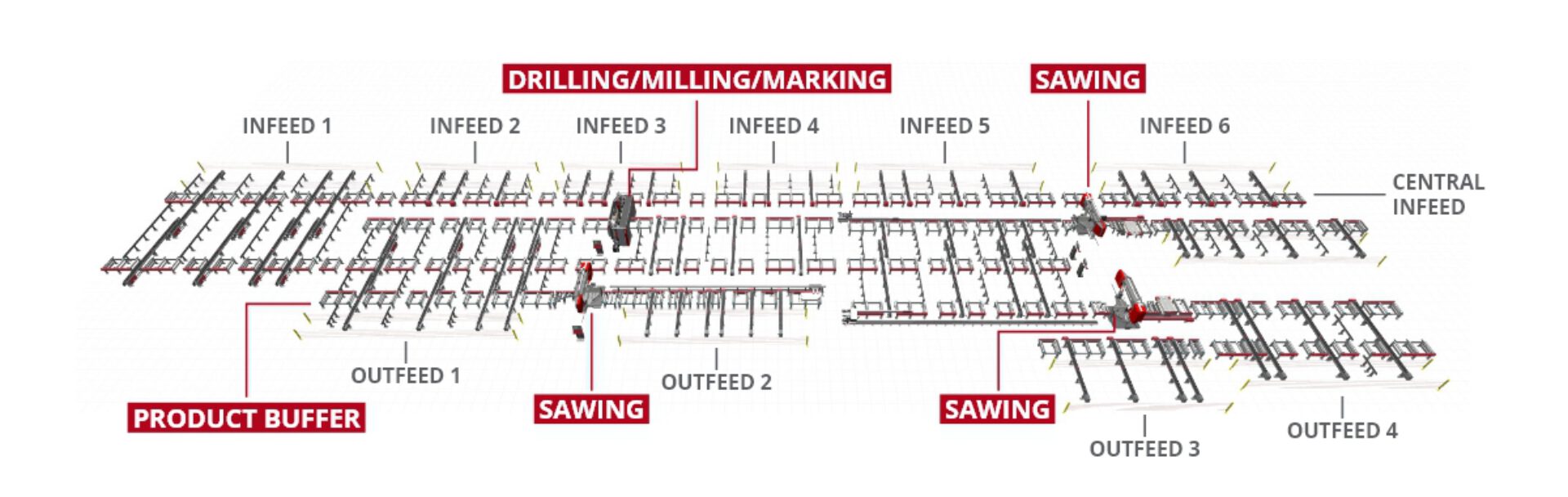
High flexibility in creating your optimal beam processing layout
Combining your input and requirements with real data to create your optimal design
Steel fabricators often face challenges like insufficient capacity, lack of manpower or limited facility workspace. By integrating a customized beam line tailored specifically to serve your business model you can significantly lower overhead costs while improving your overall efficiency, all achieved through Multi System Integration (MSI). Voortman uses a customized data-driven approach to determine the best layout and configuration of an automated beam line tailored specifically to serve your business model. The process begins with identifying the most effective layout for beam processing tailored to your unique requirements.
Every business is unique and an optimal layout depends on many factors. Everything is considered during consultation – the processes you perform, the types of profiles, your product lengths, your workshop space availability and your desired output to name a few. Voortman is very flexible and capable of customizing an optimal beam line layout in the most efficient way possible for every scenario. The modular build approach is used, which means more flexibility in processing sequence.
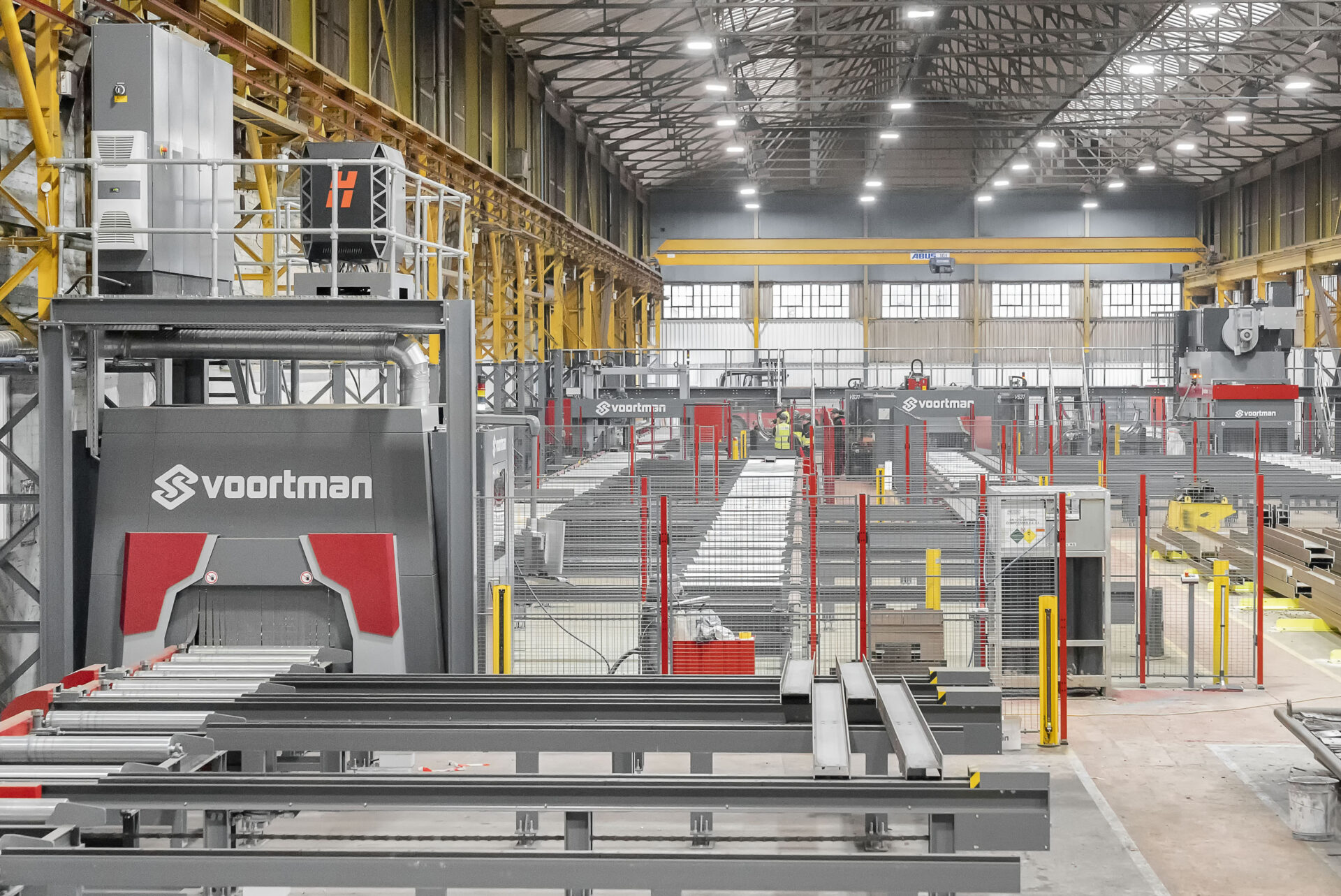
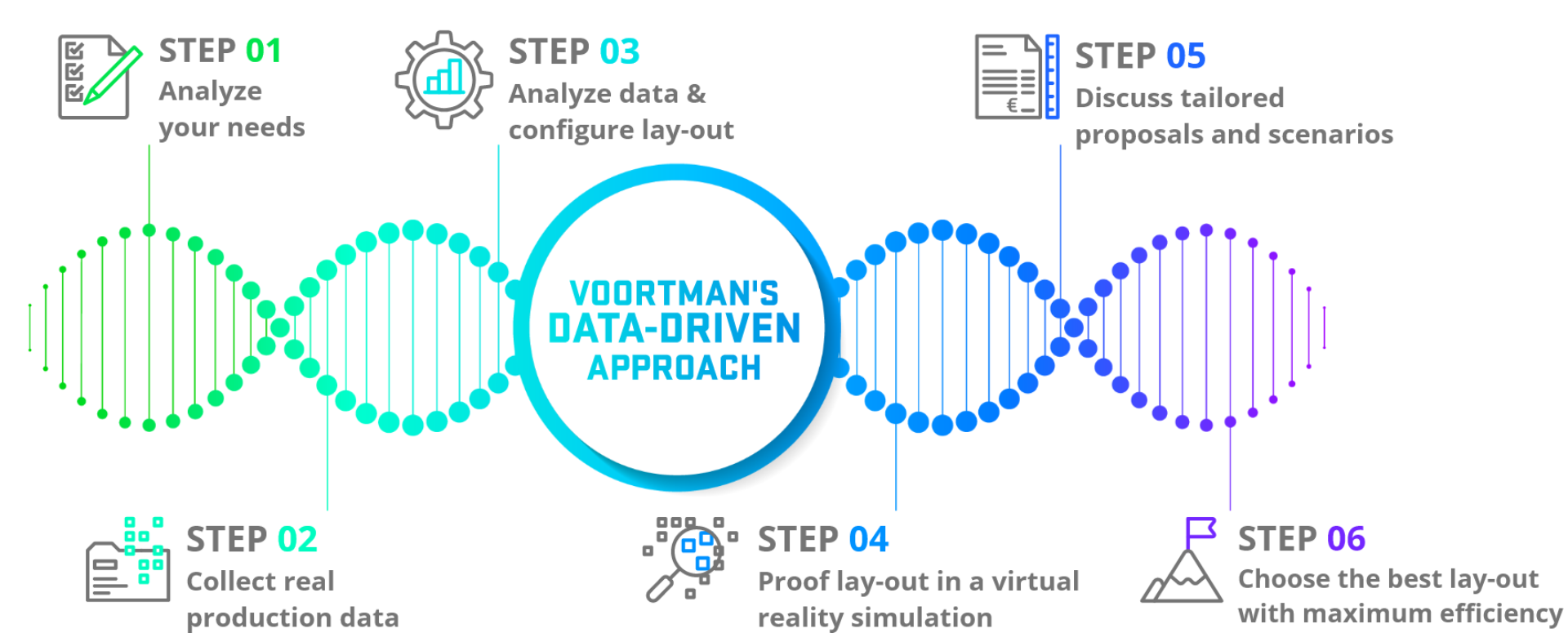
Our Data-Driven Approach
To get to such an optimal lay-out with maximum efficiency, we use a data-driven approach combining your input and requirements with real data while keeping future expectations into account. Let's see what this lay-out design looks like!
Finley Structures Embraces Efficiency
Finley Structures, a United Kingdom company based in County Durham, has recently undergone commissioning and training for their new Voortman automated machine line. The company has invested in the latest technology and equipment to ensure that their production process is as efficient as possible. The new machinery includes a unique U-shaped system that was specifically designed to fit within the available space at the company's facility. The system is fully automated, with a built-in infeed and buffer system for multiple outfeed zones. Raw profiles are cleaned using the Voortman Shot blaster, then processed with the three-axis Voortman V631, which can also handle milling to reduce the workload on the V807 robotic coping machine. The profiles are cut to length with the Voortman Bandsaw, including the removal of short pieces, and finally, the profiles are finished with the all-in-one Voortman V807.
"The decision for the U-shaped system, which is unique to Voortman, was to enable us to have the key elements that we required, and also because of the existing space that was available. When we had a look at other systems that were available, they couldn't make it work within the area that we had. So Voortman again came up with the best solution."
JULIE RAISTRICK, MANAGING DIRECTOR OF FINLEY STRUCTURES
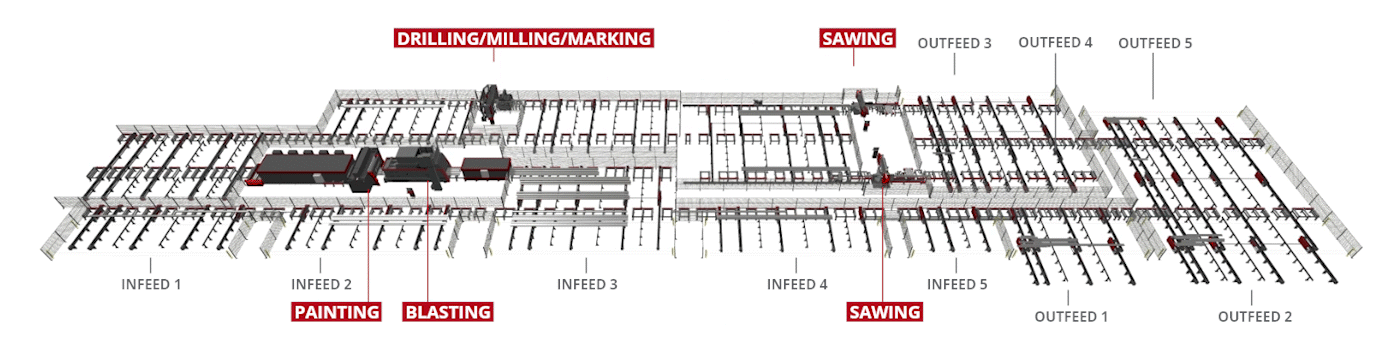
Integration in your workshop
MSI Layout 1 - Leading global steel distributor
This example shows the layout of a leading global steel distributor. This advanced Voortman production line consists of five machines: two identical VB series sawing machines, the Voortman V631 drilling and milling machine and the blasting and painting line consisting of a Voortman VSB series and VP series. The creation of this highly efficient production line was the result of an in-depth analysis of their production data and product assortment. Voortman undertook the design and assessment of various configurations to achieve an optimized layout that facilitates the streamlined processing of steel beams, profiles, and bar steel.
The process begins with profiles undergoing full automatic blasting and painting, after which they are directed either towards the Voortman V631 for detailed drilling and milling or straight to one of the two VB series saws, both equipped to handle short piece removal efficiently. This operation is part of a seamless workflow where profiles are already buffered and automatically transported to the next machine in the line or to one of the outfeed locations. Once there, the Smart Unloading screens significantly speed up the sorting and shipping process by easily displaying which profiles are ready for shipment to the customer. The complete line ensures product traceability, allowing them to remain "in control" at all times and guarantee reliable delivery times.
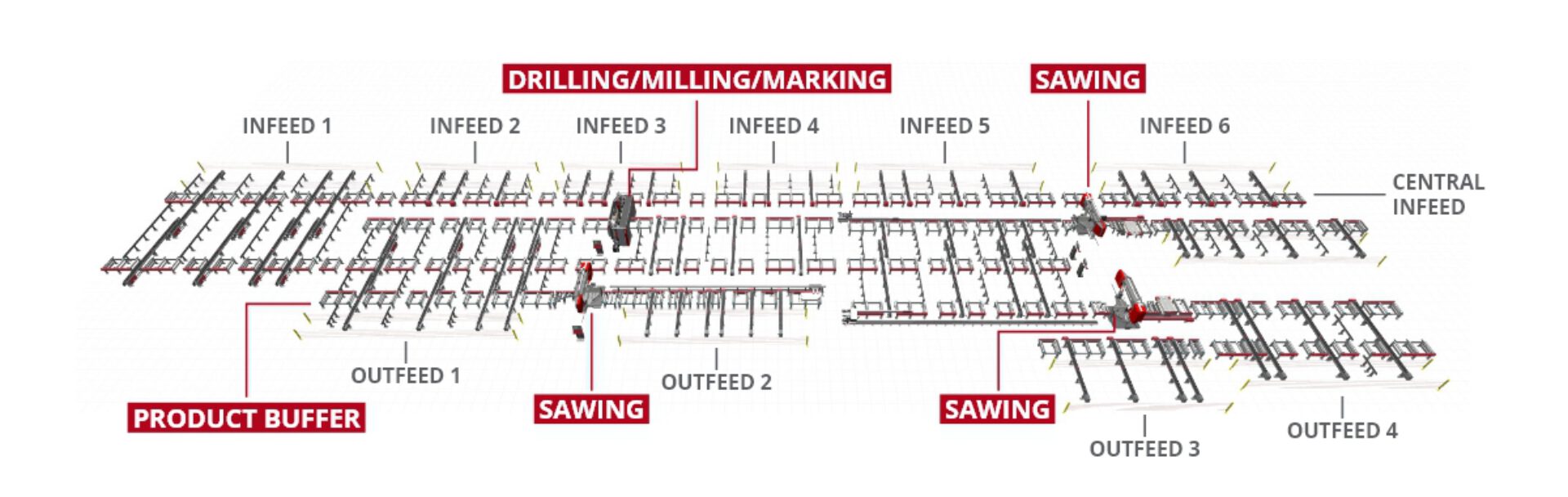
MSI Layout 2 - Large steel service center
This example shows the layout and configuration at a large steel service center. Recognizing the need for optimization, a team of experts has successfully developed a highly efficient layout that enables the loading of profiles from six different halls onto various infeed zones. This innovative design revolves around strategically positioned infeed and outfeed locations, as well as the seamless integration of specialized machinery and streamlined processes.
The Voortman V631 drilling and milling machine and Voortman VB1250 band saws with an automatic short piece removal system effectively perform their tasks. Additionally, a dedicated route incorporating the Voortman VB1250 band saw featuring a backstop system, enables high-volume profile- and bundle cutting. Time-consuming material movements, bottlenecks, and complicated logistics are eliminated. With intelligent buffer management, load balancing principles, and efficient routing, the system can operate autonomously for extended periods, ensuring maximum throughput. Moreover, the sawing capacity has doubled twice and crane capacity is used more efficiently. The substantial increase in output marks a significant advancement in the logistics process, resulting in fast lead times and enhanced competitiveness – from stock to finished product.
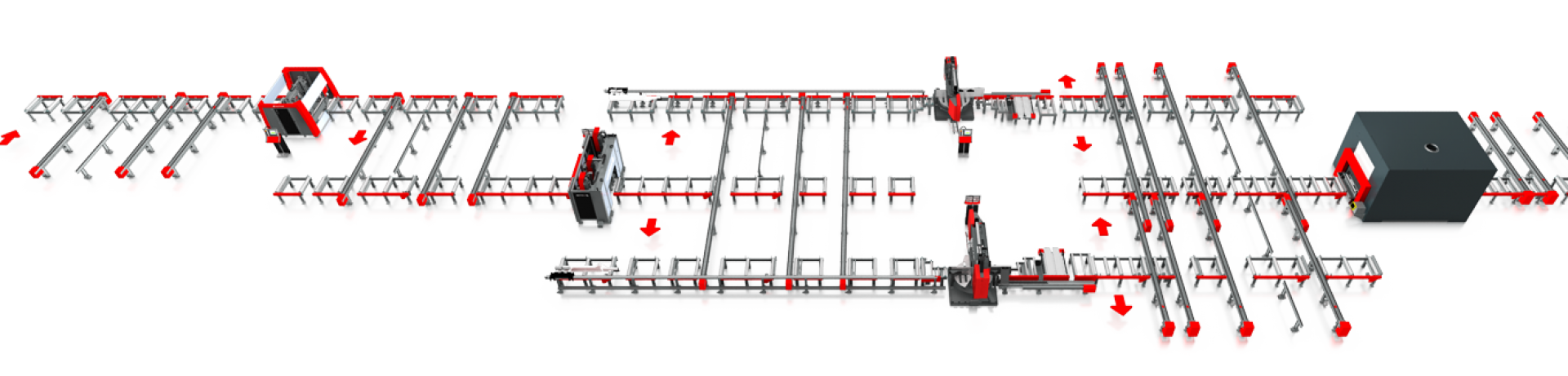
MSI Layout 3 - Large Steel Fabricator
This example shows the layout and configuration at a larger steel fabricator. Voortman's analysis showed that this customer had a lot of marking work in their production, so a separate V704 marking machine was recommended for the layout. This strategic move allows the V704 to focus on marking profiles, which are then forwarded to either the V630 or V631 for drilling operations. Positioning the two saws somewhat further down the production line instead of the beginning has the advantage of being faster by requiring fewer front measurements. Full-length raw beams can pass through the marking and drilling units without needing to stop for measuring.
The analysis further revealed that this customer performs a higher-than-average number of saw cuts, making a strong case for investing in a highly automatic sawing process with two saws and a short product removal system (SPRS) based on volume. Marked and drilled profiles can be simultaneously cut to length, and short pieces are automatically transported sideways. when coping operations are required, profiles are automatically moved to the coper via infeed cross transports for further processing, such as creating copes, block outs, or preparing weld sites.
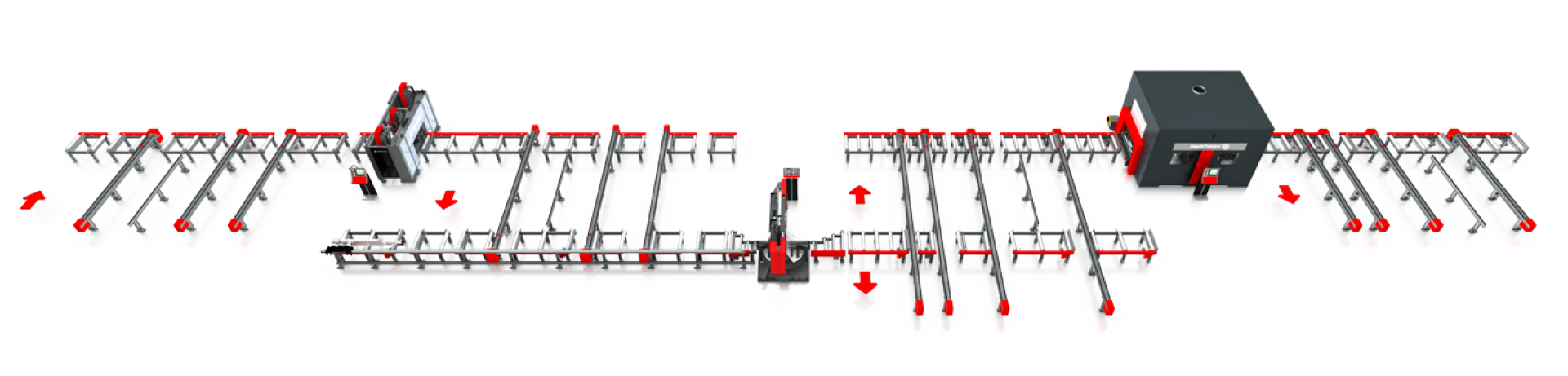
MSI Layout 4 - Medium-Sized Steel Fabricator
This example shows the layout and configuration of a medium-sized steel fabricator. In this case nested beams are marked, drilled and milled on the V630 / V631. Profiles are then automatically transported to the VB1050 saw where they are cut-to-length. Following these processes, profiles are seamlessly conveyed to the VB1050 saw for precise cut-to-length operations. Profiles that require no further processing post-sawing are automatically directed towards the right. However, When the coper is needed, profiles are automatically transported to the left and moved to the coper so copes, block outs, weld preparations, layout marking and other complex cuts are created.
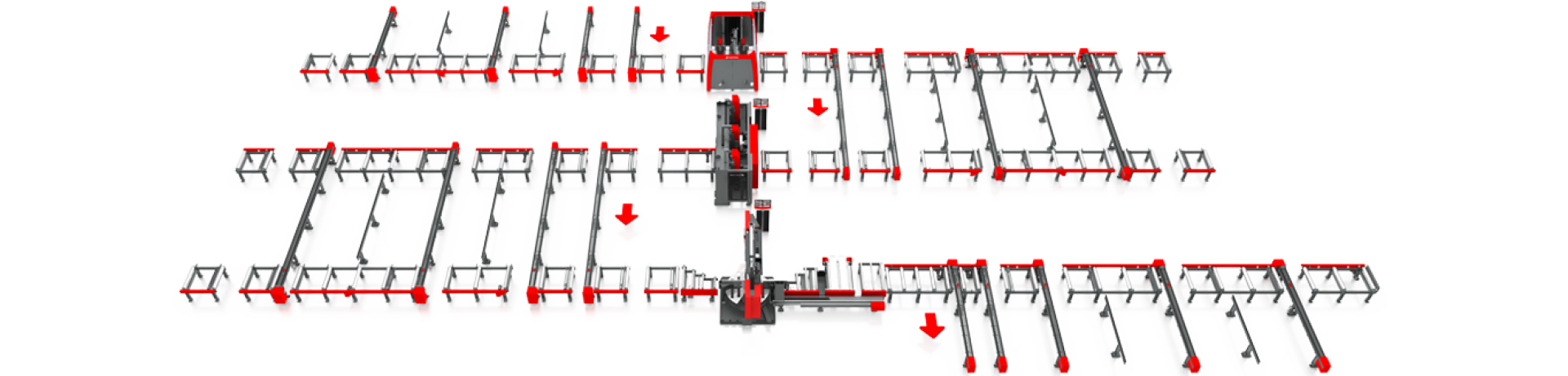
MSI Layout 5 - Small Steel Fabricator
This example shows the layout and configuration at a customer that had limited workshop floor space. Voortman designed this "double U-shape" configuration to maximize utilization of their floor space. Recognizing the client's specific needs, the inclusion of a coping machine was deemed unnecessary after a thorough analysis indicated that the volume of copes and block outs did not warrant the investment in such equipment. To efficiently manage a high volume of layout marking, the addition of a dedicated V704 marking machine was advised. This strategic decision allows the V630 or V631 drilling machines to concentrate exclusively on drilling and milling tasks, thereby enhancing their overall capacity and efficiency. The marked, drilled and milled profiles are finally cut-to-length by the VB1050 saw and automatically transported sideways on the outfeed cross transports.
A FULLY AUTOMATED PRODUCTION SYSTEM
Let's design your layout!
Let's start finding ways to reach your goals! Contact us today for a consultation with one of our experts! With decades of experience, proven solutions and our responsive worldwide service, you can Accelerate Your Performance and make a difference with Voortman and lead the way in your market!